Sintering is a versatile process used across various industries for different purposes. It is most commonly associated with preparing iron ore fines for blast furnace use in steel production, where it agglomerates fine particles into lumps suitable for high-temperature processing. Additionally, sintering is widely used in powder metallurgy to create custom metal parts, especially for metals with high melting points, as it operates at relatively lower temperatures compared to melting. It also plays a significant role in 3D printing, enabling the layer-by-layer formation of complex metal shapes. Beyond metals, sintering is applied in ceramics, glass manufacturing, and even in creating sintered plastic and PE filters, showcasing its broad utility in improving material properties and reducing porosity.
Key Points Explained:
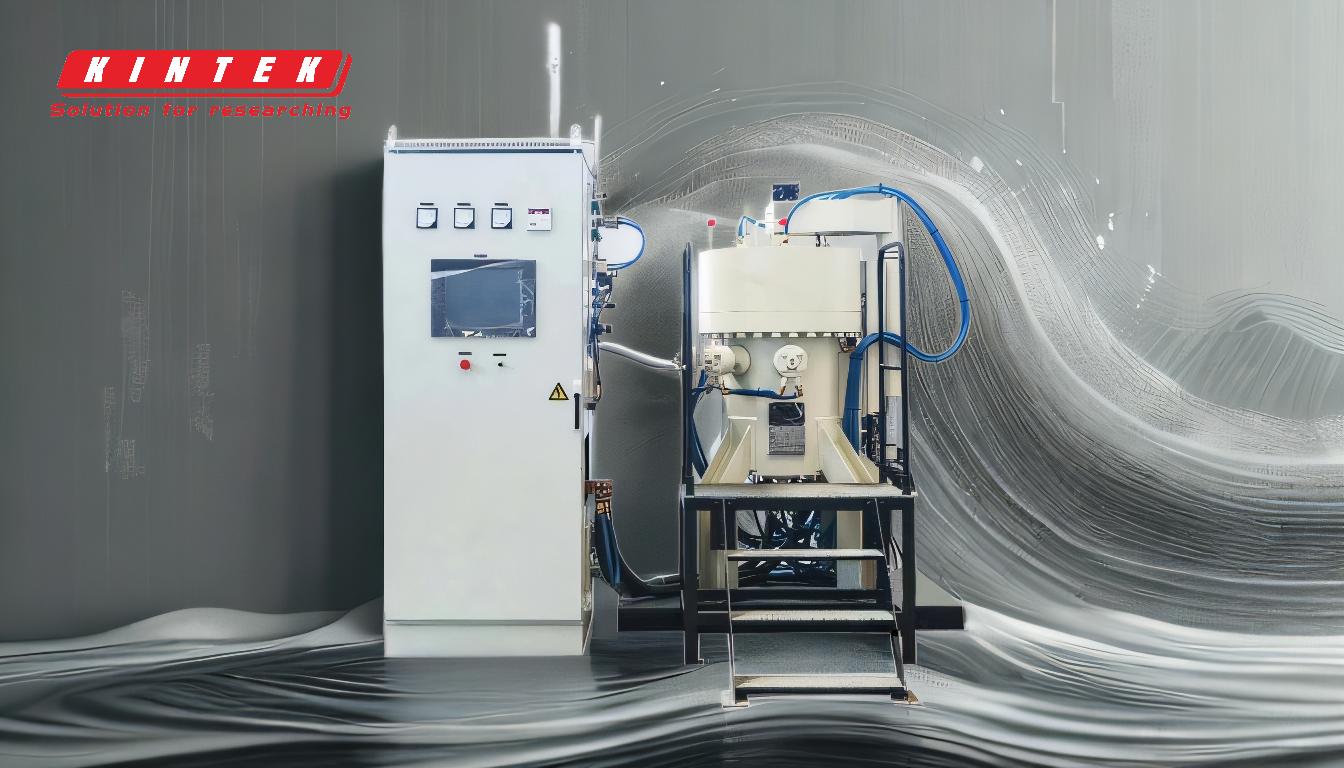
-
Iron Ore Preparation for Blast Furnaces:
- Sintering is a critical step in the steel manufacturing process, where iron ore fines are agglomerated into lumps.
- The process involves mixing powdered iron ore with coke, igniting it, and drawing air through a traveling grate to initiate combustion.
- This generates high heat, causing fine particles to form larger lumps, which are then charged into blast furnaces for hot metal production.
- This method is economical and widely used due to its efficiency in preparing raw materials for steelmaking.
-
Powder Metallurgy and Custom Metal Parts:
- Sintering is extensively used in powder metallurgy to create metal parts, particularly for metals with high melting points.
- The process involves compacting metal powders and heating them below their melting point to bond the particles.
- This is advantageous for producing complex shapes and custom parts, as it avoids the energy-intensive melting process.
- Common applications include automotive components, aerospace parts, and industrial machinery.
-
3D Printing and Additive Manufacturing:
- Sintering is integral to 3D printing, especially in metal additive manufacturing.
- It allows for the layer-by-layer creation of custom metal shapes, offering design flexibility and energy efficiency.
- Unlike traditional melting, sintering operates at lower temperatures, making it suitable for materials that are difficult to melt.
- This technique is widely used in industries requiring precision parts, such as medical devices and robotics.
-
Ceramics and Glass Manufacturing:
- Sintering is traditionally used in the production of ceramic objects and glass.
- It helps reduce porosity and improve the mechanical properties of these materials.
- By heating ceramic or glass powders below their melting points, sintering bonds particles to form durable and dense products.
- Applications include household ceramics, industrial ceramics, and specialized glass products.
-
Sintered Filters and Plastics:
- Sintering is employed to create sintered plastic and polyethylene (PE) filters.
- These filters are characterized by their controlled porosity, which is achieved through the sintering process.
- They are used in various industries, including water purification, chemical processing, and air filtration.
- Sintered plastics are also used in applications requiring lightweight, durable, and porous materials.
-
Surface Property Enhancement:
- Sintering can improve the surface properties of materials by reducing porosity and increasing density.
- This is particularly useful in applications requiring wear resistance, thermal conductivity, or mechanical strength.
- For example, sintered metal parts often exhibit enhanced durability and performance compared to their non-sintered counterparts.
-
Energy Efficiency and Environmental Benefits:
- Sintering is generally more energy-efficient than melting, as it operates at lower temperatures.
- This makes it an environmentally friendly option for material processing, reducing energy consumption and greenhouse gas emissions.
- Its application in recycling metal powders and waste materials further contributes to sustainability efforts in manufacturing.
By understanding these key points, it becomes clear that sintering is a foundational process in modern manufacturing, offering versatility, efficiency, and improved material properties across a wide range of industries.
Summary Table:
Application | Key Benefits |
---|---|
Iron Ore Preparation | Agglomerates fine particles for blast furnace use; economical and efficient. |
Powder Metallurgy | Creates custom metal parts; avoids energy-intensive melting. |
3D Printing | Enables layer-by-layer formation of complex metal shapes; energy-efficient. |
Ceramics & Glass Manufacturing | Reduces porosity; improves mechanical properties. |
Sintered Filters & Plastics | Produces lightweight, durable, and porous materials for filtration. |
Surface Property Enhancement | Improves wear resistance, thermal conductivity, and mechanical strength. |
Energy Efficiency | Operates at lower temperatures; reduces energy consumption and emissions. |
Discover how sintering can transform your manufacturing processes—contact our experts today!