Heat treatment is a critical process in metallurgy, particularly for aluminium, as it enhances the material's mechanical properties, such as hardness, strength, and ductility. The standard heat treatment processes for aluminium typically include annealing, solution heat treatment, and precipitation hardening (also known as age hardening). These processes are designed to optimize the material's microstructure, making it suitable for various industrial applications. Below, we will explore these processes in detail, focusing on their purpose, methodology, and benefits.
Key Points Explained:
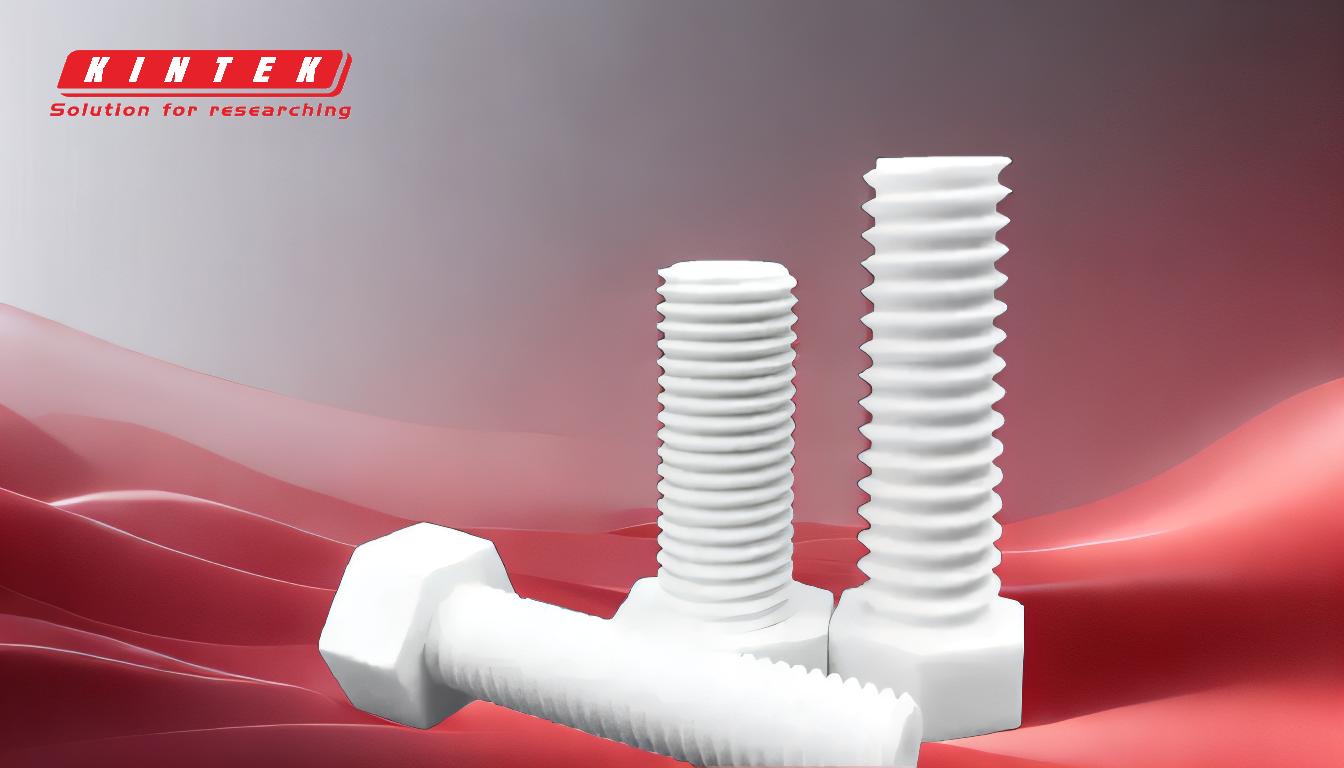
-
Annealing
- Purpose: Annealing is primarily used to soften aluminium, improve its ductility, and relieve internal stresses caused by prior manufacturing processes like cold working or welding.
