The sintering process of advanced ceramics is a critical step in transforming a green body (unfired ceramic compact) into a dense, strong, and functional ceramic material. It involves heating the ceramic powder compact to high temperatures, typically below its melting point, to facilitate particle bonding and densification. The process is influenced by various factors such as temperature, pressure, particle size, and atmosphere, which collectively determine the final properties of the sintered ceramic. Key steps include preparation of the powder compact, binder removal, sintering at high temperatures, and controlled cooling. The goal is to achieve a low-porosity, high-strength ceramic with the desired microstructure and mechanical properties.
Key Points Explained:
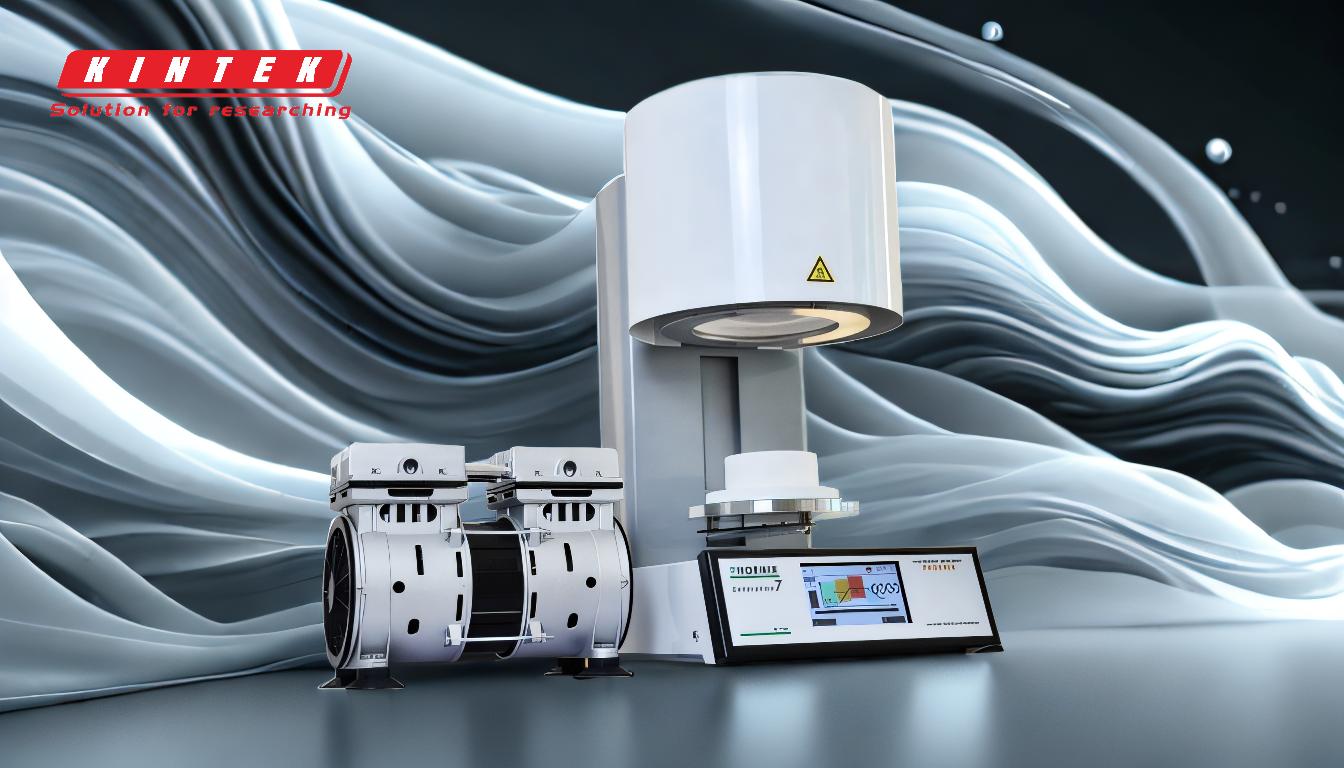
-
Preparation of the Powder Compact:
- The process begins with the preparation of a ceramic powder compact, often referred to as a green body. This involves mixing ceramic powder with binders, deflocculants, and water to form a slurry, which is then spray-dried to create a free-flowing powder.
