Spark Plasma Sintering (SPS) is an advanced sintering technique that combines pulsed direct electric current, uniaxial pressure, and plasma activation to achieve rapid and efficient densification of materials. Unlike traditional sintering methods, SPS utilizes a unique combination of Joule heating, plastic deformation, and localized plasma discharge between powder particles to activate surfaces, purify impurities, and promote particle bonding. This results in faster heating rates, shorter sintering times, and lower processing temperatures, while preserving the microstructure and enhancing the mechanical properties of the final product. SPS is particularly advantageous for producing high-density, fine-grained materials with improved performance.
Key Points Explained:
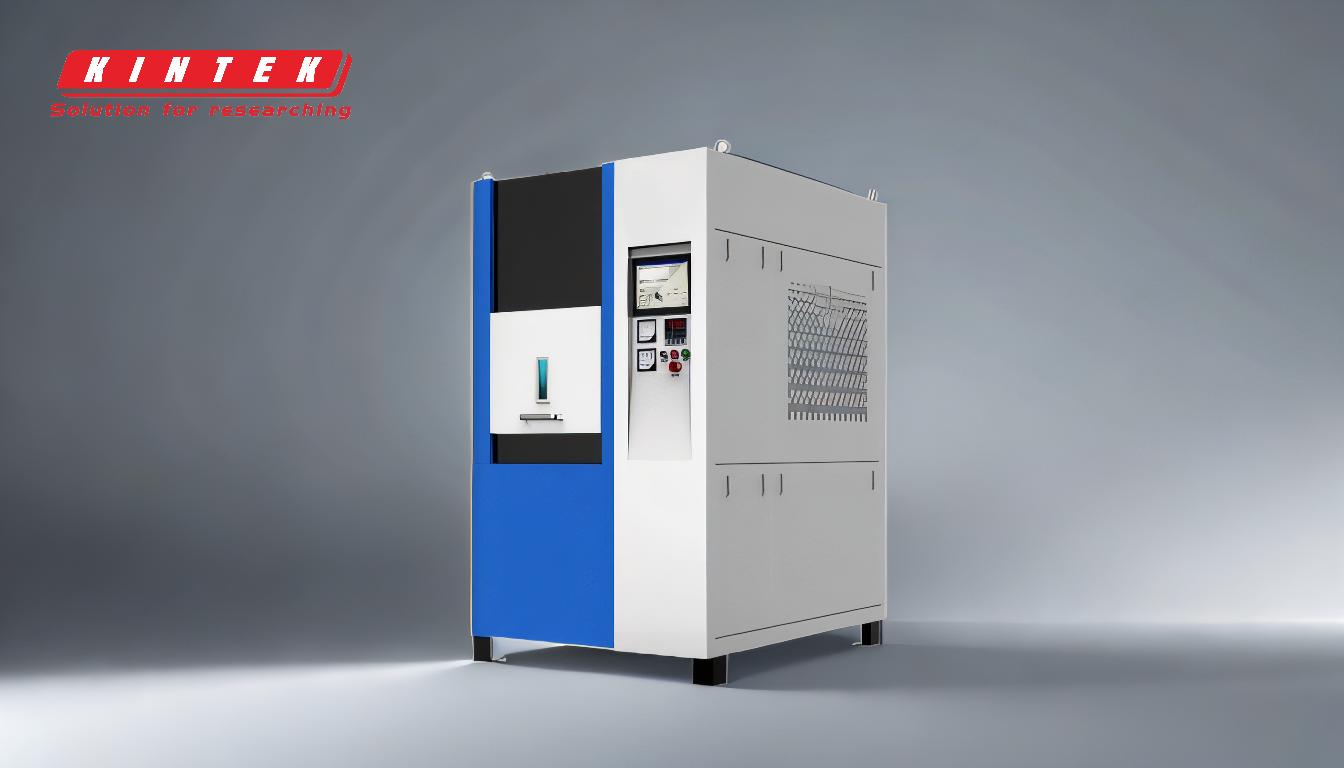
-
Fundamental Principles of SPS:
- SPS employs pulsed direct electric current passed through a conductive graphite die, combined with uniaxial pressure, to sinter materials.
- The process integrates three key mechanisms: plasma activation, hot pressing, and resistance heating.
- Joule heating generates heat within the material, while pressure induces plastic deformation, and pulsed voltage creates localized plasma discharges between particles.
-
Plasma Activation and Particle Bonding:
- During the plasma heating stage, electrical discharges between powder particles cause localized surface heating, reaching temperatures of several thousand degrees Celsius.
- This heating purifies particle surfaces by vaporizing impurities and activates the surfaces, promoting the formation of "necks" between particles.
- The uniform distribution of heat and plasma activation ensures efficient bonding and densification.
-
Advantages of SPS:
- Fast Heating and Sintering: SPS achieves rapid heating rates and short sintering times, significantly reducing processing time compared to conventional methods.
- Low Sintering Temperature: The process operates at temperatures below the material’s melting point, preserving the microstructure and minimizing grain growth.
- Energy Efficiency: The combination of direct heating and plasma activation results in lower energy consumption.
- Improved Material Properties: SPS produces materials with high density, fine-grained structures, and enhanced mechanical properties.
-
Applications and Benefits:
- SPS is ideal for consolidating milled powders, especially those with refined microstructures achieved through processes like cryogenic milling.
- It is widely used in the production of advanced ceramics, composites, and nanostructured materials, where maintaining fine grain sizes and high density is critical.
- The ability to sinter at lower temperatures and shorter times makes SPS suitable for materials sensitive to high-temperature degradation.
-
Unique Features of SPS:
- Uniform Heating: The process ensures even heat distribution throughout the sample, reducing thermal gradients and minimizing defects.
- Surface Activation: Plasma discharge purifies and activates particle surfaces, enhancing bonding and densification.
- Microstructure Preservation: SPS inhibits grain growth, maintaining the original particle microstructure and improving the final product's performance.
-
Comparison with Traditional Sintering:
- Traditional sintering relies on external heating sources and longer processing times, often leading to grain growth and reduced material properties.
- SPS, with its direct heating and plasma activation, offers a more efficient and controlled sintering process, resulting in superior material characteristics.
In summary, Spark Plasma Sintering is a cutting-edge technique that leverages the synergistic effects of pulsed electric current, pressure, and plasma activation to produce high-performance materials with exceptional density and microstructure. Its advantages in speed, efficiency, and material quality make it a preferred choice for advanced material processing.
Summary Table:
Key Aspect | Description |
---|---|
Fundamental Principles | Combines pulsed electric current, uniaxial pressure, and plasma activation. |
Plasma Activation | Localized surface heating purifies and activates particles for efficient bonding. |
Advantages | Fast heating, low sintering temperatures, energy efficiency, and improved properties. |
Applications | Advanced ceramics, composites, nanostructured materials, and sensitive materials. |
Unique Features | Uniform heating, surface activation, and microstructure preservation. |
Comparison with Traditional | Faster, more efficient, and superior material properties compared to traditional sintering. |
Unlock the potential of Spark Plasma Sintering for your materials—contact our experts today!