Heating elements are critical components in various applications, from household appliances to industrial furnaces. The choice of material for a heating element depends on several factors, including the required temperature, resistance to oxidation, cost, and specific application needs. Common materials include nickel-chromium alloys, iron-chromium-aluminum alloys, molybdenum, tungsten, and non-metallic materials like graphite and silicon carbide. These materials are selected based on their high resistivity, high melting points, low temperature coefficients, and resistance to oxidation. For low to medium temperatures, nickel-chromium alloys are ideal, while high-temperature applications may require exotic materials like tungsten disilicide or molybdenum disilicide.
Key Points Explained:
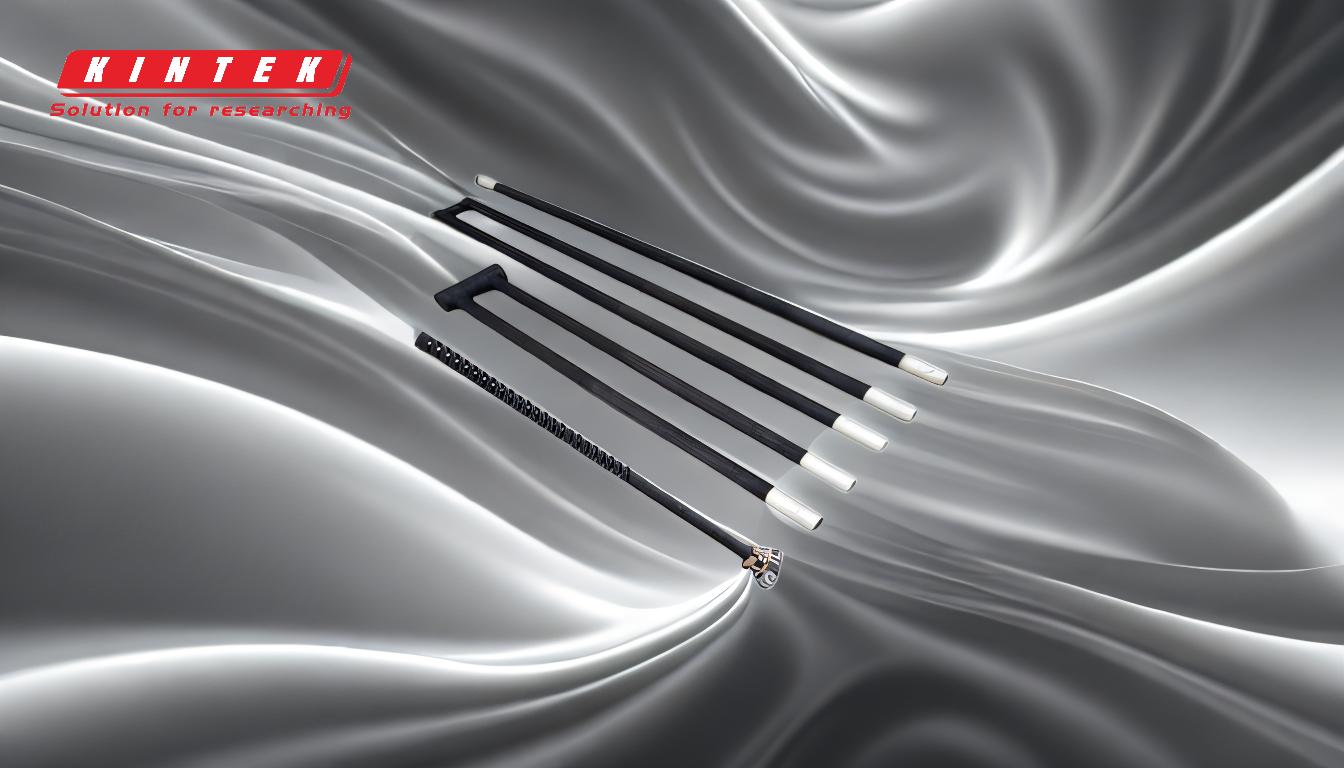
-
High Resistivity:
- Explanation: High resistivity is crucial for heating elements because it allows a small length of wire to produce significant heat. This property ensures that the element can efficiently convert electrical energy into thermal energy.
