Rotary kilns are thermal processing machines that rely on heat sources to achieve the desired material transformations. The primary source of heat in a rotary kiln is typically fossil fuels such as natural gas, which are burned to generate the necessary thermal energy. This heat is transferred to the material being processed through conduction, convection, and radiation. Rotary kilns can be heated either directly, where the heat source is inside the kiln chamber, or indirectly, where the heat is applied externally. Additionally, internal heat exchangers, such as scoops, lifters, or metallic inserts, are often used to enhance heat transfer efficiency, especially in low-temperature processes or cooler sections of the kiln. Electric heaters and gas burners are common heating methods, with electric heaters offering precise temperature control and gas burners utilizing waste heat for energy efficiency.
Key Points Explained:
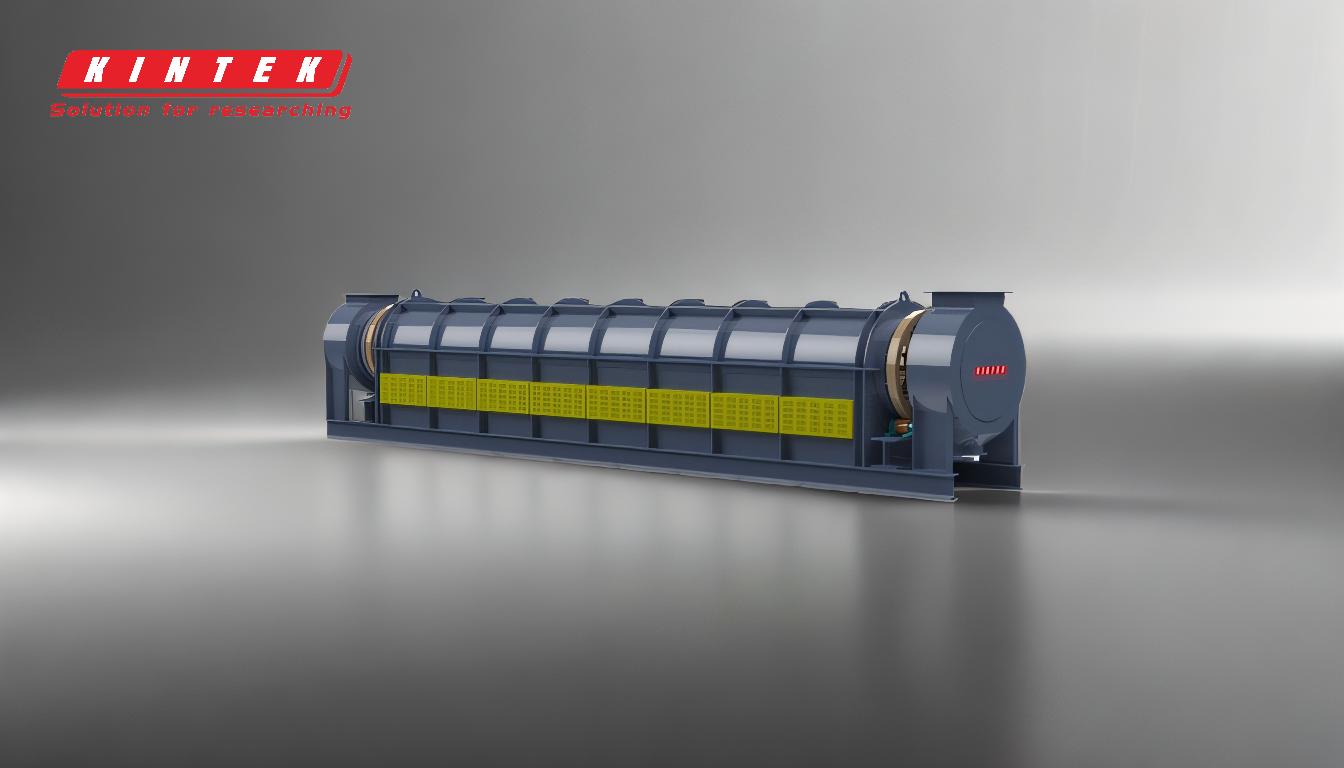
-
Primary Heat Source: Fossil Fuels
- Rotary kilns primarily use fossil fuels like natural gas as their heat source. These fuels are burned to generate the high temperatures required for thermal processing.
