Brazing is a versatile joining process that utilizes various machines and heating methods depending on the application, materials, and desired outcomes. The most common machines used for brazing include torch brazing equipment, furnace brazing systems (such as vacuum or controlled atmosphere furnaces), induction brazing machines, and resistance brazing setups. Each method has its unique advantages, such as precision, scalability, or suitability for specific materials like aluminum-silicon alloys, copper, or gold-silver-nickel alloys. Industries like aerospace, automotive, electronics, and medical devices rely on these machines to produce high-quality, durable joints for critical components such as turbine blades, fuel injectors, and surgical instruments.
Key Points Explained:
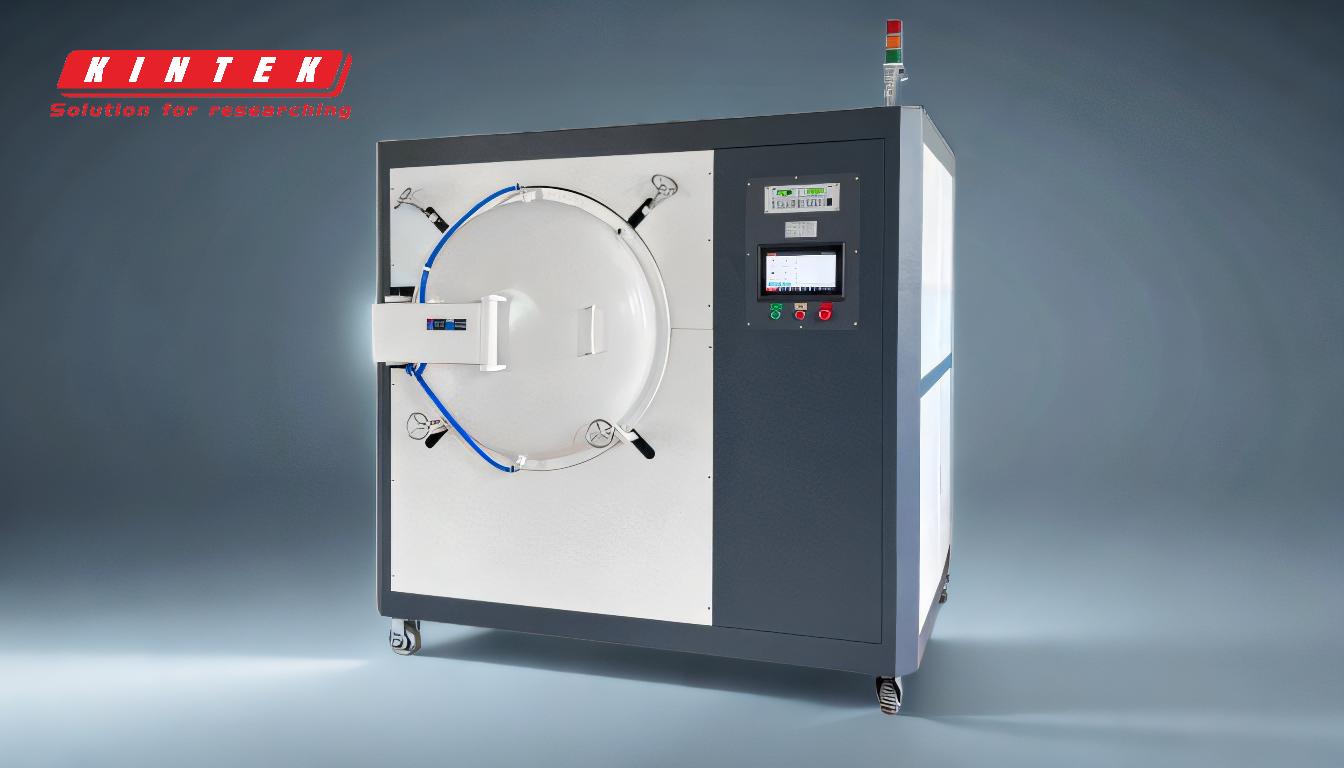
-
Torch Brazing:
- Torch brazing is one of the most common and straightforward methods, using a gas-fueled torch to heat the filler metal and base materials.
