Heat treatment is a critical process in metallurgy that can significantly alter the properties of metals and alloys. By controlling factors such as heating temperature, cooling rate, and diffusion, heat treatment can enhance or modify mechanical and physical properties. These changes include improvements in strength, hardness, ductility, toughness, wear resistance, elasticity, and even magnetic properties (permeability). The process works by manipulating the microstructure of the metal, which directly influences its performance characteristics. Understanding these changes is essential for selecting the right heat treatment process to achieve desired material properties for specific applications.
Key Points Explained:
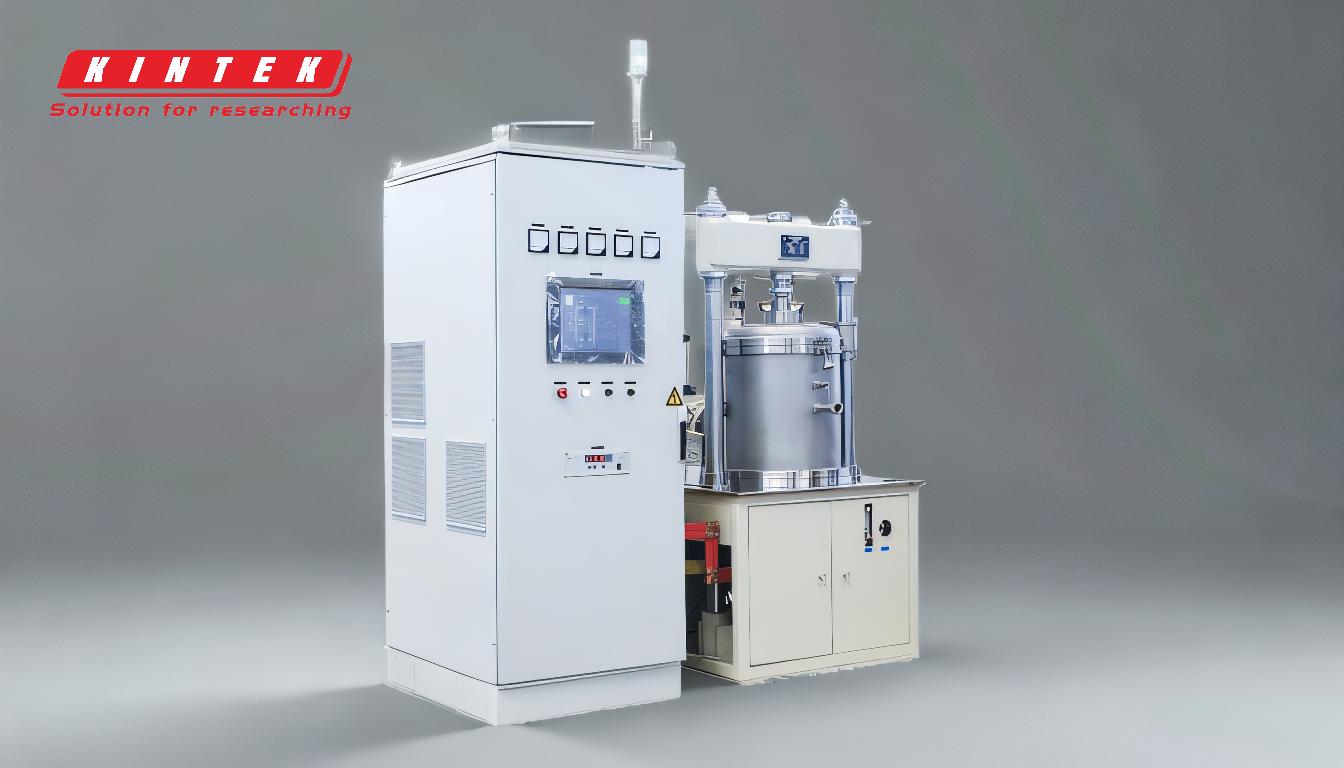
-
Strength:
- Heat treatment can increase the strength of a metal by altering its microstructure. For example, processes like quenching and tempering can create a fine-grained structure that resists deformation under stress.
