Thermal evaporation is a widely used physical vapor deposition (PVD) technique for depositing thin films onto substrates. It involves heating a solid material in a high vacuum chamber until it vaporizes, creating a vapor stream that travels through the chamber and adheres to the substrate as a thin film or coating. This method is particularly useful for applications such as creating OLEDs, thin-film transistors, and other electronic or optical coatings. The process relies on high vacuum conditions to ensure the vapor stream travels without scattering or reacting with other atoms, resulting in a pure and uniform deposition. Thermal evaporation can be achieved using electric resistance heaters, electron beam evaporators, or tungsten filaments, depending on the material and application requirements.
Key Points Explained:
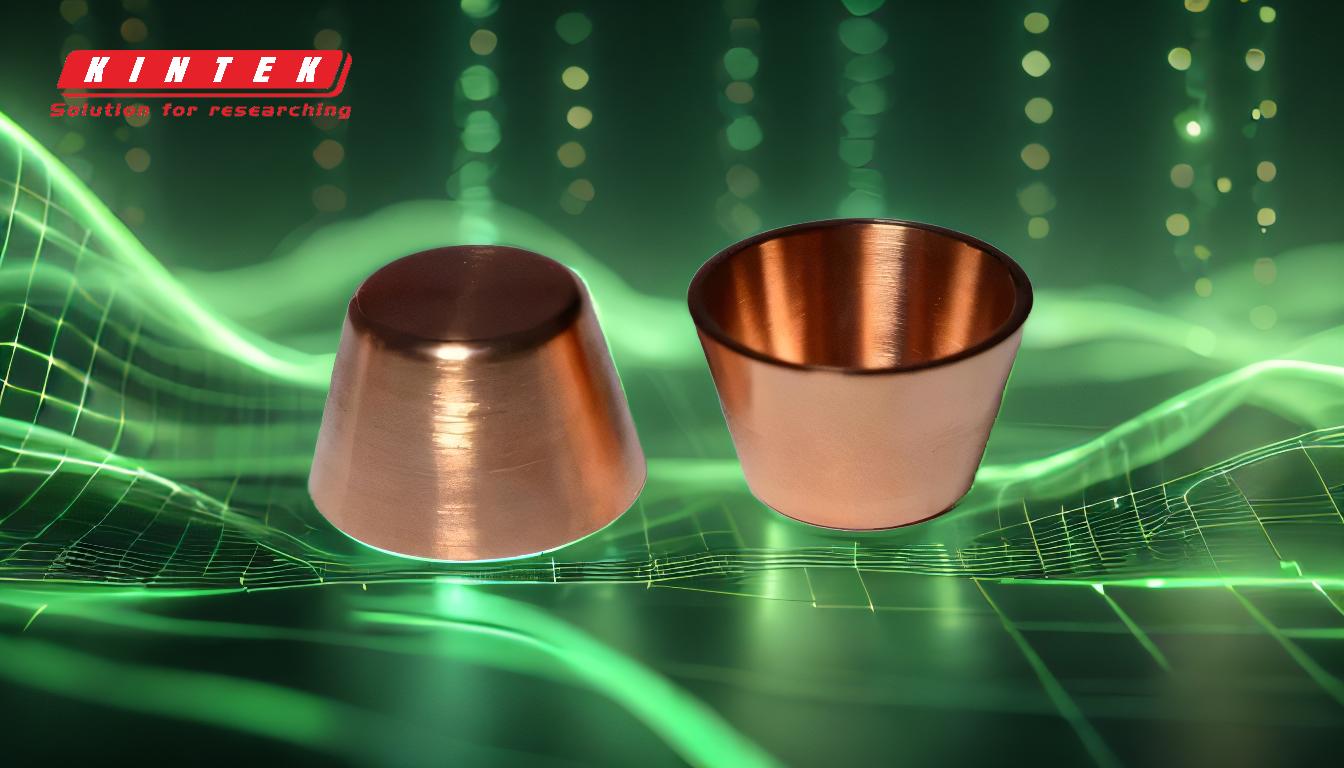
-
Basic Principle of Thermal Evaporation:
- Thermal evaporation involves heating a solid material in a high vacuum chamber until it vaporizes, producing a vapor pressure. The vacuum environment ensures that the vapor stream travels unimpeded to the substrate, where it condenses and forms a thin film or coating.
