The temperature for debinding, specifically thermal debinding, typically ranges between 200°C and 550°C. This range is influenced by the type of binder material and the metal being used in the process. The furnace temperature is ramped up slowly to ensure the binder is not converted to gas too quickly, which could damage the parts. Additionally, the rate of debinding is affected by the particle size of the metal powder, typically occurring at a rate of 1-4 mm/h. Debinding ovens, on the other hand, have a maximum temperature of 150°C and are available in specific sizes.
Key Points Explained:
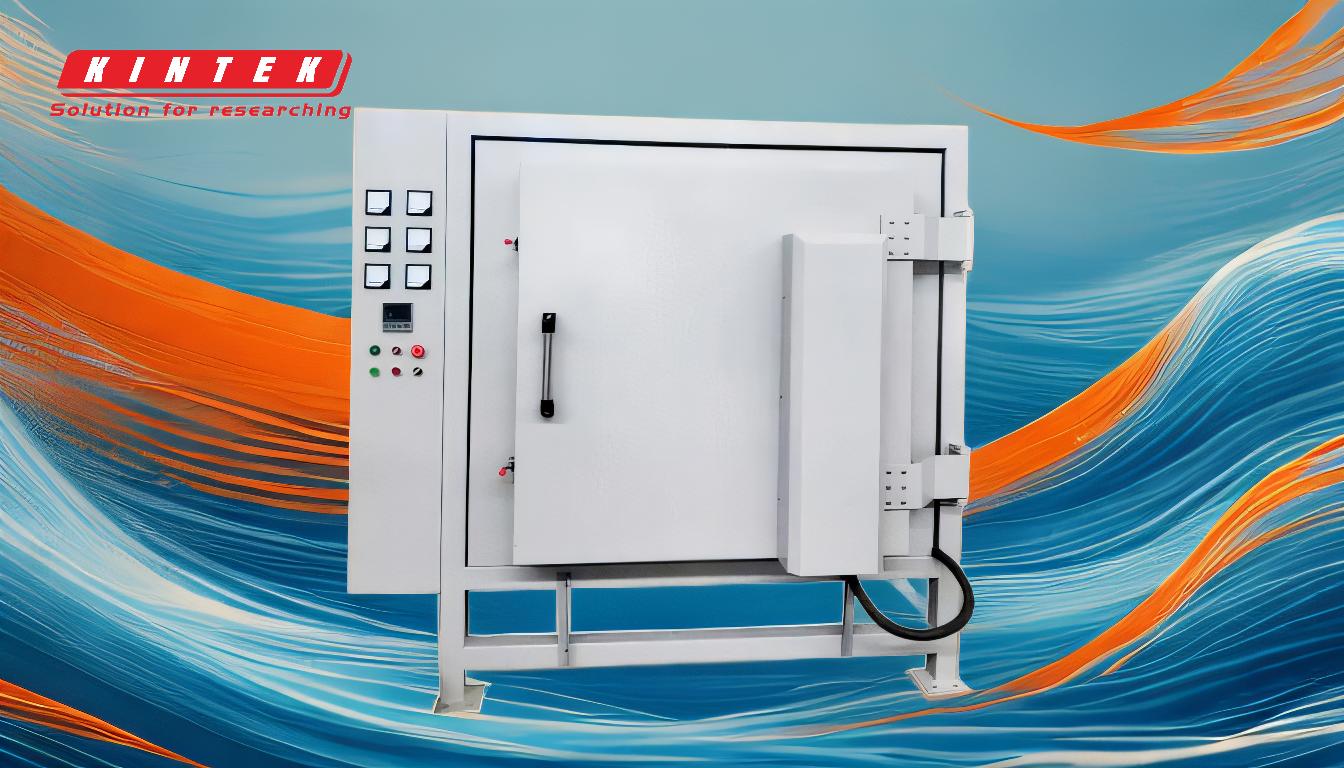
-
Temperature Range for Thermal Debinding:
- Thermal debinding generally occurs between 200°C and 550°C.
- This range is not fixed and depends on:
- Binder Material: Different binders have different thermal decomposition temperatures.
- Metal Used: The type of metal powder influences the debinding temperature due to its thermal properties.
-
Importance of Controlled Temperature Ramping:
- Furnaces are designed to ramp up slowly to the desired temperature.
- Rapid heating can cause the binder to convert to gas too quickly, leading to:
- Part Damage: Cracks or deformations in the final product.
- Incomplete Debinding: Uneven removal of the binder, affecting part quality.
-
Debinding Rate and Particle Size:
- The rate of debinding is influenced by the particle size of the metal powder.
- Typical debinding rates range between 1-4 mm/h.
- Smaller particle sizes generally lead to faster debinding rates due to increased surface area.
-
Debinding Oven Specifications:
- Debinding ovens have a maximum temperature of 150°C.
- These ovens are available in two sizes:
- 120 liters: Rectangular available space of 400 mm x 400 mm x 700 mm.
- 250 liters: Rectangular available space of 500 mm x 500 mm x 1000 mm.
- These ovens are typically used for processes requiring lower temperatures compared to thermal debinding furnaces.
-
Safety Considerations in Debinding:
- During thermal debinding, gaseous nitric acid is introduced into the furnace at a constant rate.
- It is critical to maintain a higher nitrogen flow than the nitric acid gas flow to:
- Prevent Explosive Mixtures: Ensuring safety by avoiding the formation of hazardous gas mixtures.
- Maintain Process Stability: Consistent gas flow ensures uniform debinding.
By understanding these key points, equipment and consumable purchasers can make informed decisions about the debinding process, ensuring optimal results and safety.
Summary Table:
Key Aspect | Details |
---|---|
Temperature Range | 200°C to 550°C, depending on binder material and metal type. |
Controlled Ramping | Slow heating to prevent part damage and ensure complete binder removal. |
Debinding Rate | 1–4 mm/h, influenced by metal powder particle size. |
Debinding Oven Specs | Max 150°C; sizes: 120L (400x400x700mm) and 250L (500x500x1000mm). |
Safety Considerations | Higher nitrogen flow than nitric acid gas to prevent explosive mixtures. |
Ready to optimize your debinding process? Contact our experts today for tailored solutions!