The temperature of an ashing oven typically ranges between 500°C and 900°C, depending on the specific application and material being processed. Ashing ovens are used to burn off organic material from a sample, leaving behind inorganic residues (ash). The temperature must be carefully controlled to ensure complete combustion of organic matter without damaging the sample or the oven itself. Key factors influencing the temperature setting include the type of sample, the desired level of ashing, and the oven's design. Proper calibration and monitoring are essential to maintain consistent and accurate temperatures for reliable results.
Key Points Explained:
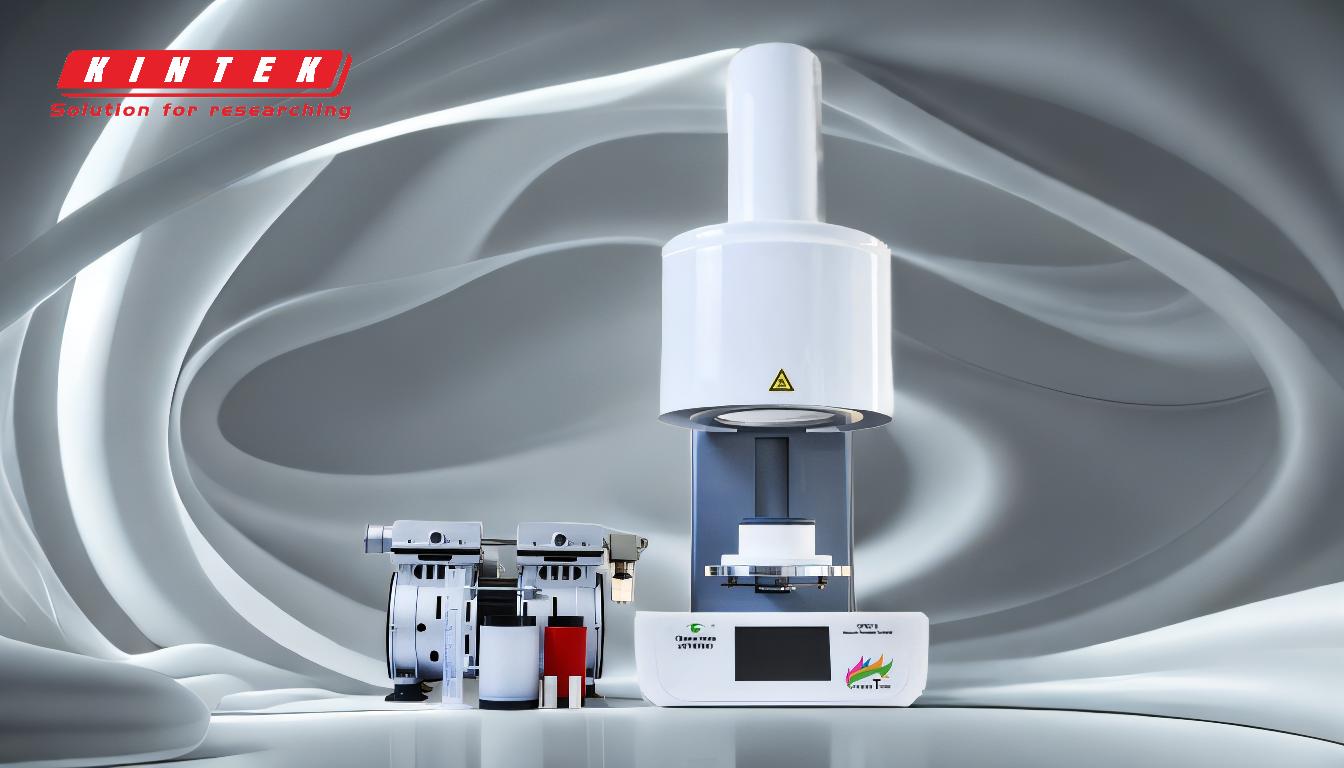
-
Typical Temperature Range:
- Ashing ovens generally operate between 500°C and 900°C.
- This range is suitable for most organic materials, ensuring complete combustion while minimizing damage to inorganic residues.
-
Factors Influencing Temperature:
- Type of Sample: Different materials require different temperatures for effective ashing. For example, biological samples may need lower temperatures compared to industrial materials.
- Desired Level of Ashing: Higher temperatures may be needed for complete ashing, but excessive heat can alter the inorganic residue.
- Oven Design: The construction and insulation of the oven can affect its ability to maintain consistent temperatures.
-
Importance of Temperature Control:
- Complete Combustion: Ensuring all organic material is burned off is critical for accurate analysis of inorganic residues.
- Sample Integrity: Overheating can damage the sample or the oven, while insufficient heat may leave residual organic material.
- Consistency: Reliable results depend on maintaining a stable temperature throughout the ashing process.
-
Calibration and Monitoring:
- Calibration: Regular calibration ensures the oven operates at the correct temperature.
- Monitoring: Continuous temperature monitoring helps detect and correct deviations, ensuring consistent performance.
-
Applications of Ashing Ovens:
- Laboratory Analysis: Used in chemistry and biology labs to analyze inorganic content in organic samples.
- Industrial Processes: Applied in industries like metallurgy and environmental testing to determine ash content in materials.
By understanding these key points, users can select the appropriate temperature for their specific application and ensure optimal performance of their ashing oven.
Summary Table:
Aspect | Details |
---|---|
Typical Temperature | 500°C–900°C, suitable for most organic materials |
Key Influencing Factors | - Sample type - Desired ashing level - Oven design |
Importance of Control | Ensures complete combustion, sample integrity, and consistent results |
Calibration & Monitoring | Regular calibration and continuous monitoring for accurate performance |
Applications | - Laboratory analysis - Industrial processes (e.g., metallurgy, testing) |
Need help selecting the right ashing oven for your application? Contact our experts today!