- This method is a form of physical vapor deposition (PVD), where the material transitions from a solid to a vapor phase and then back to a solid on the substrate.
-
Role of High Vacuum:
- The high vacuum environment is critical for the success of thermal evaporation. It minimizes the presence of other gases or particles that could interfere with the vapor stream, ensuring a clean and uniform deposition.
- In a vacuum, even a relatively low vapor pressure is sufficient to create a vapor cloud, allowing the material to travel and deposit efficiently.
-
Heating Methods:
- Electric Resistance Heating: A common method where an electric current passes through a resistive boat or basket, heating it to the point where the material melts and evaporates. This is suitable for materials with lower melting points.
- Electron Beam Evaporation: For materials with higher melting points, an electron beam is used to heat and vaporize the target material. This method provides precise control over the heating process.
- Tungsten Filament Heating: A filament made of tungsten or another high-melting-point material is used to heat and evaporate the coating substance.
-
Material Vaporization and Deposition:
- The material is heated to its melting point, causing it to evaporate and form a vapor cloud. The vapor stream then travels through the vacuum chamber and deposits onto the substrate.
- The deposited material condenses and forms a thin film, adhering to the substrate surface. The thickness and uniformity of the film depend on factors such as the evaporation rate, substrate temperature, and vacuum conditions.
-
Applications of Thermal Evaporation:
- Thermal evaporation is widely used in the fabrication of OLEDs (organic light-emitting diodes) and thin-film transistors, where precise and uniform coatings are essential.
- It is also used in optical coatings, such as anti-reflective layers, and in the deposition of metals and other materials for electronic devices.
-
Advantages of Thermal Evaporation:
- Simplicity: The process is relatively straightforward and easy to control, making it suitable for a wide range of materials and applications.
- High Purity: The high vacuum environment ensures minimal contamination, resulting in high-purity films.
- Versatility: Thermal evaporation can be used with a variety of materials, including metals, semiconductors, and organic compounds.
-
Limitations of Thermal Evaporation:
- Material Constraints: Some materials may decompose or react at high temperatures, limiting their suitability for thermal evaporation.
- Uniformity Challenges: Achieving uniform film thickness over large areas can be difficult, especially for complex geometries or multiple substrates.
-
Comparison with Other PVD Techniques:
- Thermal evaporation is one of the simplest and most cost-effective PVD methods. However, it may not be suitable for all materials or applications, particularly those requiring higher precision or more complex deposition processes.
- Other PVD techniques, such as sputtering or pulsed laser deposition, may offer better control over film properties but are often more complex and expensive.
In summary, thermal evaporation is a versatile and widely used technique for depositing thin films and coatings in a high vacuum environment. Its simplicity, high purity, and ability to work with a variety of materials make it a valuable tool in industries ranging from electronics to optics. However, careful consideration of material properties and process parameters is necessary to achieve optimal results.
Summary Table:
Aspect | Details |
---|---|
Basic Principle | Heating solid material in a vacuum to vaporize and deposit as a thin film. |
Heating Methods | Electric resistance, electron beam, or tungsten filament heating. |
Key Applications | OLEDs, thin-film transistors, optical coatings, and electronic devices. |
Advantages | Simplicity, high purity, and versatility with various materials. |
Limitations | Material constraints and uniformity challenges. |
Vacuum Importance | Ensures clean, uniform deposition by minimizing interference. |
Discover how thermal evaporation can enhance your thin film deposition process—contact our experts today!