The temperature of an induction furnace can vary significantly depending on its design, application, and the materials being processed. Generally, induction furnaces can achieve temperatures ranging from 800°C to 2000°C or higher. For forging applications, temperatures typically reach up to 1250°C, while melting processes can achieve temperatures of 1650°C or more. Advanced induction heating systems, especially those using IGBT frequency conversion, can even reach temperatures as high as 1800°C or more, depending on the inductive coupling between the coil and the charge materials. These high temperatures are achieved through the generation of eddy currents within the material, which produce uniform heating and efficient melting or forging. Additionally, the furnace's design, including its power regulation and cooling systems, ensures stable operation and precise temperature control.
Key Points Explained:
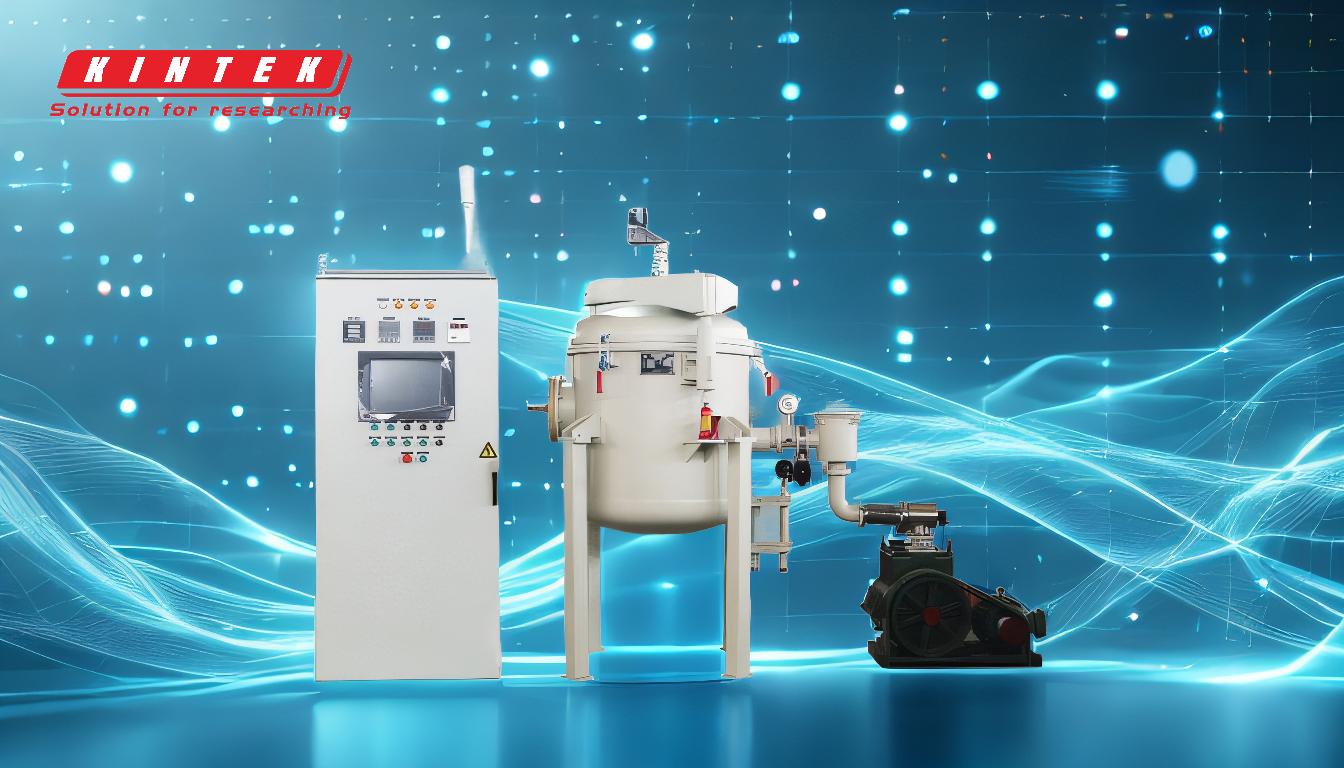
-
Temperature Range of Induction Furnaces:
- Induction furnaces can achieve a wide range of temperatures, typically between 800°C and 2000°C.