- This is particularly important in applications where the material must withstand high loads or forces without failing.
-
Hardness:
- Hardness refers to a material's resistance to indentation or scratching. Heat treatment methods such as hardening (quenching) can significantly increase hardness by forming martensite, a hard and brittle phase in steel.
- This property is crucial for tools, cutting instruments, and wear-resistant components.
-
Ductility:
- Ductility is the ability of a material to deform plastically without breaking. Heat treatment can either increase or decrease ductility, depending on the process. For instance, annealing improves ductility by reducing internal stresses and refining the grain structure.
- This is important for materials that need to be shaped or formed without cracking.
-
Toughness:
- Toughness is the ability of a material to absorb energy and plastically deform without fracturing. Heat treatment processes like tempering can enhance toughness by reducing brittleness while maintaining adequate strength.
- This property is vital for components subjected to impact or shock loads.
-
Wear Resistance:
- Wear resistance is the ability of a material to withstand surface degradation due to friction or abrasion. Heat treatment can improve wear resistance by increasing surface hardness or creating a hardened outer layer through processes like case hardening.
- This is essential for gears, bearings, and other moving parts.
-
Elasticity:
- Elasticity refers to a material's ability to return to its original shape after being deformed. Heat treatment can modify elasticity by altering the microstructure to achieve a balance between stiffness and flexibility.
- This is important for springs, wires, and other components that require resilience.
-
Magnetism (Permeability):
- Heat treatment can influence the magnetic properties of metals, such as permeability, which is the ability to support the formation of a magnetic field. Processes like annealing can optimize magnetic properties for applications in electrical and electronic devices.
- This is critical for transformers, motors, and other magnetic components.
-
Microstructural Changes:
- The key to altering these properties lies in controlling the microstructure of the metal. Heat treatment processes manipulate phase transformations, grain size, and dislocation density, which directly impact mechanical and physical properties.
- For example, rapid cooling (quenching) can create a hard martensitic structure, while slow cooling (annealing) can produce a softer, more ductile microstructure.
-
Cooling Rate and Diffusion:
- The rate of cooling and diffusion during heat treatment plays a crucial role in determining the final properties of the material. Faster cooling rates generally lead to harder and stronger materials, while slower cooling rates promote ductility and toughness.
- Understanding these factors allows engineers to tailor heat treatment processes to achieve specific performance requirements.
By carefully selecting and controlling heat treatment processes, manufacturers can optimize the properties of metals and alloys to meet the demands of various applications, from automotive components to aerospace structures.
Summary Table:
Property | Effect of Heat Treatment | Key Applications |
---|---|---|
Strength | Increases resistance to deformation through processes like quenching and tempering. | High-load components, structural parts. |
Hardness | Enhances resistance to indentation and scratching via hardening (quenching). | Tools, cutting instruments, wear-resistant parts. |
Ductility | Improves ability to deform without breaking through annealing. | Shaping and forming applications. |
Toughness | Balances strength and brittleness with tempering for impact resistance. | Shock-absorbing components. |
Wear Resistance | Increases surface hardness or creates hardened layers via case hardening. | Gears, bearings, moving parts. |
Elasticity | Adjusts microstructure for optimal stiffness and flexibility. | Springs, wires, resilient components. |
Magnetism | Optimizes magnetic properties (permeability) through annealing. | Transformers, motors, magnetic devices. |
Microstructure | Controls grain size, phase transformations, and dislocation density. | Tailored material properties for specific applications. |
Cooling Rate | Faster cooling increases hardness; slower cooling enhances ductility and toughness. | Customized heat treatment for desired performance. |
Need help optimizing your metal properties? Contact our experts today to find the perfect heat treatment solution!