Thin film vapor deposition is a process used to create thin layers of material on a substrate, typically within a vacuum chamber. This technique is essential in various industries, including semiconductors, optics, aerospace, and biomedical devices. The process involves vaporizing chemical precursors, which then react on the substrate surface to form a high-performance thin film coating. Thin film vapor deposition is used for applications such as improving optical properties, enhancing electrical conductivity, creating anti-corrosive coatings, and enabling the development of advanced technologies like solar cells, quantum computers, and biomedical devices. The method varies depending on the specific technique used, such as chemical vapor deposition (CVD), thermal evaporation, or sputtering.
Key Points Explained:
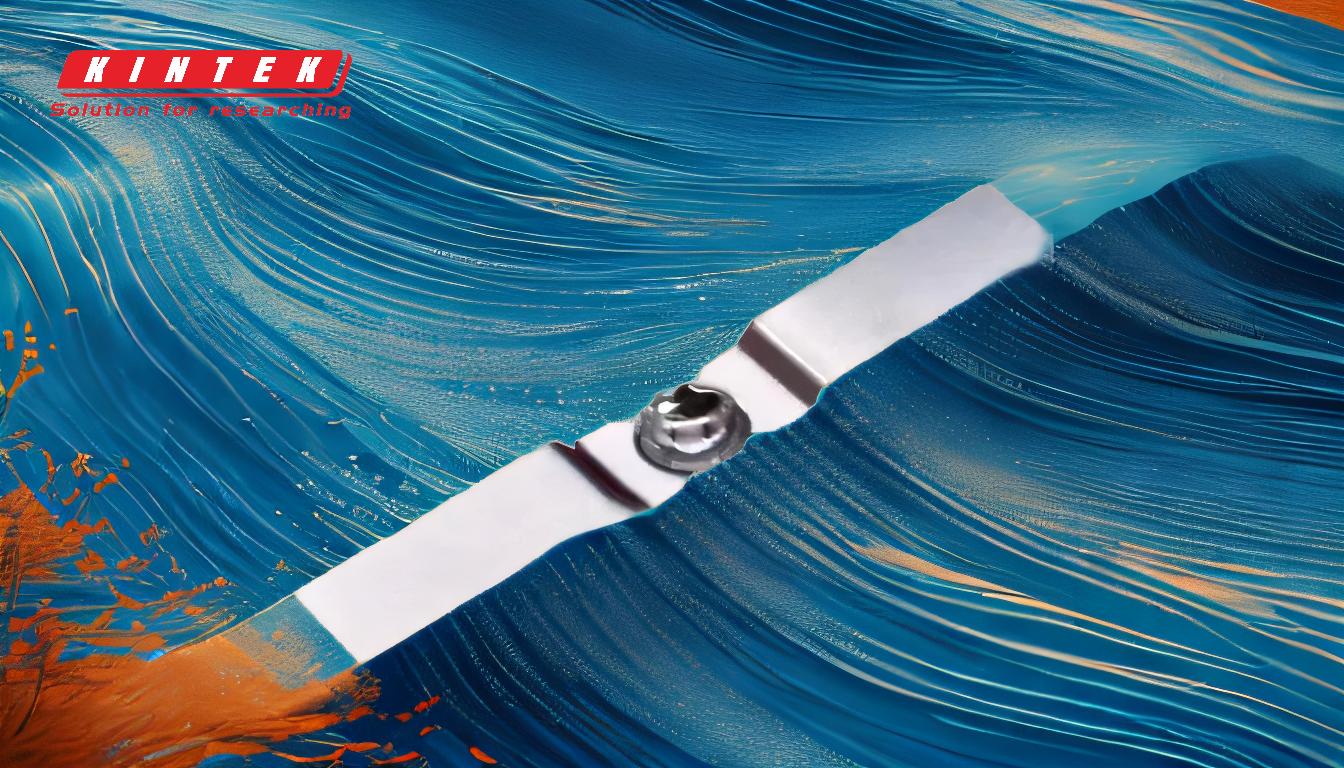
-
Definition of Thin Film Vapor Deposition:
- Thin film vapor deposition is a process where a thin layer of material is deposited onto a substrate within a vacuum chamber.
- It involves vaporizing chemical precursors, which then react on the substrate surface to form a thin film.
-
Techniques Used in Thin Film Vapor Deposition:
- Chemical Vapor Deposition (CVD): Involves heating chemical precursors to vaporize them, causing a chemical reaction on the substrate surface to form a thin film.
- Thermal Evaporation: Uses heat to vaporize a material, which then condenses on the substrate to form a thin film.
- Sputtering: Involves bombarding a target material with ions to eject atoms, which then deposit onto the substrate.
- Ion Beam Deposition: Uses an ion beam to sputter material from a target, which then deposits onto the substrate.
-
Applications of Thin Film Vapor Deposition:
- Optical Coatings: Used to improve the transmission, refraction, and reflection properties of lenses and plate glass.
- Semiconductor Industry: Enhances conductance or insulation in semiconductor devices and integrated circuits.
- Anti-Corrosive Coatings: Creates ceramic thin films for sensors and other devices to protect against corrosion.
- Advanced Technologies: Enables the development of ultra-small structures like batteries, solar cells, drug delivery systems, and quantum computers.
- Decorative and Functional Coatings: Used for decorative finishes, electrical coatings, and other functional applications.
-
Industries Utilizing Thin Film Vapor Deposition:
- Semiconductors: Essential for growing electronic materials and improving device performance.
- Aerospace: Forms thermal and chemical barrier coatings to protect against corrosive environments.
- Optics: Imparts desired reflective and transmissive properties to substrates.
- Biomedical Devices: Used in medical electronics and devices for improved performance and durability.
- Consumer Electronics: Enhances the functionality and durability of a wide range of electronic devices.
-
Benefits of Thin Film Vapor Deposition:
- High-Performance Coatings: Produces coatings with superior properties such as hardness, corrosion resistance, and heat resistance.
- Precision and Control: Allows for precise control over the thickness and composition of the deposited films.
- Versatility: Applicable to a wide range of materials and substrates, making it suitable for diverse applications.
-
Future Trends and Innovations:
- Nanotechnology: Continued development of ultra-small structures and devices.
- Sustainable Energy: Advancements in solar cells and energy storage devices.
- Biomedical Applications: Enhanced drug delivery systems and biocompatible coatings for medical devices.
In summary, thin film vapor deposition is a versatile and essential process used across various industries to create high-performance coatings and enable the development of advanced technologies. Its applications range from improving optical properties to enhancing the functionality of electronic and biomedical devices.
Summary Table:
Aspect | Details |
---|---|
Definition | Process of depositing thin material layers on a substrate in a vacuum. |
Techniques | CVD, thermal evaporation, sputtering, ion beam deposition. |
Applications | Optical coatings, semiconductors, anti-corrosion, advanced technologies. |
Industries | Semiconductors, aerospace, optics, biomedical, consumer electronics. |
Benefits | High-performance coatings, precision, versatility. |
Future Trends | Nanotechnology, sustainable energy, biomedical advancements. |
Discover how thin film vapor deposition can transform your industry—contact us today for expert guidance!