- It is ideal for small-scale or manual operations and is widely used in repair work or on-site applications.
- The equipment is portable and relatively inexpensive, making it accessible for various industries.
-
Furnace Brazing:
- Furnace brazing is a highly controlled process performed in specialized furnaces, such as batch or continuous furnaces.
- It is suitable for mass production and complex assemblies, ensuring uniform heating and consistent joint quality.
- Types of furnace brazing include:
- Vacuum Furnace Brazing: Uses a vacuum environment to prevent oxidation, ideal for materials like titanium and stainless steel. Commonly used in aerospace and medical industries.
- Controlled Atmosphere Furnace Brazing: Employs gases like hydrogen or argon to create an inert environment, preventing contamination and oxidation.
-
Induction Brazing:
- Induction brazing uses electromagnetic induction to generate heat in the workpiece, allowing for precise and localized heating.
- It is highly efficient and suitable for high-volume production, particularly in the automotive and electronics industries.
- The process is fast and minimizes thermal distortion, making it ideal for delicate components.
-
Resistance Brazing:
- Resistance brazing relies on electrical resistance to generate heat at the joint interface.
- It is commonly used for small parts and assemblies, offering quick heating cycles and high repeatability.
- This method is often employed in the electronics industry for joining components like connectors and terminals.
-
Dip Brazing:
- Dip brazing involves immersing the assembly in a molten salt or metal bath to achieve brazing temperatures.
- It is particularly effective for joining complex geometries and is widely used in the automotive and aerospace industries.
- The process ensures uniform heating and is suitable for high-volume production.
-
Infrared and Laser Brazing:
- Infrared brazing uses focused infrared radiation to heat the joint, offering precise control and minimal heat-affected zones.
- Laser brazing employs a high-energy laser beam for localized heating, ideal for joining thin or delicate materials.
- Both methods are used in advanced manufacturing, particularly in the electronics and medical device industries.
-
Applications Across Industries:
- Aerospace: Vacuum brazing is used for turbine blades, fuel piping, and heat exchangers due to its ability to produce strong, oxidation-free joints.
- Automotive: Exhaust pipes, sensors, and fuel injectors are often brazed using induction or furnace brazing for durability and reliability.
- Electronics: Printed circuit boards and electronic components are joined using resistance or laser brazing for precision and minimal thermal impact.
- Medical Devices: Artificial joints and surgical instruments are brazed in vacuum furnaces to ensure biocompatibility and high strength.
-
Filler Metals:
- The choice of filler metal depends on the base materials and application requirements. Common filler metals include:
- Aluminum-silicon alloys for aluminum components.
- Copper, copper-silver, and copper-zinc (brass) for general-purpose brazing.
- Gold-silver-nickel alloys for high-temperature applications.
- Amorphous brazing foils containing nickel, iron, copper, silicon, boron, and phosphorus for specialized uses.
- The choice of filler metal depends on the base materials and application requirements. Common filler metals include:
By understanding the specific requirements of the application, such as material compatibility, joint strength, and production volume, the appropriate brazing machine and method can be selected to achieve optimal results.
Summary Table:
Brazing Method | Key Features | Applications |
---|---|---|
Torch Brazing | Portable, cost-effective, ideal for small-scale or repair work | Repair work, on-site applications |
Furnace Brazing | Uniform heating, mass production, controlled environment | Aerospace, medical devices, complex assemblies |
Induction Brazing | Precise, localized heating, high efficiency, minimal thermal distortion | Automotive, electronics, high-volume production |
Resistance Brazing | Quick heating cycles, high repeatability, suitable for small parts | Electronics, connectors, terminals |
Dip Brazing | Uniform heating, effective for complex geometries, high-volume production | Automotive, aerospace |
Infrared & Laser Brazing | Precise control, minimal heat-affected zones, ideal for thin materials | Electronics, medical devices, advanced manufacturing |
Need help choosing the right brazing machine for your application? Contact our experts today for personalized advice!