Dental porcelain is a widely used material in dentistry for creating crowns, veneers, and other dental restorations due to its aesthetic properties and biocompatibility. However, its strength is a critical factor in determining its suitability for various dental applications. The strength of dental porcelain is influenced by factors such as composition, processing techniques, and the presence of defects. Generally, dental porcelain has a flexural strength ranging from 70 to 120 MPa, which is lower than that of metals but sufficient for many dental applications. Advances in materials science, such as the development of high-strength ceramics like zirconia, have improved the mechanical properties of dental restorations. Understanding the strength of dental porcelain helps in selecting the appropriate material for specific clinical needs.
Key Points Explained:
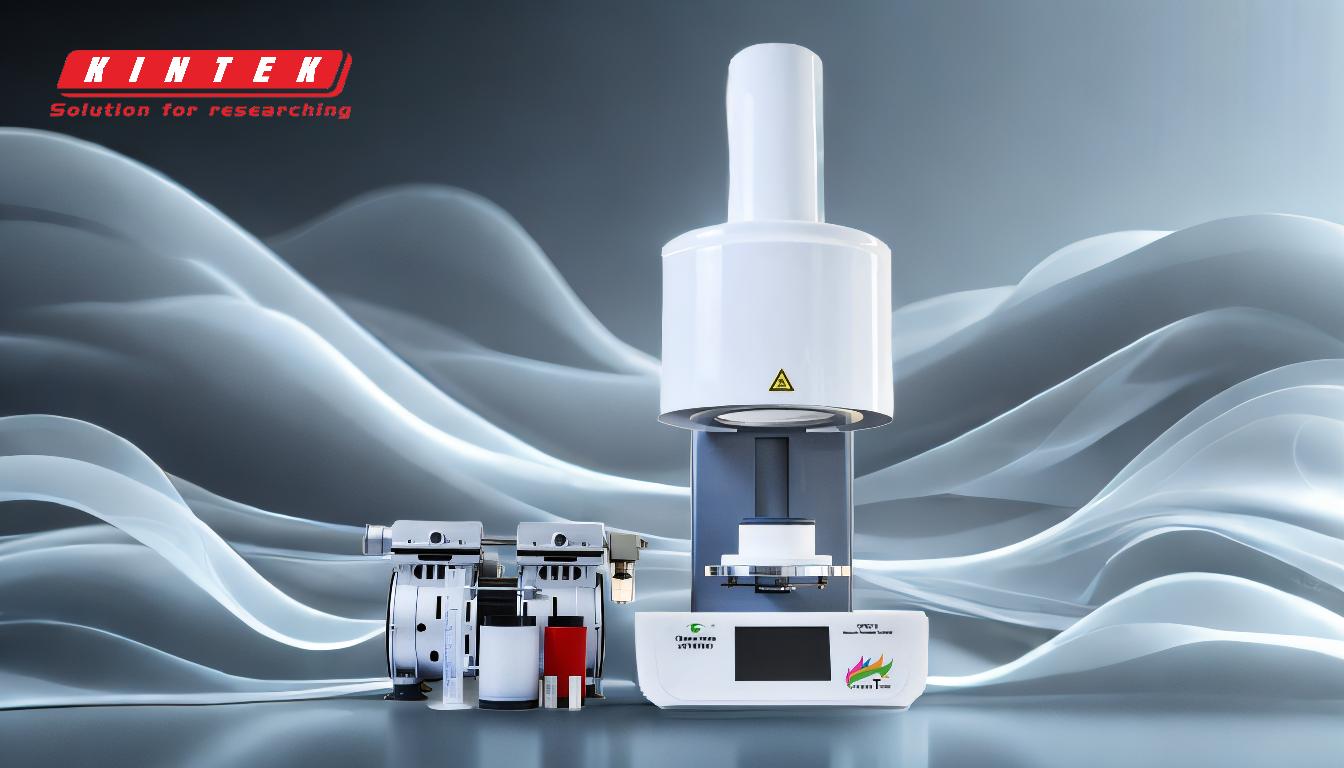
-
Composition and Types of Dental Porcelain:
- Dental porcelain is primarily composed of feldspar, quartz, and kaolin. These materials are combined to create a glassy matrix that mimics the appearance of natural teeth.
- There are different types of dental porcelain, including feldspathic porcelain, leucite-reinforced porcelain, and lithium disilicate porcelain. Each type has varying strength properties, with lithium disilicate being one of the strongest, offering flexural strengths of up to 400 MPa.
-
Flexural Strength of Dental Porcelain:
- The flexural strength of traditional dental porcelain typically ranges between 70 to 120 MPa. This measures the material's ability to resist deformation under load.
- While this strength is lower than that of metal alloys used in dentistry, it is sufficient for applications such as veneers and anterior crowns, where the aesthetic appearance is prioritized over extreme mechanical strength.
-
Factors Affecting Strength:
- Processing Techniques: The method of fabrication, such as sintering or pressing, significantly impacts the strength of dental porcelain. Pressed ceramics generally exhibit higher strength due to fewer internal defects.
- Microstructure: The presence of crystalline phases, such as leucite or lithium disilicate, can enhance strength by providing resistance to crack propagation.
- Surface Treatments: Techniques like glazing or polishing can reduce surface defects, thereby improving the overall strength of the material.
-
Comparison with Other Dental Materials:
- Compared to metals and metal-ceramic hybrids, dental porcelain has lower tensile and flexural strength. However, it offers superior aesthetics, which is crucial for visible restorations.
- High-strength ceramics like zirconia have emerged as alternatives, offering flexural strengths exceeding 900 MPa, making them suitable for posterior crowns and bridges where higher mechanical strength is required.
-
Clinical Implications:
- The choice of dental porcelain depends on the clinical situation. For anterior restorations, where aesthetics are paramount, traditional porcelain is often preferred.
- In areas subjected to higher masticatory forces, such as posterior teeth, stronger materials like zirconia or lithium disilicate are recommended to prevent fracture.
-
Advancements in Dental Porcelain:
- Recent developments in material science have led to the creation of high-strength ceramics, such as zirconia-reinforced lithium silicate, which combine the aesthetic properties of porcelain with enhanced mechanical strength.
- These advancements have expanded the applications of dental porcelain, making it a versatile option for a wide range of dental restorations.
Understanding the strength of dental porcelain is essential for clinicians to make informed decisions about material selection, ensuring both functional and aesthetic success in dental restorations.
Summary Table:
Aspect | Details |
---|---|
Flexural Strength | 70–120 MPa (traditional porcelain); up to 400 MPa (lithium disilicate) |
Composition | Feldspar, quartz, kaolin; types include feldspathic, leucite-reinforced, etc. |
Strength Factors | Processing techniques, microstructure, surface treatments |
Comparison with Metals | Lower strength but superior aesthetics |
Clinical Applications | Veneers, anterior crowns (traditional); posterior crowns (high-strength) |
Advancements | High-strength ceramics like zirconia (900+ MPa) |
Need help choosing the right dental porcelain for your practice? Contact our experts today!