A twin-chamber furnace, specifically the Twin-Chamber Melting Furnace (TCF®), is a specialized type of furnace designed with two distinct chambers—a heating chamber and a scrap chamber—housed within a single furnace casing. These chambers share a common melt bath but operate with separate atmospheres, allowing for efficient and controlled melting processes. This design is particularly useful in industries requiring precise temperature control and separation of materials during heating. Twin-chamber furnaces are versatile and find applications in fields such as metallurgy, ceramics, electronics, and materials research, where processes like sintering, annealing, and heat treatment are essential.
Key Points Explained:
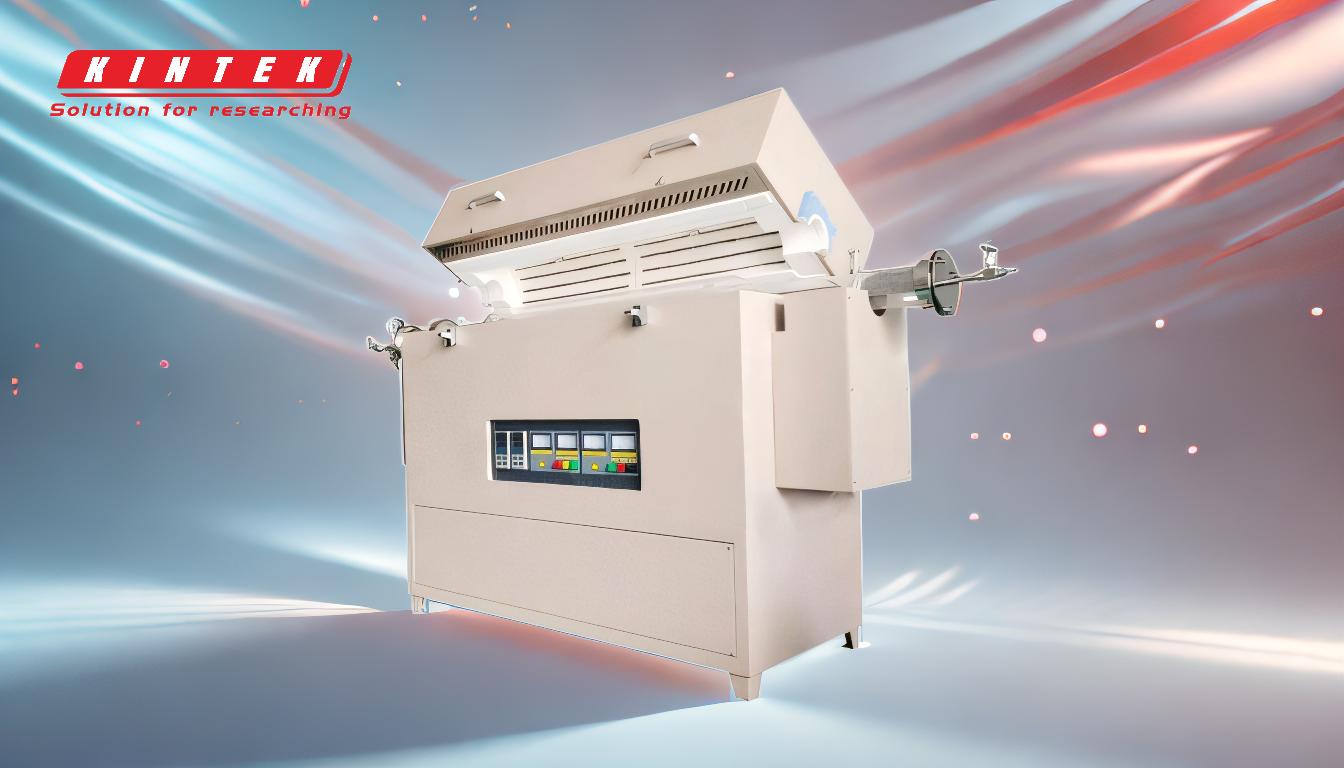
-
Structure of the Twin-Chamber Furnace:
- The furnace consists of two chambers: a heating chamber and a scrap chamber, both housed within a single furnace casing.