- The spray-dried powder is pressed into a mold to form a coherent shape. The green body has a certain initial porosity, which will influence the final porosity after sintering.
-
Binder Removal (Debinding):
- Before sintering, the green body is heated at a low temperature to remove the organic binders and other volatile components. This step is crucial to prevent defects such as cracking or bloating during the high-temperature sintering process.
- The debinding process must be carefully controlled to ensure complete removal of binders without damaging the green body.
-
Sintering at High Temperature:
- The core of the sintering process involves heating the green body to a temperature just below its melting point. This high temperature facilitates particle diffusion, leading to densification and the formation of strong bonds between ceramic particles.
- The sintering temperature, duration, and atmosphere (e.g., air, vacuum, or inert gas) are critical parameters that influence the final properties of the ceramic. Higher temperatures and longer sintering times generally lead to greater densification but must be balanced against the risk of excessive grain growth.
-
Particle Merging and Densification:
- During sintering, particles densify and merge through mechanisms such as solid-state diffusion, grain boundary migration, and, in some cases, liquid phase sintering (LPS). LPS involves the presence of a liquid phase that enhances particle rearrangement and densification.
- The choice between solid-state sintering and LPS depends on the material composition and the desired properties of the final product.
-
Cooling and Solidification:
- After sintering, the ceramic is cooled at a controlled rate to solidify into a unified mass. The cooling rate can affect the microstructure and mechanical properties of the ceramic, such as tensile strength and impact energy.
- Proper cooling ensures that the ceramic retains its desired properties and avoids thermal stresses that could lead to cracking.
-
Post-Sintering Processes:
- After sintering, the ceramic part may undergo additional machining using diamond tools or ultrasonic methods to achieve precise dimensions and surface finishes.
- In some cases, ceramic parts are metallized and brazed for assembly with other components, enhancing their functionality in specific applications.
-
Factors Influencing Sintering:
- Temperature: Determines the kinetics of sintering and the final material properties. Higher temperatures generally increase densification but may also lead to grain growth.
- Pressure: Applying pressure during sintering can reduce porosity and enhance densification, especially in processes like hot pressing or spark plasma sintering.
- Particle Size: Smaller particles have higher surface energy, promoting faster densification and better sintering behavior.
- Atmosphere: The sintering atmosphere (e.g., air, vacuum, or inert gas) can affect oxidation, reduction, or other chemical reactions during sintering.
- Composition: The homogeneity and chemical composition of the ceramic powder influence sintering behavior and the final properties of the material.
-
Optimization of Sintering Parameters:
- The optimal sintering process is determined by balancing factors such as temperature, pressure, and time to achieve the desired product properties. Finer powders and higher temperatures can increase compaction, but the amount of liquid phase must be carefully controlled to avoid defects.
- The choice of sintering method (e.g., conventional sintering, hot pressing, or spark plasma sintering) depends on the specific requirements of the application and the material being processed.
By understanding and controlling these key aspects of the sintering process, manufacturers can produce advanced ceramics with tailored properties for a wide range of applications, from electronic components to structural materials.
Summary Table:
Step | Description |
---|---|
Preparation of Powder Compact | Mix ceramic powder with binders, deflocculants, and water to form a slurry. |
Binder Removal (Debinding) | Heat green body to remove organic binders, preventing defects during sintering. |
Sintering at High Temperature | Heat to just below melting point to enable particle bonding and densification. |
Particle Merging and Densification | Particles merge via solid-state diffusion or liquid phase sintering (LPS). |
Cooling and Solidification | Controlled cooling ensures desired microstructure and mechanical properties. |
Post-Sintering Processes | Machining, metallization, or brazing for precise dimensions and functionality. |
Factors Influencing Sintering | Temperature, pressure, particle size, atmosphere, and material composition. |
Optimization of Parameters | Balance temperature, pressure, and time for tailored ceramic properties. |
Need help optimizing your ceramic sintering process? Contact our experts today for tailored solutions!