- Fossil fuels are chosen for their high energy density and availability, making them a cost-effective and efficient option for industrial applications.
-
Heat Transfer Mechanisms
- Heat in rotary kilns is transferred through three main mechanisms: conduction, convection, and radiation.
- Conduction: The most efficient method, where heat is transferred directly through physical contact between the kiln's internal surfaces and the material.
- Convection: Heat is transferred through the movement of hot gases within the kiln, which come into contact with the material.
- Radiation: Heat is emitted as infrared radiation from the hot surfaces of the kiln and absorbed by the material.
- The efficiency of these methods decreases in the order of conduction > convection > radiation.
- Heat in rotary kilns is transferred through three main mechanisms: conduction, convection, and radiation.
-
Direct vs. Indirect Heating
- Rotary kilns can be heated either directly or indirectly, depending on the application requirements.
- Direct Heating: The heat source (e.g., a burner) is located inside the kiln chamber, directly exposing the material to the flame and hot gases. This method is suitable for high-temperature processes.
- Indirect Heating: The heat is applied externally, and the kiln chamber is heated through its walls. This method is used when direct exposure to flames or combustion gases is undesirable, such as in processes requiring a controlled atmosphere.
- Rotary kilns can be heated either directly or indirectly, depending on the application requirements.
-
Internal Heat Exchangers
- In low-temperature processes or cooler sections of long kilns, internal heat exchangers are used to improve heat transfer efficiency.
- Scoops or Lifters: These devices lift and cascade the material through the gas stream, increasing the surface area exposed to heat.
- Metallic Inserts: These components heat up as the kiln rotates and transfer heat to the material through conduction.
- These heat exchangers ensure uniform heating and optimize energy usage.
- In low-temperature processes or cooler sections of long kilns, internal heat exchangers are used to improve heat transfer efficiency.
-
Heating Methods: Electric Heaters vs. Gas Burners
- Rotary kilns employ different heating methods, each with its advantages:
- Electric Heaters: Provide precise control over heating rates and temperature distribution. They are versatile and can operate in various atmospheres (e.g., air, oxygen, nitrogen, argon). Electric heaters are ideal for processes requiring consistent and controlled heating.
- Gas Burners: Utilize the heat from the processed material as fuel, making them energy-efficient by recycling waste heat. Gas burners are commonly used in high-temperature applications and are cost-effective for large-scale operations.
- Rotary kilns employ different heating methods, each with its advantages:
-
Applications and Process Requirements
- The choice of heat source and heating method depends on the specific application and material being processed.
- For example, in the manufacturing of roofing granules, a rotary kiln heats the coating material to just below its liquefaction point, allowing it to bond evenly with the core mineral.
- Different materials and processes may require varying temperature ranges, heating rates, and atmospheres, influencing the selection of the heat source and transfer mechanisms.
- The choice of heat source and heating method depends on the specific application and material being processed.
By understanding these key points, equipment and consumable purchasers can make informed decisions about the type of rotary kiln and heating system that best suits their operational needs, ensuring efficient and effective thermal processing.
Summary Table:
Aspect | Details |
---|---|
Primary Heat Source | Fossil fuels like natural gas for high energy density and cost efficiency. |
Heat Transfer | Conduction (most efficient), convection, and radiation. |
Heating Methods | Direct (internal heat source) or indirect (external heat source). |
Internal Heat Exchangers | Scoops, lifters, or metallic inserts for improved heat transfer. |
Heating Options | Electric heaters (precise control) or gas burners (energy-efficient). |
Applications | Depends on material, temperature range, and process requirements. |
Optimize your thermal processing with the right rotary kiln—contact our experts today for tailored solutions!