- Forging applications usually require temperatures up to 1250°C, while melting processes can reach 1650°C or higher.
- Advanced systems, such as those using IGBT frequency conversion, can achieve temperatures of 1800°C or more, depending on the inductive coupling with the charge materials.
-
Mechanism of Heating:
- Induction furnaces use alternating electromagnetic fields to generate eddy currents within the material being heated.
- These eddy currents produce resistive heating, which rapidly and uniformly raises the temperature of the material.
- The process ensures uniform composition and temperature distribution, which is critical for melting or forging applications.
-
Components and Design Features:
- The main components of an induction furnace include the inductor, furnace body, power supply, capacitor, and control system.
- Modern induction furnaces often use IGBT frequency conversion and power regulation, which improve efficiency and temperature control.
- The furnace design includes cooling systems (e.g., chillers) and protection mechanisms (e.g., overcurrent, overheating, and water shortage protection) to ensure safe and stable operation.
-
Applications and Temperature Requirements:
- Forging: Typically requires temperatures up to 1250°C for heating metal workpieces.
- Melting: Can achieve temperatures of 1650°C or higher, depending on the material being melted (e.g., steel, cast iron, or alloys).
- High-Temperature Applications: Advanced systems can reach 1800°C or more, making them suitable for specialized industrial processes.
-
Advantages of Induction Furnaces:
- Uniform Heating: The induction process ensures even temperature distribution, reducing the risk of hot spots or uneven melting.
- Energy Efficiency: Induction furnaces are highly efficient, with more than 95% effective output power.
- Environmental Benefits: They are power-saving and produce fewer emissions compared to traditional furnaces.
- Versatility: Induction furnaces can handle a wide range of materials and weights, with easy replacement of furnace bodies for different applications.
-
Operational Features:
- Continuous Operation: Many induction furnaces support 24-hour continuous smelting, making them ideal for industrial settings.
- Compact Design: Modern induction furnaces are lightweight and movable, with a small footprint (less than one square meter).
- Precise Control: Features like automatic frequency scanning, constant power circuits, and comprehensive protection systems ensure reliable and stable operation.
-
Inductive Coupling and Temperature:
- The temperature achieved in an induction furnace depends on the inductive coupling between the coil and the charge materials.
- Stronger coupling results in higher temperatures, making it possible to reach 1800°C or more for specialized applications.
- This coupling also enables magnetic stirring, which improves composition uniformity and scum removal during melting.
-
Safety and Reliability:
- Induction furnaces are equipped with comprehensive protection systems, including alarms for overvoltage, overcurrent, overheating, and water shortage.
- These features ensure higher reliability and durability, even during continuous operation.
- The use of large-scale integrated circuits and optimized control boards further enhances stability and performance.
-
Industrial Use Cases:
- Induction furnaces are widely used in metal forging, melting, and alloy production.
- They are particularly effective for high-precision applications, where exact composition and temperature control are critical.
- The ability to reach extremely high temperatures makes them suitable for processing high melting point alloys like cast iron.
-
Future Trends:
- The trend towards miniaturization and integration in induction furnace design is improving efficiency and reducing costs.
- Advances in IGBT technology and cooling systems are enabling higher temperatures and faster processing times.
- The focus on environmental sustainability is driving the development of more energy-efficient and eco-friendly induction furnaces.
By understanding these key points, equipment and consumable purchasers can make informed decisions about the type of induction furnace that best meets their needs, ensuring optimal performance and cost-effectiveness.
Summary Table:
Feature | Details |
---|---|
Temperature Range | 800°C to 2000°C+ |
Forging Applications | Up to 1250°C |
Melting Applications | Up to 1650°C or higher |
Advanced Systems | Up to 1800°C+ with IGBT frequency conversion |
Heating Mechanism | Eddy currents for uniform, efficient heating |
Key Components | Inductor, furnace body, power supply, capacitor, control system |
Energy Efficiency | >95% effective output power |
Environmental Benefits | Power-saving, fewer emissions |
Operational Features | 24-hour smelting, compact design, precise control |
Safety Features | Overvoltage, overcurrent, overheating, and water shortage protection |
Ready to optimize your industrial processes with a high-performance induction furnace? Contact us today to find the perfect solution for your needs!