The temperature at the bottom of a blast furnace is a critical factor in the iron-making process. According to the reference, hot air with a temperature ranging from 1,000°C to 1,200°C is blown into the furnace. This hot air reacts with coke and pulverized coal to form a reduction gas, which plays a key role in extracting oxygen from iron ore. The temperature at this stage ensures the efficiency of the reduction process and the overall productivity of the blast furnace.
Key Points Explained:
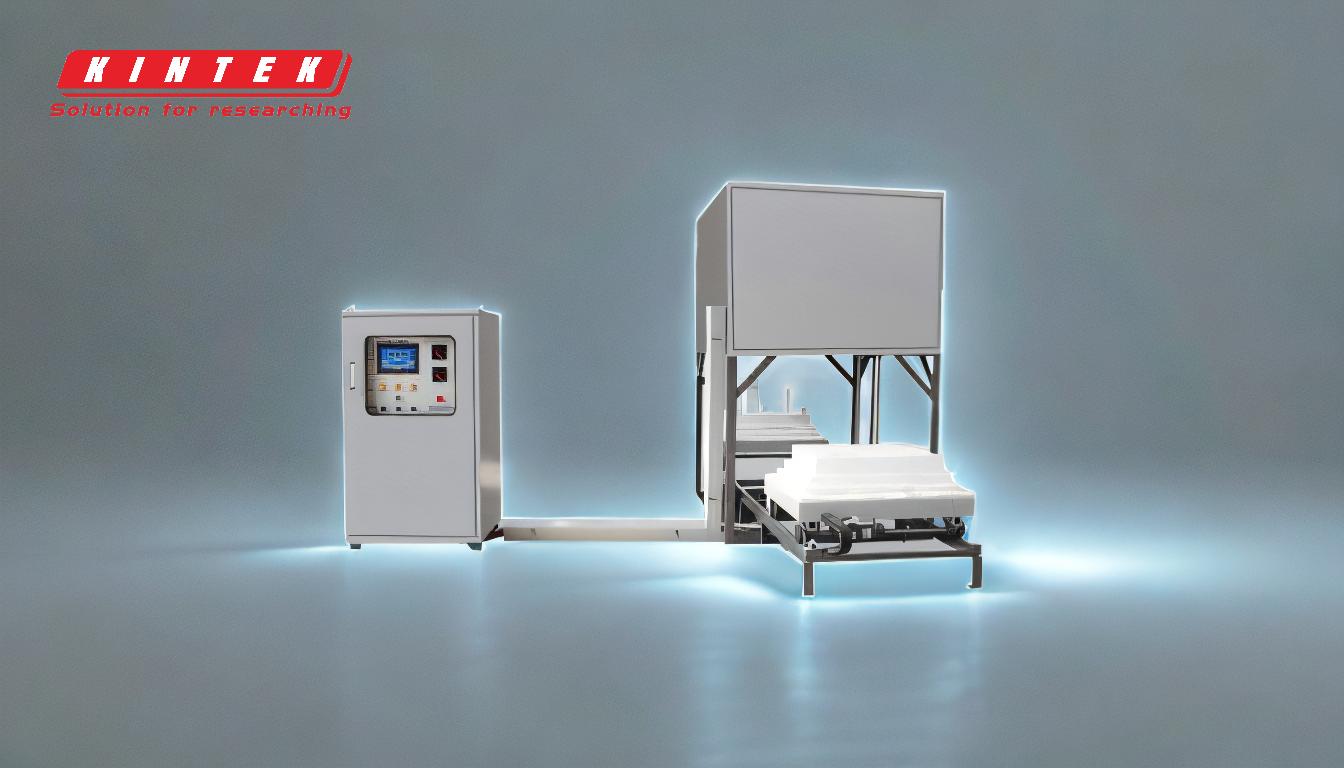
-
Temperature Range at the Bottom of the Blast Furnace:
- The temperature at the bottom of the blast furnace typically ranges between 1,000°C and 1,200°C. This high temperature is essential for maintaining the chemical reactions required for iron production.
-
Role of Hot Air in the Furnace:
- Hot air, also known as blast air, is introduced into the furnace at these high temperatures. This air is critical for:
- Reacting with coke (a form of carbon) to produce carbon monoxide (CO).
- Reacting with pulverized coal to further enhance the reduction process.
- Hot air, also known as blast air, is introduced into the furnace at these high temperatures. This air is critical for:
-
Formation of Reduction Gas:
- The hot air reacts with coke and pulverized coal to form a reduction gas, primarily composed of carbon monoxide (CO) and hydrogen (H₂).
- This gas is responsible for abstracting oxygen from the iron ore, a process known as reduction, which converts iron oxides into metallic iron.
-
Importance of High Temperature:
- The high temperature ensures that the reduction reactions occur efficiently and at a rapid pace.
- It also helps maintain the molten state of the iron and slag, allowing them to be easily separated and tapped from the furnace.
-
Impact on Furnace Efficiency:
- Maintaining the correct temperature range is crucial for:
- Maximizing the yield of metallic iron.
- Minimizing energy consumption and operational costs.
- Ensuring the longevity of the furnace lining and equipment.
- Maintaining the correct temperature range is crucial for:
-
Practical Considerations for Equipment and Consumable Purchasers:
- When purchasing equipment or consumables for a blast furnace, consider:
- The thermal resistance of materials used in the furnace lining to withstand high temperatures.
- The quality of coke and pulverized coal to ensure efficient reduction reactions.
- The design of air injection systems to deliver hot air uniformly and at the required temperature.
- When purchasing equipment or consumables for a blast furnace, consider:
By understanding these key points, equipment and consumable purchasers can make informed decisions to optimize the performance and longevity of blast furnace operations.
Summary Table:
Key Aspect | Details |
---|---|
Temperature Range | 1,000°C to 1,200°C |
Role of Hot Air | Reacts with coke and pulverized coal to form reduction gas (CO and H₂). |
Importance of High Temp | Ensures efficient reduction reactions and maintains molten iron and slag. |
Furnace Efficiency | Maximizes iron yield, reduces energy costs, and extends equipment life. |
Purchasing Considerations | Focus on thermal resistance, coke/coal quality, and air injection design. |
Ready to optimize your blast furnace operations? Contact our experts today for tailored solutions!