The voltage required for arcing, also known as the breakdown voltage, depends on several factors, including the distance between electrodes, the type of gas or medium between them, pressure, temperature, and electrode material. In air, the general rule of thumb is that it takes approximately 30,000 volts per centimeter to create an arc, but this can vary significantly based on conditions. For example, at standard temperature and pressure (STP), the breakdown voltage in air is roughly 3,000 volts per millimeter. However, this value decreases in high-pressure environments or with specific gases like sulfur hexafluoride (SF6), which has a higher dielectric strength. Understanding these variables is crucial for designing electrical systems, ensuring safety, and preventing unintended arcing.
Key Points Explained:
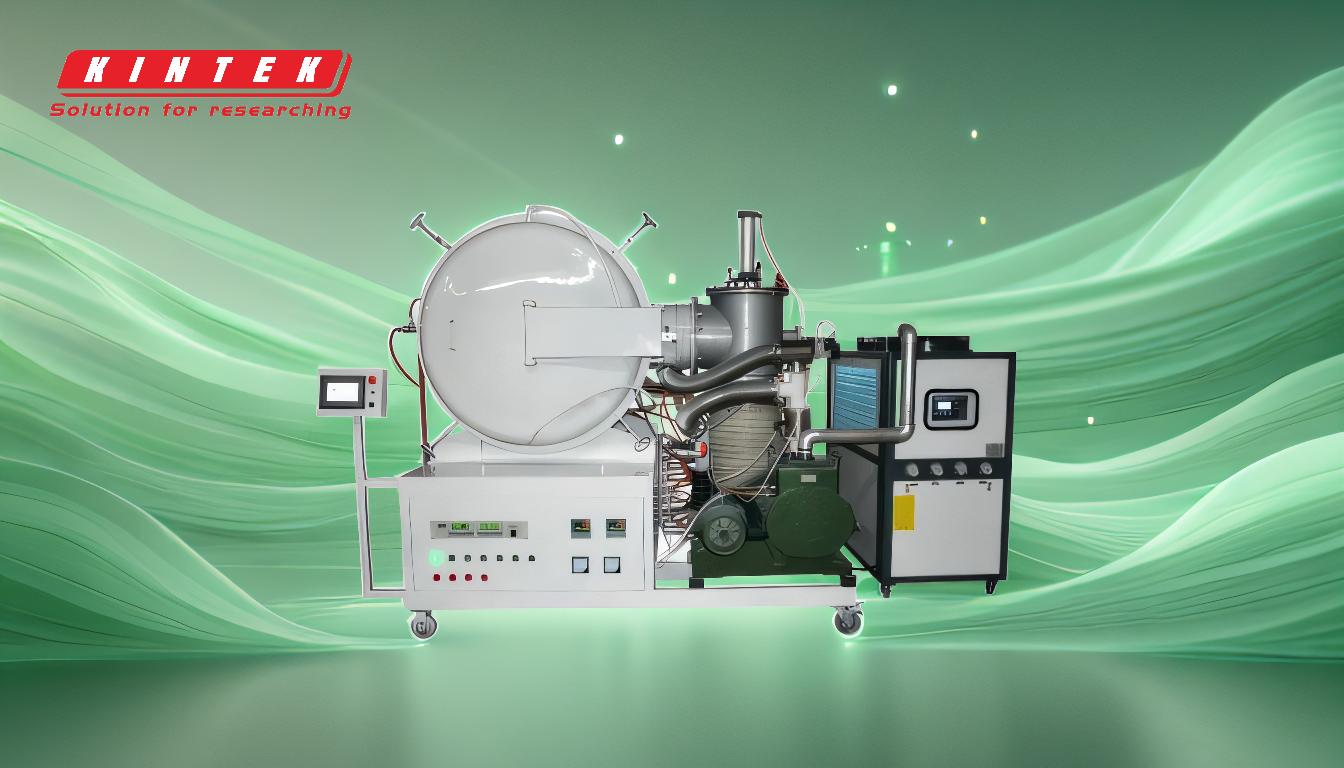
-
Definition of Arcing Voltage
- Arcing voltage, or breakdown voltage, is the minimum voltage required to ionize a medium (e.g., air, gas, or vacuum) and create an electrical arc between two electrodes.
