Aluminum heat treatment is a critical process in metallurgy, aimed at enhancing the mechanical properties of aluminum alloys, such as hardness, strength, and durability. The process involves heating the aluminum to a specific temperature, holding it for a set period, and then cooling it under controlled conditions. Standards for aluminum heat treatment are established by organizations like ASTM International, ISO, and SAE, which provide guidelines for temperature ranges, soaking times, cooling rates, and other parameters. These standards ensure consistency, quality, and reliability in the final product, making them essential for industries like aerospace, automotive, and construction.
Key Points Explained:
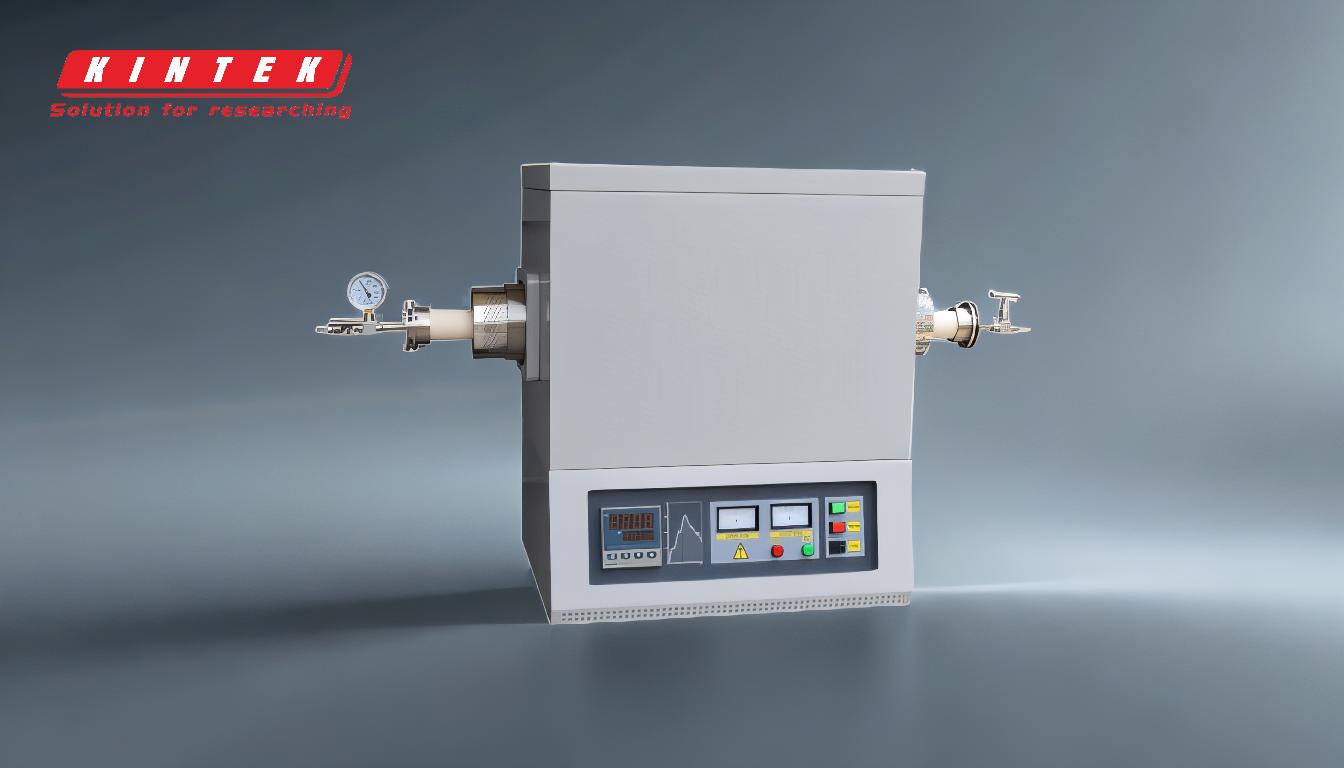
-
Purpose of Aluminum Heat Treatment:
- Heat treatment is used to alter the microstructure of aluminum alloys, improving their mechanical properties.
- Common objectives include increasing strength, improving ductility, and enhancing corrosion resistance.
- The process is tailored to specific alloys and their intended applications.
-
Types of Aluminum Heat Treatment:
- Annealing: Softens the aluminum by heating it to a specific temperature and slowly cooling it, reducing internal stresses and improving machinability.
- Solution Heat Treatment: Heats the alloy to dissolve alloying elements into a solid solution, followed by rapid cooling to retain the dissolved elements.
- Aging (Precipitation Hardening): After solution heat treatment, the alloy is aged at room temperature (natural aging) or elevated temperatures (artificial aging) to precipitate strengthening phases.
- Quenching: Rapid cooling after heating to lock in the desired microstructure, often used in conjunction with solution heat treatment.
-
Standards Governing Aluminum Heat Treatment:
- ASTM Standards: ASTM B918 and ASTM B597 provide guidelines for heat-treating aluminum alloys, including temperature ranges, soaking times, and cooling methods.
- ISO Standards: ISO 2107 specifies heat treatment terms and definitions for aluminum and its alloys.
- SAE Standards: SAE AMS 2772 outlines requirements for heat treatment of wrought aluminum alloys, particularly in aerospace applications.
-
Critical Parameters in Heat Treatment:
- Temperature: Must be carefully controlled to avoid overheating or underheating, which can lead to undesirable microstructures.
- Soaking Time: The duration the material is held at the target temperature to ensure uniform heating and proper dissolution of alloying elements.
- Cooling Rate: Determines the final microstructure and properties; rapid cooling is often required to achieve desired results.
-
Equipment Used in Heat Treatment:
- Furnaces: Precision-controlled furnaces are essential for maintaining consistent temperatures during heating and soaking.
- Quenching Systems: Used for rapid cooling, with options like water, oil, or air quenching depending on the alloy and desired properties.
- Temperature Monitoring Devices: Thermocouples and pyrometers ensure accurate temperature control throughout the process.
-
Applications of Heat-Treated Aluminum:
- Aerospace: High-strength aluminum alloys are heat-treated for use in aircraft structures and components.
- Automotive: Heat-treated aluminum is used in engine parts, wheels, and body panels to reduce weight and improve performance.
- Construction: Heat-treated aluminum alloys are used in structural components, offering a combination of strength and corrosion resistance.
-
Challenges and Considerations:
- Alloy Sensitivity: Different aluminum alloys require specific heat treatment parameters, making process control critical.
- Distortion and Warping: Improper heating or cooling can lead to dimensional changes, requiring precise process management.
- Surface Oxidation: Aluminum is prone to oxidation at high temperatures, necessitating protective atmospheres or coatings during heat treatment.
By adhering to established standards and carefully controlling the heat treatment process, manufacturers can achieve the desired properties in aluminum alloys, ensuring their suitability for demanding applications across various industries.
Summary Table:
Standard | Description |
---|---|
ASTM B918 | Guidelines for heat-treating aluminum alloys, including temperature and cooling. |
ASTM B597 | Specifies heat treatment procedures for aluminum alloys. |
ISO 2107 | Defines heat treatment terms and definitions for aluminum and its alloys. |
SAE AMS 2772 | Outlines requirements for heat treatment of wrought aluminum alloys in aerospace. |
Need expert guidance on aluminum heat treatment standards? Contact us today for tailored solutions!