The sintering process is a critical method in materials science and manufacturing, used to transform powdered materials into solid, cohesive structures without reaching the material's melting point. This process involves several stages, including powder preparation, compaction, controlled heating, and cooling. Sintering is widely used to create components with high precision, hardness, and toughness, making it ideal for producing complex shapes and geometries that are difficult to achieve through traditional manufacturing methods. The process is also cost-effective, enabling rapid mass production while maintaining precision and repeatability. Below, we break down the key stages and benefits of sintering.
Key Points Explained:
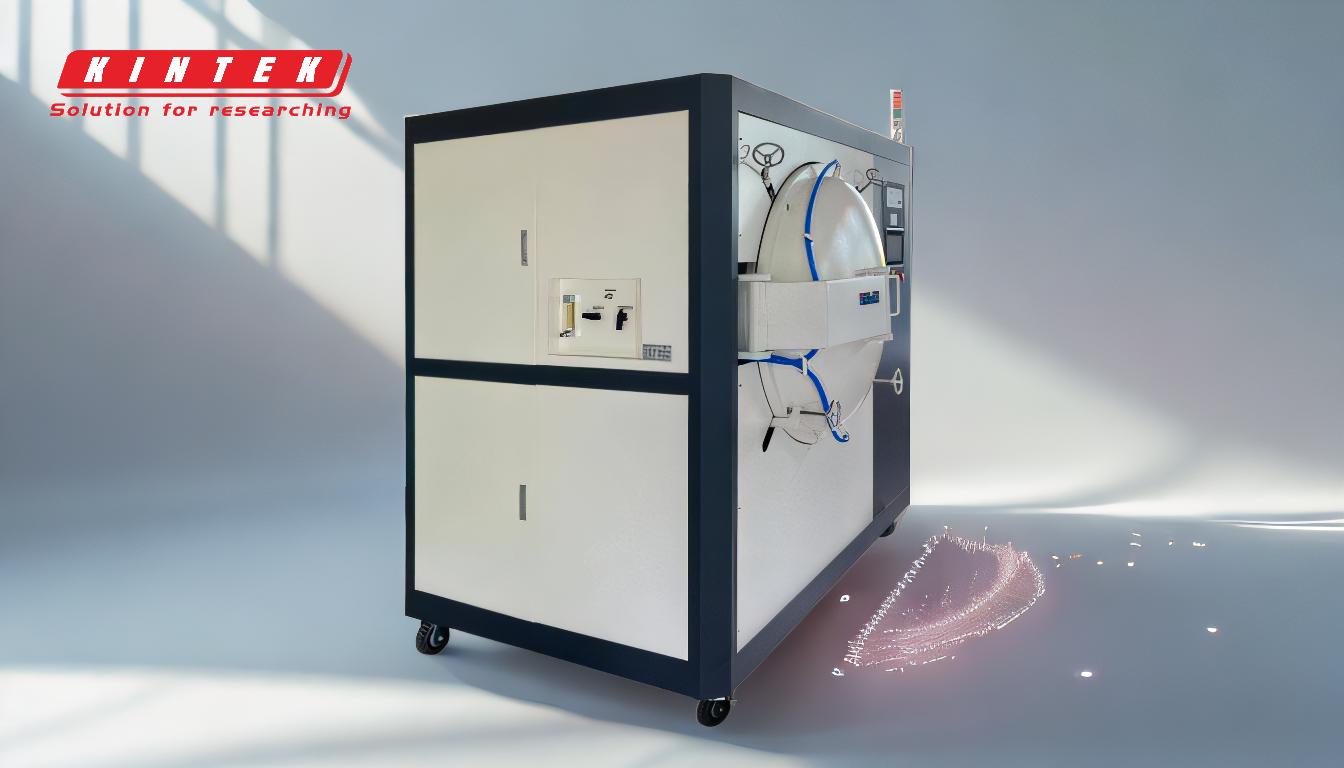
-
Preparation of the Powder Compact
- The process begins with the preparation of raw materials, typically in powder form. The powder is mixed with bonding agents such as water, wax, or polymers to help it stick together.
- The powder is then compacted using methods like cold welding, pressing tools, or 3D-printed lasers to form a "green part." This step ensures uniformity and eliminates voids in the material.
-
Heating and Consolidation
- The compacted powder is placed in a sintering furnace, where it is heated to a temperature just below its melting point. This controlled heating activates diffusion processes between particles, leading to neck formation and densification.
- During this stage, the bonding agent evaporates or burns away, and the primary particles begin to fuse at their surfaces. In some cases, intermediate bonding agents like bronze melt and couple between particles, leaving the primary material unaltered.
-
Particle Merging and Densification
- As the temperature rises, particles undergo diffusion, causing them to merge and densify. This stage can be accelerated using techniques like liquid phase sintering (LPS), where a liquid phase forms and enhances particle bonding.
- The material transitions from a porous structure to a dense, solid mass, with reduced porosity and improved mechanical properties.
-
Cooling and Solidification
- After the heating stage, the material is allowed to cool gradually. This cooling process solidifies the sintered product into a rigid and cohesive structure.
- The final product retains the desired shape and exhibits enhanced properties such as hardness, toughness, and abrasion resistance.
-
Advantages of Sintering
- Complex Geometries: Sintering enables the production of intricate shapes and geometries that are difficult to achieve with traditional manufacturing methods.
- Material Properties: It allows the combination of multiple materials, merging properties like toughness and abrasion resistance.
- Cost-Effectiveness: Sintering reduces tooling costs and enables rapid mass production while maintaining precision and repeatability.
- High Melting Point Materials: The process is particularly useful for materials with extremely high melting points, such as tungsten and molybdenum, where traditional melting methods are impractical.
-
Applications of Sintering
- Sintering is widely used in industries such as automotive, aerospace, and electronics to produce components like gears, bearings, filters, and structural parts.
- It is also employed in the production of ceramics, metals, and composites, making it a versatile manufacturing technique.
By understanding the sintering process, manufacturers can leverage its benefits to produce high-quality, durable components efficiently and cost-effectively. The ability to create complex shapes and combine material properties makes sintering an indispensable technique in modern manufacturing.
Summary Table:
Stage | Description |
---|---|
Powder Preparation | Raw materials are prepared in powder form and mixed with bonding agents. |
Compaction | Powder is compacted to form a 'green part,' ensuring uniformity and eliminating voids. |
Heating & Consolidation | Compacted powder is heated below melting point, activating diffusion and bonding. |
Particle Merging | Particles merge and densify, transitioning from porous to dense solid structures. |
Cooling & Solidification | Gradual cooling solidifies the material into a rigid, cohesive final product. |
Advantages | - Complex geometries |
- Enhanced material properties
- Cost-effective mass production
- Ideal for high-melting-point materials | | Applications | Automotive, aerospace, electronics, ceramics, metals, and composites. |
Discover how sintering can revolutionize your manufacturing process—contact our experts today!