Ceramic tubes, depending on their composition, exhibit excellent temperature resistance, making them suitable for high-temperature applications. For instance, C30 ceramic (mullite) can withstand temperatures up to 2900°F (1600°C) and is impervious to air up to 3000°F. Alumina ceramic tubes can endure even higher temperatures, up to 1800°C, especially under reducing, inert, and high-vacuum conditions. These materials are chosen for their low thermal expansion, high thermal shock resistance, and resistance to corrosive environments, making them ideal for industrial and scientific applications where extreme conditions are prevalent.
Key Points Explained:
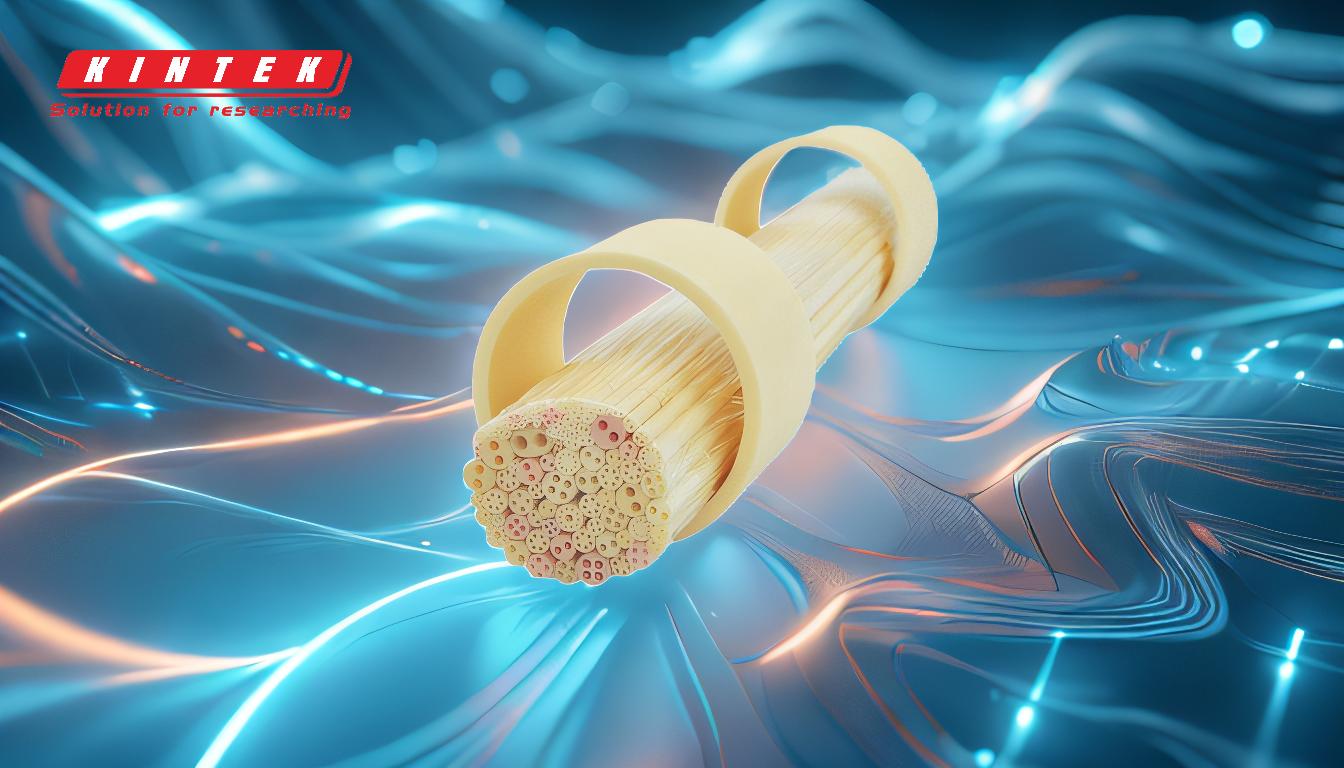
-
Temperature Resistance of C30 Ceramic (Mullite):
- Maximum Operating Temperature: C30 ceramic can operate at temperatures up to 2900°F (1600°C).
- Impervious to Air: It remains impervious to air up to 3000°F.
- Resistance to Gases: It is also resistant to dry hydrogen and carbon monoxide up to 2550°F.
- Thermal Expansion: The low rate of thermal expansion (2.8 x 10^-6/°F) enhances its thermal shock resistance, making it suitable for environments with rapid temperature changes.
-
Temperature Resistance of Alumina Ceramic Tubes:
- Maximum Operating Temperature: Alumina ceramic tubes can withstand temperatures up to 1800°C.
- Environmental Conditions: They are particularly effective under reducing, inert, and high-vacuum environments, which are common in advanced industrial processes.
-
General Properties of Ceramic Materials:
- Thermal Stability: Traditional ceramics are known for their thermal stability, which has been utilized in various applications such as cooking vessels and serving dishes.
- Chemical and Mechanical Stability: These materials are also mechanically and chemically stable, which is crucial for their use in harsh environments.
- Advanced Ceramics: Advanced ceramic materials, composed of ionic or covalent bonds, offer properties like high strength, hardness, wear resistance, and corrosion resistance, in addition to high temperature resistance.
-
Applications and Implications:
- Industrial Use: The high temperature resistance of ceramic tubes makes them ideal for use in industries such as metallurgy, chemical processing, and semiconductor manufacturing.
- Scientific Research: In scientific research, especially in high-temperature experiments, the stability and resistance of ceramic materials are invaluable.
- Durability and Longevity: The wear and corrosion resistance of these materials contribute to their durability and longevity, reducing the need for frequent replacements and maintenance.
In summary, ceramic tubes, particularly those made from C30 ceramic and alumina, offer exceptional temperature resistance and stability under various environmental conditions. These properties make them indispensable in both industrial and scientific settings where high temperatures and corrosive environments are common.
Summary Table:
Property | C30 Ceramic (Mullite) | Alumina Ceramic Tubes |
---|---|---|
Max Operating Temperature | 2900°F (1600°C) | 1800°C |
Impervious to Air | Up to 3000°F | N/A |
Gas Resistance | Dry hydrogen, CO up to 2550°F | Reducing, inert, high-vacuum |
Thermal Expansion | 2.8 x 10^-6/°F | N/A |
Applications | Industrial, scientific research | Advanced industrial processes |
Need ceramic tubes for high-temperature applications? Contact us today to find the perfect solution!