- These chambers share a common melt bath, which allows for efficient heat transfer and material processing.
- The atmospheres within the two chambers are separated, enabling distinct environmental conditions for different materials or processes.
-
Functionality and Applications:
- Heating Chamber: Used for high-temperature processes such as melting, sintering, and annealing. It ensures precise temperature control, which is critical for material properties.
- Scrap Chamber: Designed to handle raw or scrap materials, which are then melted or processed in the shared melt bath. This separation allows for efficient recycling and reuse of materials.
- Twin-chamber furnaces are widely used in industries such as metallurgy, ceramics, electronics, and materials research. They are ideal for processes like powder roasting, ceramic sintering, high-temperature experiments, and material treatment.
-
Advantages of Twin-Chamber Design:
- Efficiency: The shared melt bath reduces energy consumption by allowing heat to be transferred directly between the chambers.
- Versatility: The separation of atmospheres enables the furnace to handle different materials or processes simultaneously without cross-contamination.
- Precision: The design allows for precise control over temperature and atmosphere, which is crucial for achieving desired material properties.
-
Comparison with Other Furnace Types:
- Muffle Furnaces: Used for high-temperature applications like ashing, annealing, and material testing. Unlike twin-chamber furnaces, muffle furnaces typically have a single chamber and are used for smaller-scale processes.
- Vacuum Chamber Furnaces: Designed for heat treatment under low vacuum or controlled atmospheres. These are used for specialized applications like metal heat treatment and are not typically designed for melting or large-scale material processing.
- Laboratory Furnaces: General-purpose furnaces used for a wide range of applications, including drying, curing, and heat treatment. Twin-chamber furnaces, on the other hand, are more specialized and suited for industrial-scale melting and material processing.
-
Key Features of Twin-Chamber Furnaces:
- Temperature Control: Advanced temperature control systems ensure precise heating, which is essential for processes like sintering and annealing.
- Material Compatibility: Suitable for a wide range of materials, including metals, ceramics, and special alloys.
- Atmosphere Control: The ability to maintain separate atmospheres in the two chambers allows for processes that require different environmental conditions, such as oxidation or reduction.
-
Industrial and Scientific Applications:
- Metallurgy: Used for melting and refining metals, as well as for heat treatment processes like annealing and tempering.
- Ceramics: Ideal for sintering ceramic materials and conducting high-temperature experiments.
- Electronics: Used in the production of electronic components that require precise temperature control.
- Materials Research: Essential for studying the properties of materials at high temperatures and for developing new materials.
-
Operational Considerations:
- Energy Efficiency: The shared melt bath design reduces energy consumption, making the furnace more cost-effective for large-scale operations.
- Maintenance: Regular maintenance is required to ensure the longevity of the furnace, particularly for the heating elements and temperature control systems.
- Safety: Proper safety protocols must be followed, especially when handling high-temperature materials and maintaining separate atmospheres.
In summary, the twin-chamber furnace is a highly specialized and efficient piece of equipment designed for industrial and scientific applications that require precise temperature and atmosphere control. Its unique design, featuring a shared melt bath and separate atmospheres, makes it a versatile and valuable tool in fields ranging from metallurgy to materials research.
Summary Table:
Feature | Description |
---|---|
Structure | Two chambers (heating and scrap) with a shared melt bath and separate atmospheres. |
Applications | Metallurgy, ceramics, electronics, and materials research. |
Advantages | High efficiency, versatility, and precise temperature control. |
Key Features | Advanced temperature control, material compatibility, and atmosphere separation. |
Operational Benefits | Energy-efficient, cost-effective, and safe for high-temperature processes. |
Interested in how a twin-chamber furnace can enhance your industrial processes? Contact us today to learn more!