- This phenomenon occurs when the electric field strength exceeds the dielectric strength of the medium, allowing electrons to flow and form a conductive path.
-
Factors Influencing Arcing Voltage
- Electrode Distance (Gap): The voltage required increases with the distance between electrodes. For example, in air, the breakdown voltage is approximately 30 kV/cm.
- Medium (Gas or Material): Different gases have varying dielectric strengths. For instance, sulfur hexafluoride (SF6) has a much higher dielectric strength than air, requiring higher voltages for arcing.
- Pressure and Temperature: Higher pressure generally increases the breakdown voltage, while higher temperatures can reduce it.
- Electrode Shape and Material: Sharp or pointed electrodes can lower the breakdown voltage due to localized electric field enhancement.
-
Breakdown Voltage in Air
- At standard temperature and pressure (STP), the breakdown voltage in air is roughly 3,000 volts per millimeter (or 30 kV/cm).
- This value is a general guideline and can vary depending on humidity, air purity, and other environmental factors.
-
Paschen's Law
- Paschen's Law describes the relationship between breakdown voltage, gas pressure, and electrode distance.
- It states that the breakdown voltage is a function of the product of gas pressure and electrode gap distance.
- For example, at low pressures or very small gaps, the breakdown voltage decreases due to reduced collision frequency between electrons and gas molecules.
-
Applications and Safety Considerations
- Understanding arcing voltage is critical in designing electrical insulation systems, circuit breakers, and high-voltage equipment.
- Engineers must account for factors like humidity, contamination, and altitude to prevent unintended arcing, which can cause equipment damage or safety hazards.
- For example, in high-voltage transmission lines, maintaining sufficient clearance between conductors is essential to avoid arcing.
-
Examples of Breakdown Voltages in Different Media
- Air: ~30 kV/cm at STP.
- Sulfur Hexafluoride (SF6): ~89 kV/cm, making it ideal for use in high-voltage circuit breakers.
- Vacuum: Extremely high breakdown voltage due to the absence of gas molecules, often used in vacuum interrupters.
- Oil (Transformer Oil): ~10-20 kV/mm, commonly used in transformers for insulation.
-
Practical Implications for Equipment Design
- Engineers must consider the operating environment when designing electrical systems. For example, in high-altitude areas, the reduced air density lowers the breakdown voltage, requiring larger clearances.
- Specialized gases like SF6 are used in high-voltage equipment to increase dielectric strength and prevent arcing.
- Insulation materials and coatings are applied to electrodes to reduce the risk of arcing in sensitive applications.
-
Safety Measures to Prevent Arcing
- Maintaining Clearances: Ensuring adequate spacing between conductive parts to prevent arcing.
- Using Dielectric Materials: Incorporating materials with high dielectric strength to insulate components.
- Environmental Controls: Regulating humidity, temperature, and pressure in sensitive environments.
- Regular Maintenance: Inspecting equipment for contamination, wear, or damage that could lower the breakdown voltage.
By understanding the principles of arcing voltage and the factors that influence it, engineers and equipment purchasers can make informed decisions to ensure the safety, reliability, and efficiency of electrical systems.
Summary Table:
Factor | Influence on Arcing Voltage |
---|---|
Electrode Distance (Gap) | Increases with distance (~30 kV/cm in air). |
Medium (Gas or Material) | Varies by dielectric strength (e.g., SF6: ~89 kV/cm). |
Pressure and Temperature | Higher pressure increases voltage; higher temperature reduces it. |
Electrode Shape/Material | Sharp or pointed electrodes lower voltage due to localized field enhancement. |
Breakdown Voltage | Air: ~3,000 V/mm at STP; SF6: ~89 kV/cm; Vacuum: Extremely high; Oil: ~10-20 kV/mm. |
Ensure your electrical systems are safe and efficient—contact our experts today for tailored solutions!