- Process: The aluminium is heated to a specific temperature (typically between 300°C and 400°C) and held at that temperature for a set period. It is then slowly cooled to room temperature.
- Outcome: This process results in a more uniform microstructure, reducing hardness and increasing workability.
- Applications: Annealing is often used in the production of aluminium sheets, wires, and other components that require further shaping or forming.
-
Solution Heat Treatment
- Purpose: This process is used to dissolve alloying elements into the aluminium matrix, creating a supersaturated solid solution.
- Process: The aluminium is heated to a high temperature (typically between 450°C and 550°C) to dissolve the alloying elements. It is then rapidly cooled (quenched) to trap these elements in the solid solution.
- Outcome: The rapid cooling prevents the formation of precipitates, resulting in a softer and more ductile material.
- Applications: Solution heat treatment is commonly used in the aerospace and automotive industries, where high-strength aluminium alloys are required.
-
Precipitation Hardening (Age Hardening)
- Purpose: Precipitation hardening is used to increase the strength and hardness of aluminium alloys by forming fine precipitates within the material.
- Process: After solution heat treatment, the aluminium is aged at a lower temperature (typically between 120°C and 200°C) for several hours. This allows the alloying elements to form small, evenly distributed precipitates.
- Outcome: The precipitates impede dislocation movement, significantly increasing the material's strength and hardness while maintaining good ductility.
- Applications: This process is widely used in the production of structural components, such as aircraft frames and automotive parts.
-
Quenching
- Purpose: Quenching is a rapid cooling process used to lock the alloying elements in the aluminium matrix after solution heat treatment.
- Process: The aluminium is quickly cooled using water, air, or other cooling mediums immediately after being heated to the solution heat treatment temperature.
- Outcome: Quenching prevents the formation of coarse precipitates, ensuring a uniform microstructure.
- Applications: Quenching is an essential step in the heat treatment of high-strength aluminium alloys used in critical applications.
-
Tempering (for Aluminium Alloys)
- Purpose: Tempering is sometimes used to reduce brittleness and improve toughness in certain aluminium alloys.
- Process: The aluminium is heated to a moderate temperature (below the solution heat treatment temperature) and held for a specific period before cooling.
- Outcome: This process balances hardness and ductility, making the material more suitable for dynamic loading conditions.
- Applications: Tempering is less common for aluminium compared to steel but is used in specific alloys for specialized applications.
-
Importance of Heat Treatment in Aluminium Applications
- Heat treatment is crucial for tailoring the mechanical properties of aluminium to meet specific application requirements.
- It enables the production of lightweight, high-strength materials that are essential in industries such as aerospace, automotive, and construction.
- Proper heat treatment ensures that aluminium components can withstand mechanical stress, corrosion, and fatigue over their service life.
By understanding these standard heat treatment processes, manufacturers and purchasers can make informed decisions about the appropriate treatment methods for aluminium components, ensuring optimal performance and longevity in their intended applications.
Summary Table:
Process | Purpose | Temperature Range | Outcome | Applications |
---|---|---|---|---|
Annealing | Soften aluminium, improve ductility, relieve internal stresses | 300°C - 400°C | Uniform microstructure, reduced hardness, increased workability | Aluminium sheets, wires, components requiring shaping |
Solution Heat Treatment | Dissolve alloying elements into aluminium matrix | 450°C - 550°C | Softer, more ductile material | Aerospace, automotive industries for high-strength alloys |
Precipitation Hardening | Increase strength and hardness via fine precipitates | 120°C - 200°C (aging) | High strength, hardness, and good ductility | Structural components like aircraft frames, automotive parts |
Quenching | Rapid cooling to lock alloying elements in matrix | Immediate cooling post-heat | Prevents coarse precipitates, ensures uniform microstructure | High-strength aluminium alloys for critical applications |
Tempering | Reduce brittleness, improve toughness in specific alloys | Below solution heat temp | Balances hardness and ductility | Specialized alloys for dynamic loading conditions |
Need expert advice on aluminium heat treatment? Contact us today to optimize your material performance!