Vacuum coating is a versatile and widely used process that applies thin layers of material to surfaces in a vacuum environment. This technology enhances the performance, durability, and aesthetics of various products across multiple industries. Key applications include improving energy efficiency in low-emissivity glass, enhancing durability in automotive and aerospace components, and enabling advanced functionality in electronic devices like solar cells and microchips. Additionally, vacuum coating is used for decorative purposes, scratch resistance, and protection in everyday items such as furniture, sporting goods, and packaging. Its ability to provide precise, high-quality coatings makes it indispensable in modern manufacturing and technology.
Key Points Explained:
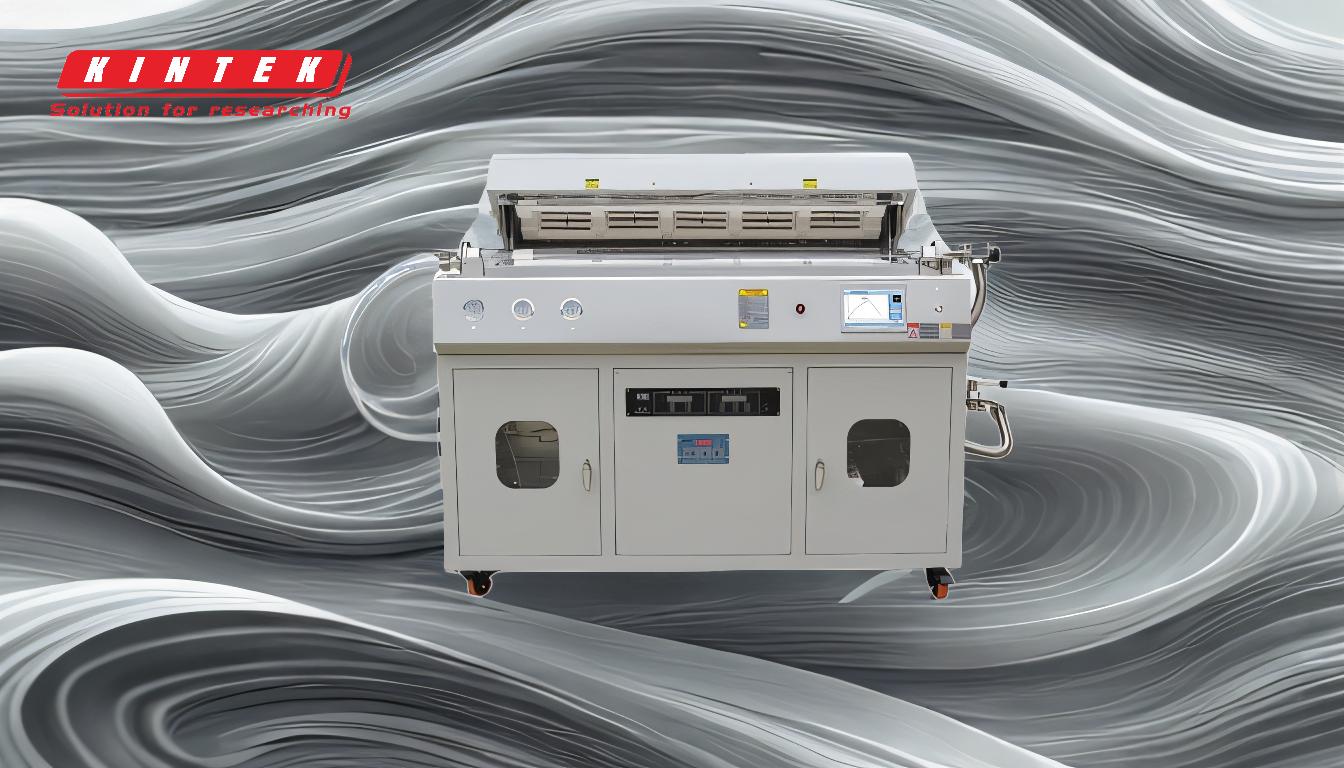
-
Enhancing Durability and Protection:
- Vacuum coating is used to apply thin, protective layers to surfaces, making them resistant to scratches, stains, and other forms of damage.
- Examples include coatings on cars, sporting goods, and furniture, which extend their lifespan and maintain their appearance.
- In industrial settings, hard coatings are applied to engine components and other machinery to improve wear resistance and durability.
-
Energy Efficiency and Sustainability:
- Vacuum coating plays a critical role in energy-saving applications, such as low-emissivity (low-E) glass used in windows. These coatings reduce heat transfer, improving insulation and energy efficiency in buildings.
- In solar cell manufacturing, vacuum deposition enhances the conductivity and light-harvesting properties of thin-film solar cells, improving their efficiency and durability.
-
Advanced Electronics and Technology:
- The process is essential in the production of electronic devices like microchips, LEDs, and flexible displays. It coats metal patterns that are critical for the functionality of these devices.
- Vacuum coating is also used to manufacture thin-film transistors, which are key components in flexible displays and sensors.
-
Decorative and Aesthetic Applications:
- Vacuum coating is widely used for decorative purposes on glass, metal, and plastics. It enhances the visual appeal of products like tableware, home furnishings, and building materials.
- The process can create reflective, metallic, or colored finishes, making it popular in consumer goods and packaging.
-
Specialized Industrial Applications:
- In the aerospace and automotive industries, vacuum coating is applied to carbon fiber composites and other materials to improve their performance and durability.
- Medical devices and equipment also benefit from vacuum coatings, which can provide biocompatibility, corrosion resistance, and improved functionality.
-
Versatility Across Materials:
- Vacuum coating can be applied to a wide range of materials, including glass, metal, plastics, and composites. This versatility makes it suitable for diverse applications across industries.
- Examples include ophthalmic coatings for eyewear and coatings for equipment in dairy sheds, which improve hygiene and durability.
-
Everyday Applications:
- The technology is integrated into many aspects of daily life, from electronic products to packaging materials. It enhances both the performance and aesthetics of these items.
- For example, vacuum-coated packaging can provide barrier properties, protecting contents from moisture and contaminants.
By leveraging vacuum coating, industries can achieve enhanced performance, durability, and aesthetics in their products, making it a cornerstone of modern manufacturing and technology.
Summary Table:
Key Applications | Benefits |
---|---|
Durability & Protection | Scratch resistance, extended lifespan, wear resistance for industrial use. |
Energy Efficiency | Low-E glass for insulation, improved solar cell efficiency. |
Advanced Electronics | Microchips, LEDs, flexible displays, and thin-film transistors. |
Decorative & Aesthetic Uses | Reflective, metallic, or colored finishes for consumer goods and packaging. |
Specialized Industrial Uses | Aerospace, automotive, and medical device coatings for enhanced performance. |
Versatility Across Materials | Applicable to glass, metal, plastics, and composites for diverse industries. |
Unlock the potential of vacuum coating for your industry—contact our experts today!