- Materials: Nickel-chromium alloys (80% nickel and 20% chromium) are commonly used due to their high resistivity.
-
High Melting Point:
- Explanation: A high melting point is essential to withstand the high temperatures that heating elements are exposed to. This ensures the element does not melt or degrade during operation.
- Materials: Nickel-chromium alloys, molybdenum, tungsten, and tantalum are preferred for their high melting points.
-
Low Temperature Coefficient:
- Explanation: A low temperature coefficient means that the resistance of the material does not vary significantly with temperature changes. This ensures consistent performance and longevity of the heating element.
- Materials: Nickel-chromium alloys and iron-chromium-aluminum alloys exhibit low temperature coefficients.
-
Resistance to Oxidation:
- Explanation: Oxidation can degrade the heating element over time, especially at high temperatures. Materials that resist oxidation ensure longer service life and reduce the need for frequent replacements.
- Materials: Nickel-chromium alloys and iron-chromium-aluminum alloys are known for their oxidation resistance. The addition of iron in some alloys (e.g., 65% nickel, 15% chromium, and 20% iron) further enhances this property.
-
Cost Considerations:
- Explanation: The cost of materials is a significant factor, especially for large-scale industrial applications. Alloys that include iron are often more cost-effective while still providing good performance.
- Materials: Iron-chromium-aluminum alloys and nickel-chromium-iron alloys are more economical compared to pure nickel-chromium alloys.
-
Application-Specific Materials:
- Explanation: Different applications require different materials based on the operating temperature and environment. For example, high-temperature furnaces may need exotic materials that can withstand extreme conditions.
-
Materials:
- Low to Medium Temperatures: Nickel-chromium alloys (80% nickel and 20% chromium) or nickel-chromium-iron alloys (65% nickel, 15% chromium, and 20% iron).
- High Temperatures: Exotic materials like platinum, tungsten disilicide, molybdenum disilicide, molybdenum, and silicon carbide.
-
Form and Shape:
- Explanation: The form and shape of the heating element can vary depending on the application. Elements can be straight, coiled, or shaped into panels, and may be made from wire, ribbon, or strips.
- Materials: Metallic materials like molybdenum, tungsten, and nickel-chromium alloys are often shaped into cylindrical, semi-circular, or flat panels. Non-metallic materials like graphite and silicon carbide are available in lightweight curved forms.
-
Non-Metallic Options:
- Explanation: Non-metallic materials offer unique properties that can be advantageous in certain applications, such as high-temperature stability and resistance to chemical attack.
- Materials: Graphite, silicon carbide, and molybdenum dioxide are common non-metallic options.
By considering these key points, one can select the most appropriate material for a heating element based on the specific requirements of the application, ensuring optimal performance, durability, and cost-effectiveness.
Summary Table:
Key Factor | Description | Common Materials |
---|---|---|
High Resistivity | Allows efficient conversion of electrical energy into thermal energy. | Nickel-chromium alloys (80% nickel, 20% chromium) |
High Melting Point | Ensures the element withstands high temperatures without melting or degrading. | Nickel-chromium alloys, molybdenum, tungsten, tantalum |
Low Temperature Coefficient | Maintains consistent resistance despite temperature changes. | Nickel-chromium alloys, iron-chromium-aluminum alloys |
Resistance to Oxidation | Prevents degradation and extends service life. | Nickel-chromium alloys, iron-chromium-aluminum alloys |
Cost Considerations | Balances performance with affordability for large-scale applications. | Iron-chromium-aluminum alloys, nickel-chromium-iron alloys |
Application-Specific | Tailored materials for specific temperature and environmental needs. | Low/Medium: Nickel-chromium alloys; High: Platinum, tungsten disilicide, silicon carbide |
Form and Shape | Varies based on application (e.g., wire, ribbon, panels). | Metallic: Molybdenum, tungsten; Non-metallic: Graphite, silicon carbide |
Non-Metallic Options | Offers high-temperature stability and chemical resistance. | Graphite, silicon carbide, molybdenum dioxide |
Need help selecting the right heating element material for your application? Contact our experts today!