Temperature verification of a muffle furnace is a critical process to ensure the furnace operates accurately and safely within the desired temperature range. It involves calibrating and verifying the furnace's temperature settings to match the experimental or processing requirements. This process ensures that the furnace maintains the correct temperature for applications such as melting, casting, or heat treatment. Proper temperature verification involves understanding the furnace's maximum temperature limits, setting the appropriate temperature setpoint, and continuously monitoring the system to avoid damage to the heating elements and ensure consistent performance.
Key Points Explained:
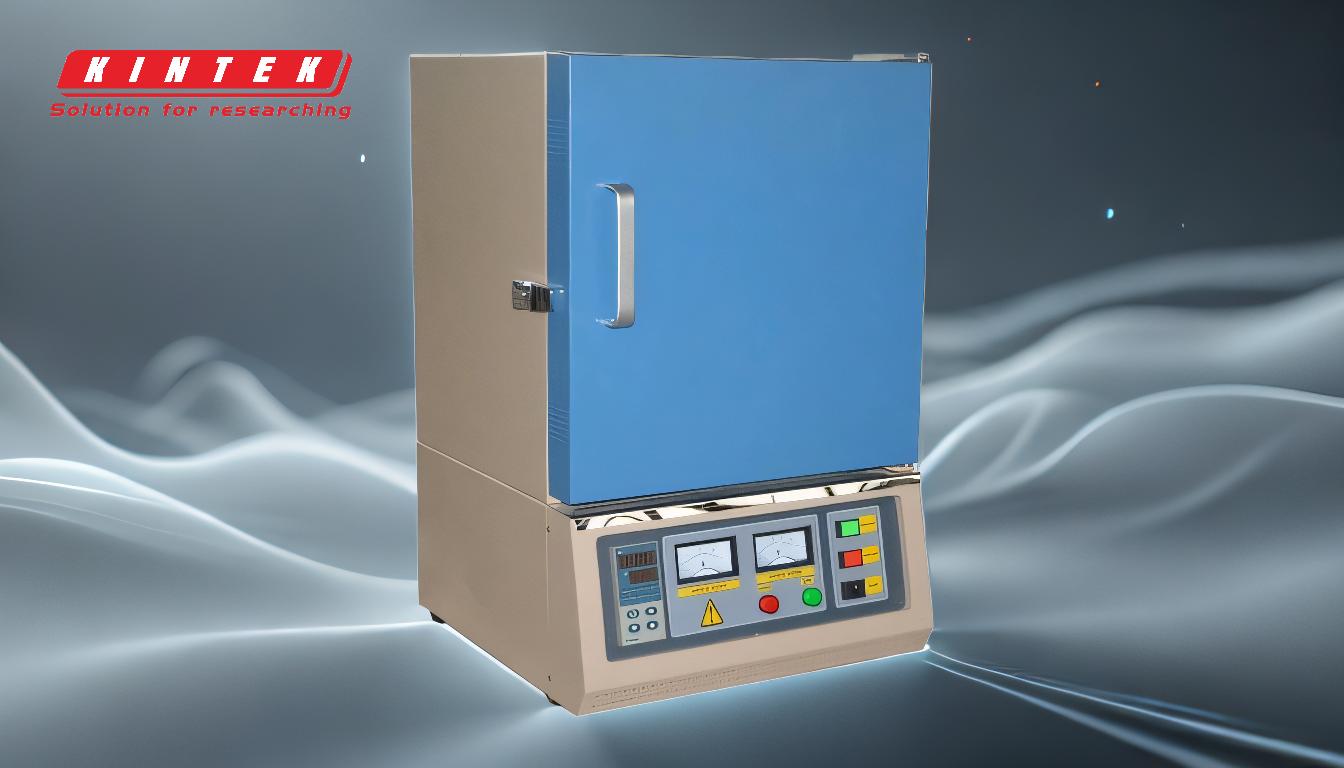
-
Understanding the Muffle Furnace's Temperature Range
- Muffle furnaces are designed to operate within specific temperature ranges, typically between 800°C and 1800°C, depending on the type of heating elements used.
- Metallic wire heating elements usually support temperatures up to 1000°C to 1200°C, while silicon carbide and molybdenum disilicide heating elements can achieve higher temperatures of 1600°C and 1800°C, respectively.
- It is crucial to know the furnace's maximum rated temperature and avoid exceeding it to prevent damage to the heating elements. Operating 50°C below the maximum temperature is recommended to extend the furnace's lifespan.
-
Setting the Temperature Setpoint
- The temperature setpoint is the specific temperature at which the muffle furnace operates, determined by the application or process requirements.
- Before adjusting the temperature, consult the experimental or processing guidelines to identify the optimal temperature range.
- Ensure the furnace is properly connected to a reliable power supply and turned on before setting the temperature.
-
Temperature Verification Process
- Temperature verification involves calibrating the furnace to ensure it accurately reaches and maintains the desired temperature.
- Use a calibrated external thermometer or a temperature data logger to verify the furnace's internal temperature matches the setpoint.
- Regularly monitor the temperature during operation to ensure consistency and make adjustments if necessary.
-
Importance of Continuous Monitoring
- Continuous monitoring is essential to ensure the furnace operates within the desired temperature range and avoids overheating.
- Overheating can damage the heating elements and compromise the furnace's performance.
- Follow the manufacturer's user manual for specific guidelines on monitoring and maintaining the furnace.
-
Safety Considerations
- Always operate the muffle furnace within its specified temperature limits to prevent accidents and equipment damage.
- Ensure the furnace is placed in a well-ventilated area and away from flammable materials.
- Regularly inspect the furnace for signs of wear or damage, especially to the heating elements and insulation.
By following these steps, you can ensure accurate temperature verification and optimal performance of your muffle furnace, making it suitable for a wide range of high-temperature applications.
Summary Table:
Key Aspect | Details |
---|---|
Temperature Range | 800°C to 1800°C, depending on heating elements (metallic wire, silicon carbide, etc.). |
Setpoint Adjustment | Determine based on application needs; ensure proper power supply and startup. |
Verification Tools | Use calibrated external thermometers or data loggers for accurate readings. |
Continuous Monitoring | Essential to avoid overheating and maintain consistent performance. |
Safety Measures | Operate within limits, ensure ventilation, and inspect for wear or damage. |
Ensure your muffle furnace operates at peak performance—contact our experts today for guidance!