An induction furnace is a cylindrical, open-topped, tiltable refractory crucible with a water-cooled induction coil installed around its side wall. It is primarily used for melting metals and creating alloys with precise compositions. The furnace operates by generating an electromagnetic field through a hollow copper coil, which induces eddy currents in the metal charge, producing heat directly within the metal. The main components include a power supply, induction coil, crucible, and various supporting systems like cooling, hydraulic, and electric control systems. These components work together to ensure efficient and controlled melting of metals.
Key Points Explained:
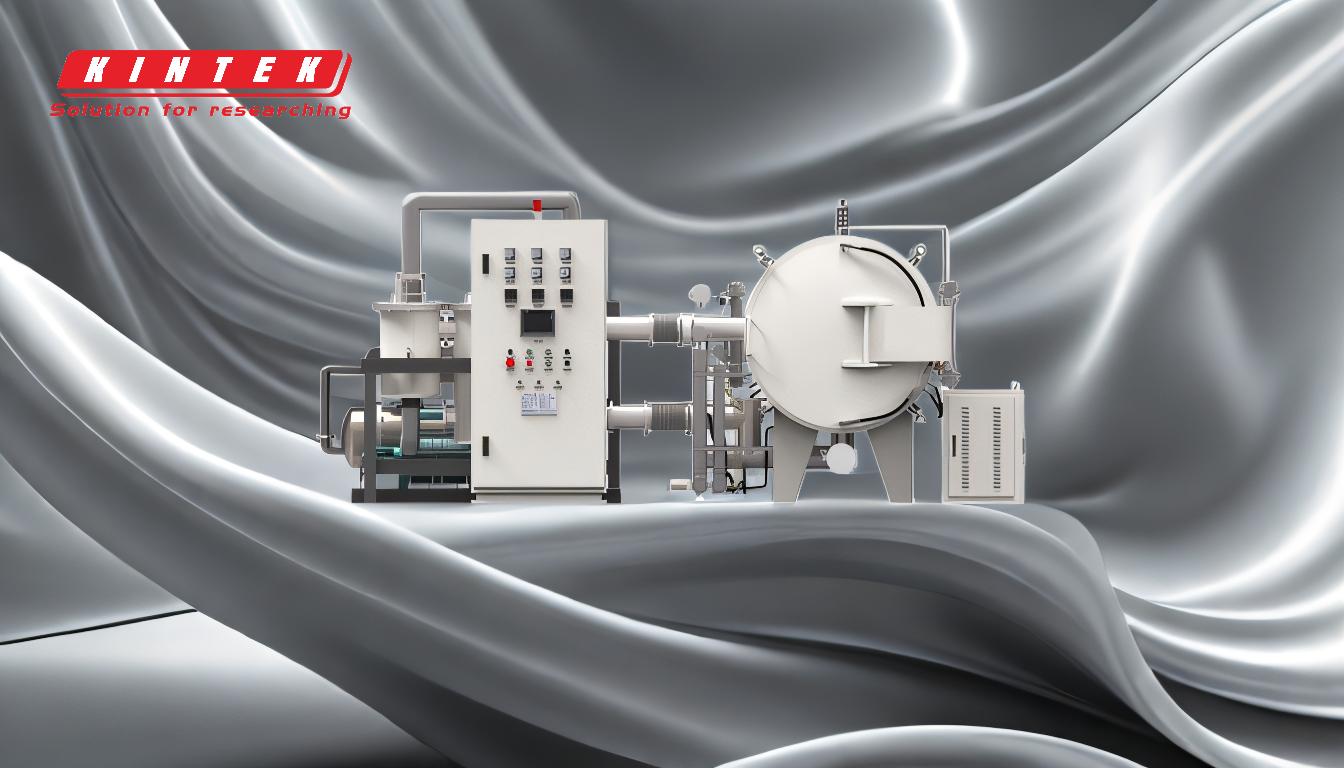
-
Cylindrical, Open-Topped, Tiltable Design:
- Induction furnaces are typically cylindrical in shape, allowing for efficient containment and melting of metal charges.
- The open-topped design facilitates easy charging of materials and observation of the melting process.
- The tiltable feature enables the furnace to pour molten metal into molds or other containers once the melting process is complete.
-
Refractory Crucible:
- The crucible is made of refractory materials that can withstand extremely high temperatures without degrading.
- It holds the metal charge and acts as the secondary winding of a transformer, where the metal charge itself becomes part of the electrical circuit.
-
Water-Cooled Induction Coil:
- The induction coil is installed around the side wall of the crucible and is typically made of hollow copper.
- The coil is water-cooled to prevent overheating due to the high-frequency alternating current passing through it.
- This coil generates the electromagnetic field necessary to induce eddy currents in the metal charge.
-
Power Supply:
- The power supply provides the necessary alternating current to the induction coil.
- In medium frequency induction furnaces, the power supply operates at frequencies such as 2500 Hz, which is optimal for efficient heating and melting of metals.
-
Induction Heating Mechanism:
- The alternating current in the induction coil creates a fluctuating electromagnetic field.
- This field induces eddy currents within the conductive metal charge, causing resistive heating.
- The heat generated is localized within the metal charge, ensuring rapid and efficient melting without excessive heating of the furnace structure.
-
Supporting Systems:
- Hydraulic System: Facilitates the tilting mechanism of the furnace for pouring molten metal.
- Water Cooling System: Ensures the induction coil and other components remain at safe operating temperatures.
- Electric Control System: Manages the power supply and other electrical components to maintain optimal melting conditions.
-
Components Specific to Aluminum Melting Induction Furnaces:
- Intermediate Frequency Power Supply: Operates at 2500 Hz, suitable for melting aluminum.
- Compensation Capacitor: Helps in maintaining the efficiency of the power supply.
- Water-Cooled Cable: Connects the power supply to the induction coil, ensuring efficient power transmission.
- Reducer: Part of the hydraulic system, aiding in the controlled tilting of the furnace.
-
Transformer Analogy:
- The induction furnace operates similarly to a transformer, where the induction coil acts as the primary winding, and the metal charge in the crucible acts as the secondary winding.
- The induced currents in the metal charge generate heat, which is the primary mechanism for melting the metal.
-
Heat Generation and Containment:
- Heat is generated directly within the metal charge, making the process highly efficient.
- The refractory crucible and water-cooled coil ensure that the heat is contained and managed effectively, preventing damage to the furnace structure.
-
Applications:
- Induction furnaces are widely used in specialty steelmaking shops and foundries.
- They are particularly valued for their ability to produce alloys with exact compositions and for their efficiency in melting metals like aluminum.
In summary, the structure of an induction furnace is designed to optimize the melting process through efficient heat generation and containment. The key components work in harmony to ensure precise control over the melting process, making induction furnaces indispensable in modern metallurgical applications.
Summary Table:
Component | Function |
---|---|
Cylindrical Crucible | Efficiently contains and melts metal charges; tiltable for pouring. |
Refractory Crucible | Withstands high temperatures; acts as a secondary winding in the circuit. |
Water-Cooled Induction Coil | Generates electromagnetic field; induces eddy currents for heating. |
Power Supply | Provides alternating current for induction heating. |
Hydraulic System | Enables tilting for pouring molten metal. |
Water Cooling System | Prevents overheating of components. |
Electric Control System | Manages power supply and melting conditions. |
Discover how an induction furnace can revolutionize your metal melting process—contact us today for expert advice!