Sintering is a critical process in materials science and manufacturing, particularly in the production of ceramics, metals, and other materials. It involves the transformation of powdery materials into dense, solid bodies by applying heat and pressure at temperatures below the material's melting point. The sintering process is essential for creating structurally sound and durable products, and it includes several key steps such as powder preparation, heating, particle merging, and solidification. Understanding the sizing process in sintering is crucial for optimizing material properties and ensuring the quality of the final product.
Key Points Explained:
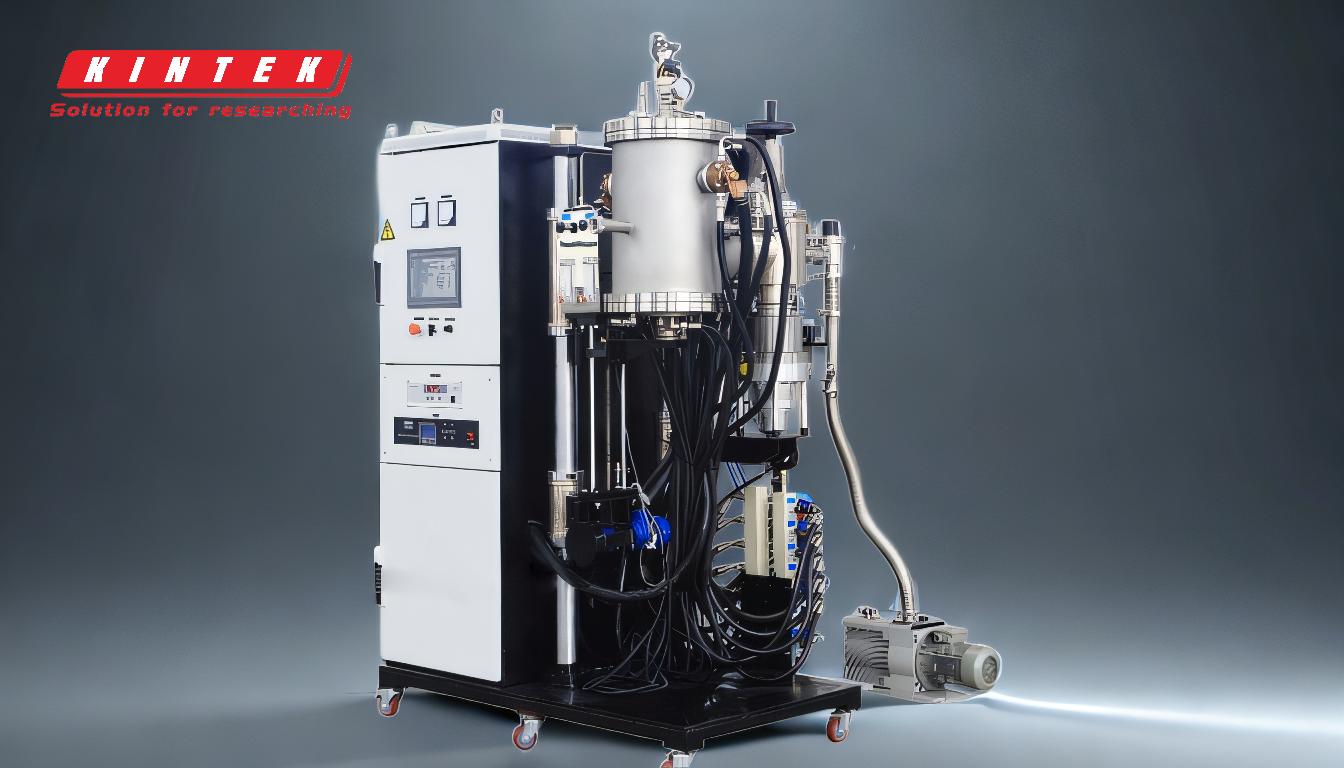
-
Definition and Purpose of Sintering:
- Sintering is a process that transforms powdery materials into dense, solid bodies by applying heat and pressure without melting the material.
- The primary purpose of sintering is to create strong, durable, and structurally sound materials by bonding adjacent powder particles.
-
Stages of the Sintering Process:
-
Preparation of the Powder Compact:
- The process begins with the preparation of a powder compact, which can be achieved through methods such as cold welding, 3D-printed lasers, or pressing tools in a controlled atmosphere.
- This stage ensures that the powder particles are evenly distributed and compacted, forming a green body that is ready for sintering.
-
Heating and Consolidation:
- The green body is then heated to a temperature just below the material's melting point. This heating activates martensitic crystalline microstructures, which are crucial for the bonding process.
- The temperature is carefully controlled to prevent melting, ensuring that the material retains its desired properties.
-
Particle Merging:
- During this stage, the powder particles densify and merge together. This can be accelerated using techniques such as liquid phase sintering (LPS), where a liquid phase aids in the bonding process.
- The merging of particles results in a reduction of porosity and an increase in the density of the material.
-
Solidification:
- After the particles have merged, the material is allowed to cool and solidify into a unified mass.
- Solidification is a critical step that ensures the final product has the desired mechanical properties and structural integrity.
-
-
Sizing Process in Sintering:
- The sizing process in sintering refers to the control and adjustment of the particle size distribution within the powder compact.
- Proper sizing is essential for achieving uniform densification and minimizing defects such as cracks or voids in the final product.
- Techniques such as sieving, milling, and classification are used to achieve the desired particle size distribution.
- The choice of particle size can significantly impact the sintering kinetics, final density, and mechanical properties of the sintered material.
-
Importance of Sizing in Sintering:
-
Uniform Densification:
- Uniform particle size distribution ensures even densification during sintering, leading to a more homogeneous final product.
-
Mechanical Properties:
- The size of the particles can influence the mechanical properties of the sintered material, such as strength, hardness, and toughness.
-
Defect Minimization:
- Proper sizing helps minimize defects such as cracks, voids, and inhomogeneities, which can compromise the integrity of the final product.
-
Process Control:
- Accurate control of particle size allows for better process control, enabling the production of materials with consistent quality and performance.
-
Uniform Densification:
-
Applications of Sintering:
- Sintering is widely used in various industries, including:
-
Powder Metallurgy:
- For the production of metal components such as gears, bearings, and filters.
-
Ceramics:
- For the manufacture of ceramic products such as tiles, insulators, and cutting tools.
-
Plastics:
- For the production of high-performance plastic components.
-
Advanced Materials:
- For the development of advanced materials with high melting points, such as tungsten and molybdenum.
-
Powder Metallurgy:
- Sintering is widely used in various industries, including:
In conclusion, the sizing process in sintering is a critical aspect that influences the quality and properties of the final product. By carefully controlling the particle size distribution, manufacturers can achieve uniform densification, minimize defects, and produce materials with superior mechanical properties. Understanding and optimizing the sizing process is essential for the successful application of sintering in various industries.
Summary Table:
Aspect | Details |
---|---|
Definition | Control of particle size distribution in powder compact for sintering. |
Key Steps | Sieving, milling, classification to achieve desired particle sizes. |
Importance | Ensures uniform densification, minimizes defects, and improves properties. |
Applications | Powder metallurgy, ceramics, plastics, and advanced materials. |
Discover how optimizing the sizing process can elevate your sintering results—contact our experts today!