Calcination is a thermal treatment process applied to solid chemical compounds, such as mixed carbonate ores, where the material is heated to high temperatures below its melting point, typically in the absence or limited supply of oxygen. This process is primarily used to remove impurities, volatile substances, or induce thermal decomposition, often to extract metals from ores or achieve specific material properties. Calcination drives off chemically bound components like water or carbon dioxide, leading to a phase transition or the formation of a more stable compound. It is widely used in industries such as metallurgy, ceramics, and cement production.
Key Points Explained:
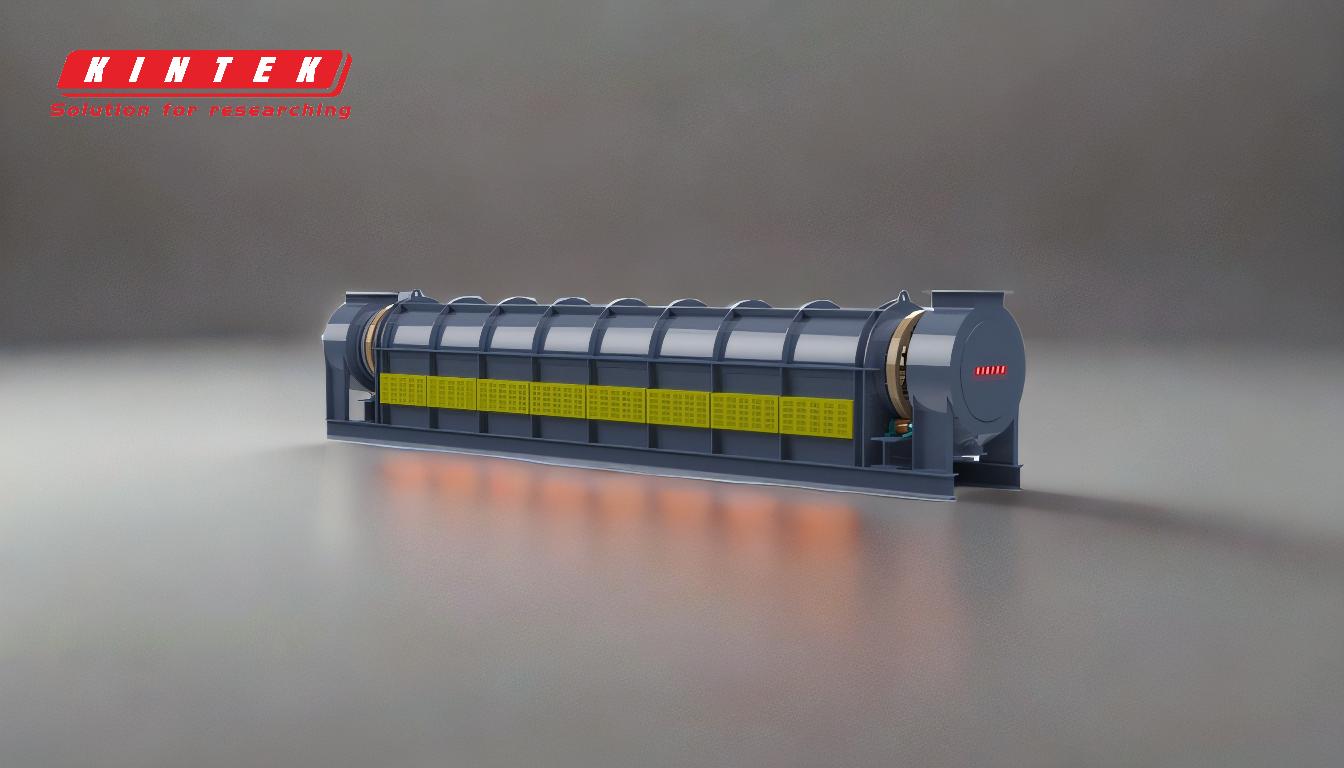
-
Definition of Calcination:
- Calcination is a heat treatment process where solid materials, such as ores or chemical compounds, are heated to high temperatures below their melting points.
