Blacksmiths use a variety of presses to shape and manipulate metal, with hydraulic presses being the most common due to their power and precision. These presses are essential for tasks such as forging, bending, and stamping metal. Hydraulic presses use fluid pressure to generate force, making them highly efficient for heavy-duty work. Additionally, mechanical presses and screw presses are also used, depending on the specific requirements of the blacksmith. Each type of press offers unique advantages, such as speed, control, or simplicity, allowing blacksmiths to choose the best tool for their particular needs.
Key Points Explained:
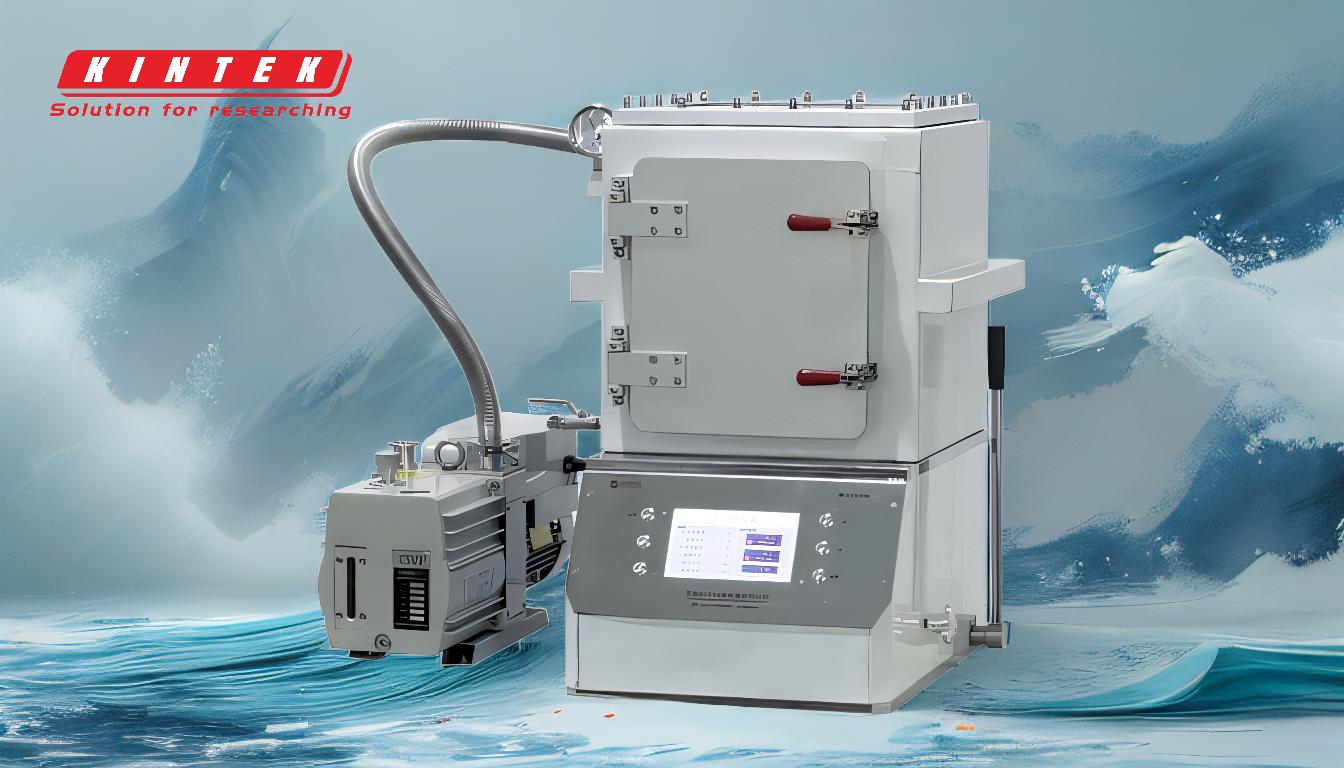
-
Hydraulic Presses:
- Functionality: Hydraulic presses are the most widely used type of press in blacksmithing. They operate by using hydraulic fluid to create pressure, which is then used to exert force on the metal. This allows for precise control over the amount of force applied, making them ideal for detailed work.
-
Advantages:
- Power: Hydraulic presses can generate a significant amount of force, making them suitable for heavy-duty tasks.
- Control: The ability to precisely control the pressure allows for more intricate designs and consistent results.
- Versatility: These presses can be used for a variety of tasks, including forging, bending, and stamping.
-
Mechanical Presses:
- Functionality: Mechanical presses use a mechanical system, such as a flywheel or a crank, to generate force. These presses are typically faster than hydraulic presses but may offer less control over the force applied.
-
Advantages:
- Speed: Mechanical presses can operate at higher speeds, making them suitable for tasks that require rapid repetition.
- Simplicity: These presses are often simpler in design, which can make them easier to maintain and repair.
- Cost-Effectiveness: Mechanical presses are generally less expensive than hydraulic presses, making them a good option for blacksmiths on a budget.
-
Screw Presses:
- Functionality: Screw presses use a large screw mechanism to apply force. The screw is turned either manually or with the help of a motor, which drives the ram down onto the metal.
-
Advantages:
- Control: Screw presses offer excellent control over the force applied, similar to hydraulic presses.
- Durability: These presses are known for their durability and long lifespan, making them a reliable choice for blacksmiths.
- Manual Operation: Some screw presses can be operated manually, which can be advantageous in situations where power sources are limited.
-
Choosing the Right Press:
- Task Requirements: The choice of press depends largely on the specific tasks the blacksmith needs to perform. For heavy-duty forging, a hydraulic press might be the best option, while a mechanical press could be more suitable for high-speed stamping.
- Workspace Constraints: The size and layout of the blacksmith's workspace can also influence the choice of press. Hydraulic presses, for example, require more space and a stable power source.
- Budget Considerations: Budget is another important factor. While hydraulic presses offer superior control and power, they are also more expensive. Mechanical and screw presses can be more cost-effective alternatives.
-
Maintenance and Safety:
- Regular Maintenance: Regardless of the type of press, regular maintenance is crucial to ensure safe and efficient operation. This includes checking hydraulic fluid levels, inspecting mechanical components, and ensuring that all safety features are functioning correctly.
- Safety Precautions: Blacksmiths should always follow safety guidelines when operating presses. This includes wearing appropriate protective gear, ensuring that the workspace is clear of obstacles, and being aware of the press's operational limits.
In summary, blacksmiths use a variety of presses, each with its own set of advantages and disadvantages. Hydraulic presses are the most common due to their power and precision, but mechanical and screw presses also have their place in the blacksmith's workshop. The choice of press depends on the specific needs of the blacksmith, including the type of work being done, the available workspace, and budget considerations. Proper maintenance and safety precautions are essential for the safe and effective use of any press.
Summary Table:
Press Type | Functionality | Advantages |
---|---|---|
Hydraulic | Uses hydraulic fluid to create pressure for precise force control. | - High power for heavy-duty tasks - Excellent control for intricate designs |
Mechanical | Operates using a mechanical system like a flywheel or crank for rapid force. | - High speed for repetitive tasks - Simple design, cost-effective |
Screw | Applies force via a screw mechanism, manually or with a motor. | - Precise control - Durable and reliable |
Ready to choose the right press for your blacksmithing needs? Contact our experts today for personalized advice!