High-temperature heating is a critical process in industries such as metallurgy, ceramics, and material testing. It involves the use of specialized materials and equipment capable of withstanding extreme temperatures while maintaining performance and durability. Key materials used for high-temperature heating include tantalum, graphite, platinum, tungsten disilicide, molybdenum disilicide, molybdenum, and silicon carbide. These materials are chosen for their high melting points, corrosion resistance, and thermal stability. High-temperature furnaces, such as tube furnaces, vacuum furnaces, box furnaces, and muffle furnaces, are designed with strategically placed heating elements to ensure uniform heat distribution. These systems are essential for processes like sintering, melting, and brazing, where precise temperature control is crucial.
Key Points Explained:
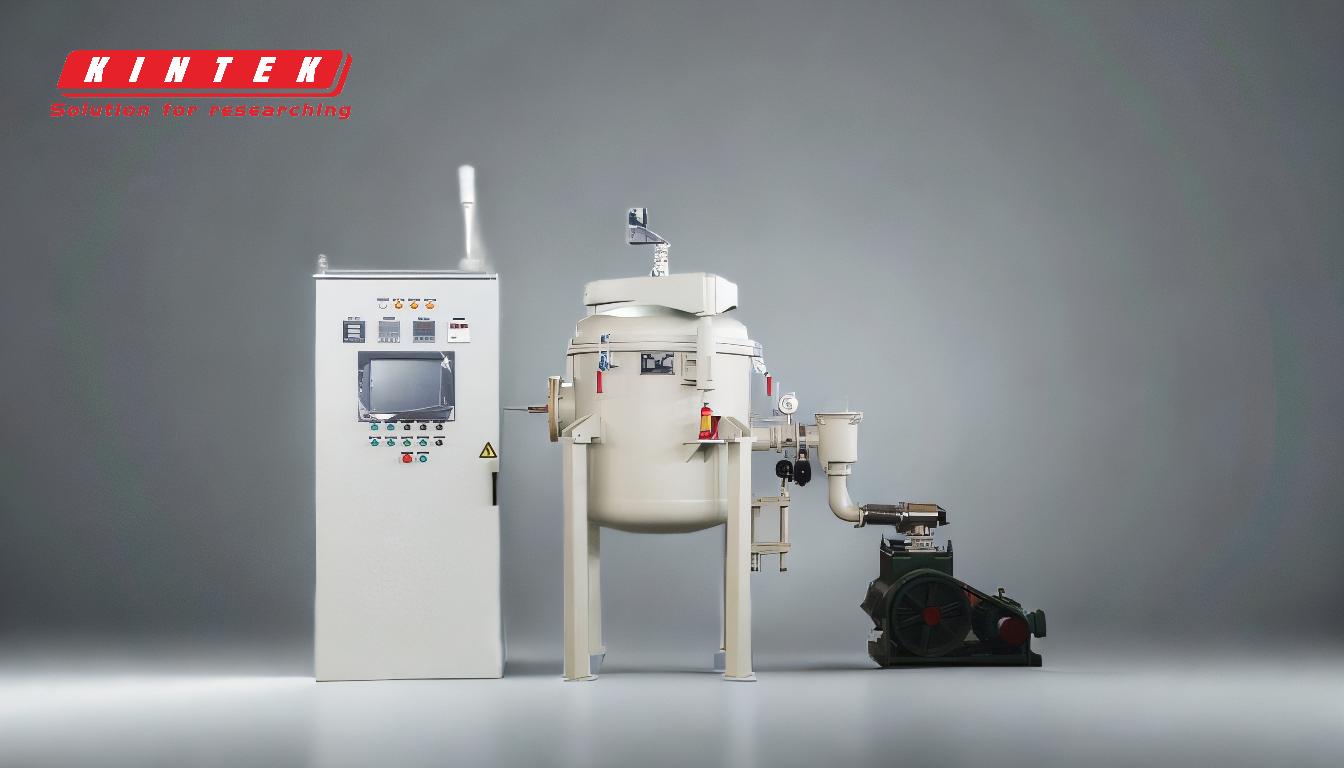
-
Materials Used for High-Temperature Heating
- Tantalum and Graphite: These materials are used in applications above 1482°C (2700°F) due to their high melting points and resistance to corrosion. They are ideal for environments where extreme heat and chemical stability are required.
- Platinum, Tungsten Disilicide, Molybdenum Disilicide, Molybdenum, and Silicon Carbide: These exotic materials are commonly used in heating elements for high-temperature furnaces. They offer excellent thermal conductivity and durability, making them suitable for processes like sintering, hardening, and brazing.
-
Types of High-Temperature Furnaces
- Tube Furnaces: Designed for processes requiring uniform heating along a cylindrical chamber, tube furnaces are used in material testing and chemical synthesis.
- Vacuum Furnaces: These furnaces operate in a vacuum environment, preventing oxidation and contamination. They are ideal for processes like brazing and heat treatment.
- Box Furnaces: Known for their versatility, box furnaces are used for sintering, annealing, and other heat treatment processes.
- Muffle Furnaces: Equipped with a separate heating chamber, muffle furnaces are used for high-temperature processes that require isolation from combustion byproducts.
-
Heating Methods
- Fuel-Powered Furnaces: These are the most common due to their cost-effectiveness. They generate heat by burning fuels like natural gas or oil.
- Electric Furnaces: While more expensive to operate, electric furnaces are preferred for specific processes where precise temperature control and clean heating environments are required.
-
Applications of High-Temperature Heating
- Hardening: A process that increases the hardness of metals by heating them to high temperatures and then rapidly cooling them.
- Sintering: The process of compacting and forming a solid mass of material by heat or pressure without melting it to the point of liquefaction.
- Nickel or Copper Brazing: A joining process that uses a filler metal with a melting point above 450°C (842°F) to bond materials.
-
Importance of Temperature Uniformity
- High-temperature furnaces are designed with strategically positioned heating elements to ensure uniform heat distribution. This uniformity is critical for processes like fusion, sintering, and melting, where inconsistent temperatures can lead to material defects or process failures.
By understanding the materials, equipment, and methods used in high-temperature heating, purchasers can make informed decisions to meet their specific industrial needs.
Summary Table:
Aspect | Details |
---|---|
Key Materials | Tantalum, Graphite, Platinum, Tungsten Disilicide, Molybdenum, Silicon Carbide |
Furnace Types | Tube Furnaces, Vacuum Furnaces, Box Furnaces, Muffle Furnaces |
Heating Methods | Fuel-Powered, Electric |
Applications | Hardening, Sintering, Nickel or Copper Brazing |
Temperature Uniformity | Critical for processes like fusion, sintering, and melting |
Need expert advice on high-temperature heating solutions? Contact us today!