- It is conducted in the absence or limited supply of oxygen to prevent combustion or unwanted oxidation.
-
Purpose of Calcination:
- Removal of Volatile Substances: Calcination removes volatile components like water, carbon dioxide, or organic impurities, which are driven off as gases.
- Thermal Decomposition: It causes the breakdown of compounds into simpler substances, such as converting carbonates to oxides.
- Phase Transition: The process can induce a change in the physical or chemical structure of the material, leading to a more stable or desired phase.
- Metal Extraction: In metallurgy, calcination is used to extract metals from ores by decomposing metal carbonates or hydroxides into metal oxides.
-
Process Conditions:
- Temperature: The material is heated to high temperatures, typically below its melting point, to avoid melting while achieving the desired chemical changes.
- Atmosphere: Calcination is performed in a controlled environment, often with limited oxygen, to prevent oxidation or combustion of the material.
- Duration: The heating duration depends on the material and the desired outcome, ensuring complete decomposition or removal of volatile components.
-
Applications of Calcination:
- Metallurgy: Used to extract metals like iron, zinc, and aluminum from their ores by converting metal carbonates or hydroxides into oxides.
- Cement Production: Calcination of limestone (calcium carbonate) produces lime (calcium oxide), a key ingredient in cement.
- Ceramics and Refractories: Calcination is used to produce ceramic materials and refractory products by removing impurities and achieving desired material properties.
- Chemical Industry: It is employed in the production of various chemicals, such as titanium dioxide from titanium ore.
-
Examples of Calcination Reactions:
-
Decomposition of Calcium Carbonate:
[ \text{CaCO}_3 \rightarrow \text{CaO} + \text{CO}_2 \uparrow ] This reaction is fundamental in cement production. -
Conversion of Zinc Carbonate to Zinc Oxide:
[ \text{ZnCO}_3 \rightarrow \text{ZnO} + \text{CO}_2 \uparrow ] Used in the extraction of zinc from its ores.
-
Decomposition of Calcium Carbonate:
-
Advantages of Calcination:
- Purification: Effectively removes impurities and volatile substances, improving the quality of the final product.
- Controlled Decomposition: Allows precise control over the thermal breakdown of compounds, leading to consistent results.
- Energy Efficiency: Since the process occurs below the melting point, it often requires less energy compared to melting or smelting.
-
Limitations of Calcination:
- High-Temperature Requirements: Calcination often requires significant energy input to achieve the necessary temperatures.
- Emission of Gases: The release of volatile substances, such as carbon dioxide, can contribute to environmental concerns if not managed properly.
- Material-Specific: The effectiveness of calcination depends on the specific properties of the material being treated, and not all compounds are suitable for this process.
-
Comparison with Other Thermal Processes:
- Calcination vs. Roasting: While both involve heating, roasting is typically done in the presence of excess oxygen and is used to convert sulfides to oxides, whereas calcination is performed in a limited oxygen environment.
- Calcination vs. Sintering: Sintering involves heating materials to bond particles together without melting, often used in powder metallurgy, whereas calcination focuses on decomposition or phase transitions.
By understanding the theory of calcination, industries can optimize this process for material purification, decomposition, and phase transformation, making it a critical step in various manufacturing and extraction processes.
Summary Table:
Aspect | Details |
---|---|
Definition | Heating solid materials below melting point in limited oxygen environments. |
Purpose | Remove impurities, induce decomposition, and extract metals. |
Applications | Metallurgy, cement production, ceramics, and chemical industries. |
Advantages | Purification, controlled decomposition, energy efficiency. |
Limitations | High energy use, gas emissions, material-specific effectiveness. |
Key Reactions | CaCO₃ → CaO + CO₂; ZnCO₃ → ZnO + CO₂. |
Discover how calcination can optimize your industrial processes—contact us today for expert guidance!