Brazing copper involves joining copper components using a filler metal that melts at a temperature above 840°F (450°C) but below the melting point of the base metal. The optimal temperature range for brazing copper typically falls between 1,100°F and 1,500°F (593°C to 816°C), depending on the specific brazing alloy and application. This temperature range ensures that the filler metal flows properly, creating a strong and durable joint without damaging the copper base material.
Key Points Explained:
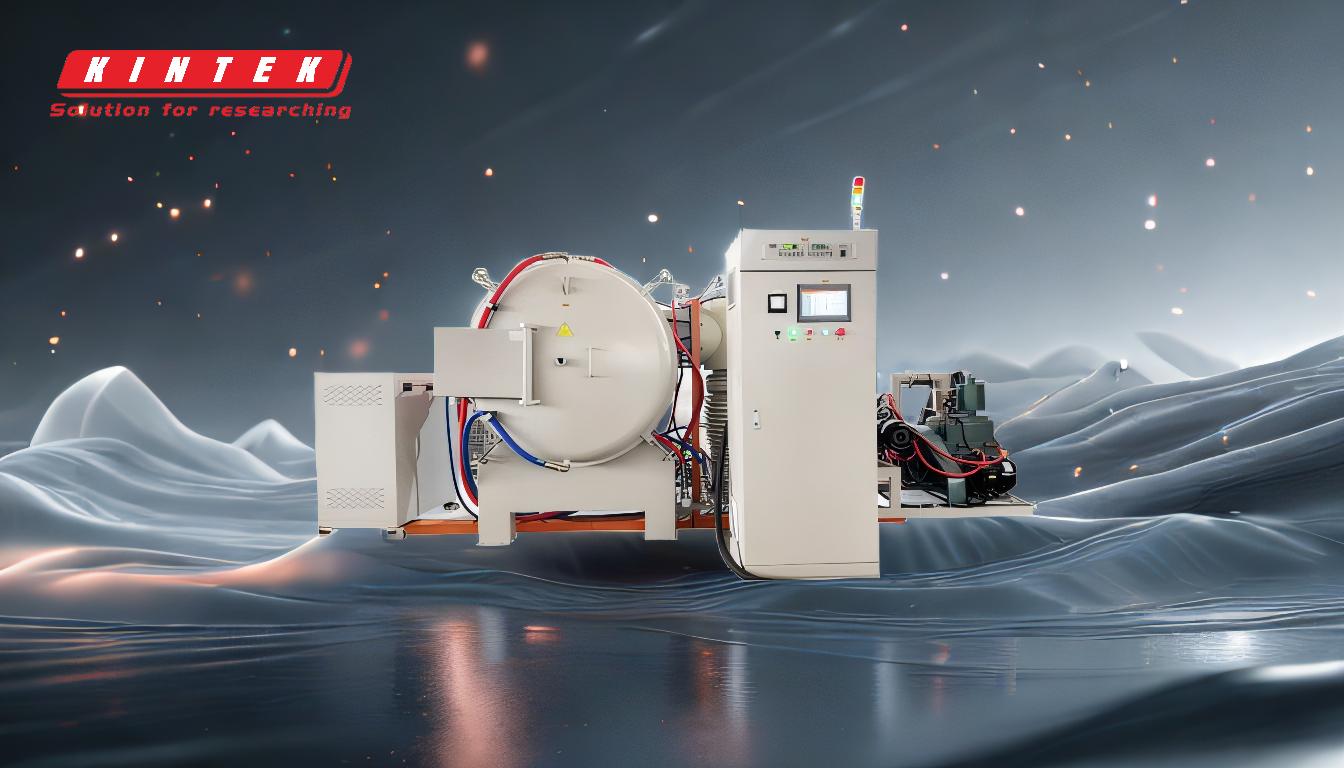
-
Temperature Range for Brazing Copper:
- The ideal temperature for brazing copper is between 1,100°F and 1,500°F (593°C to 816°C). This range ensures that the filler metal melts and flows adequately while the copper base material remains intact.
- The exact temperature within this range depends on the type of filler metal used and the specific requirements of the application.
-
Importance of Temperature Control:
- Maintaining the correct temperature is critical to avoid overheating, which can weaken the copper or cause the filler metal to vaporize.
- Underheating, on the other hand, can result in incomplete melting of the filler metal, leading to weak joints.
-
Brazing in a Hydrogen Atmosphere:
- Brazing in a hydrogen atmosphere is often preferred for copper because hydrogen acts as a reducing agent, preventing oxidation and ensuring a clean, strong joint.
- The temperature range of 1,100°F to 1,500°F is particularly effective in a hydrogen atmosphere, as it promotes proper wetting and flow of the filler metal.
-
Filler Metals for Copper Brazing:
- Common filler metals for brazing copper include silver-based alloys (e.g., BAg series) and copper-phosphorus alloys (e.g., BCuP series).
- Each filler metal has its own melting range, which must align with the brazing temperature to achieve optimal results.
-
Applications of Copper Brazing:
- Copper brazing is widely used in industries such as HVAC, plumbing, and electrical systems, where strong, leak-proof joints are essential.
- The temperature range ensures that the brazed joints can withstand thermal and mechanical stresses in these applications.
By adhering to the recommended temperature range and using appropriate filler metals, brazing copper can produce high-quality, reliable joints suitable for a variety of industrial and commercial uses.
Summary Table:
Key Aspect | Details |
---|---|
Optimal Temperature Range | 1,100°F to 1,500°F (593°C to 816°C) |
Importance of Control | Avoid overheating or underheating for strong, durable joints. |
Hydrogen Atmosphere | Prevents oxidation, ensures clean joints at 1,100°F to 1,500°F. |
Filler Metals | Silver-based (BAg) or copper-phosphorus (BCuP) alloys. |
Applications | HVAC, plumbing, electrical systems—ideal for leak-proof, stress-resistant joints. |
Need expert advice on brazing copper? Contact us today to ensure flawless results!