Heat treatment is a process used to alter the physical and sometimes chemical properties of materials, typically metals, to improve their performance. The chemicals used in heat treatment vary depending on the specific process and desired outcome. Common chemicals include quenching media like water, oil, and polymers, as well as gases such as nitrogen, argon, and carbon dioxide for controlled atmospheres. Additionally, salts like sodium chloride and potassium chloride are used in salt baths for precise temperature control. Each chemical serves a specific purpose, such as cooling, preventing oxidation, or facilitating diffusion processes.
Key Points Explained:
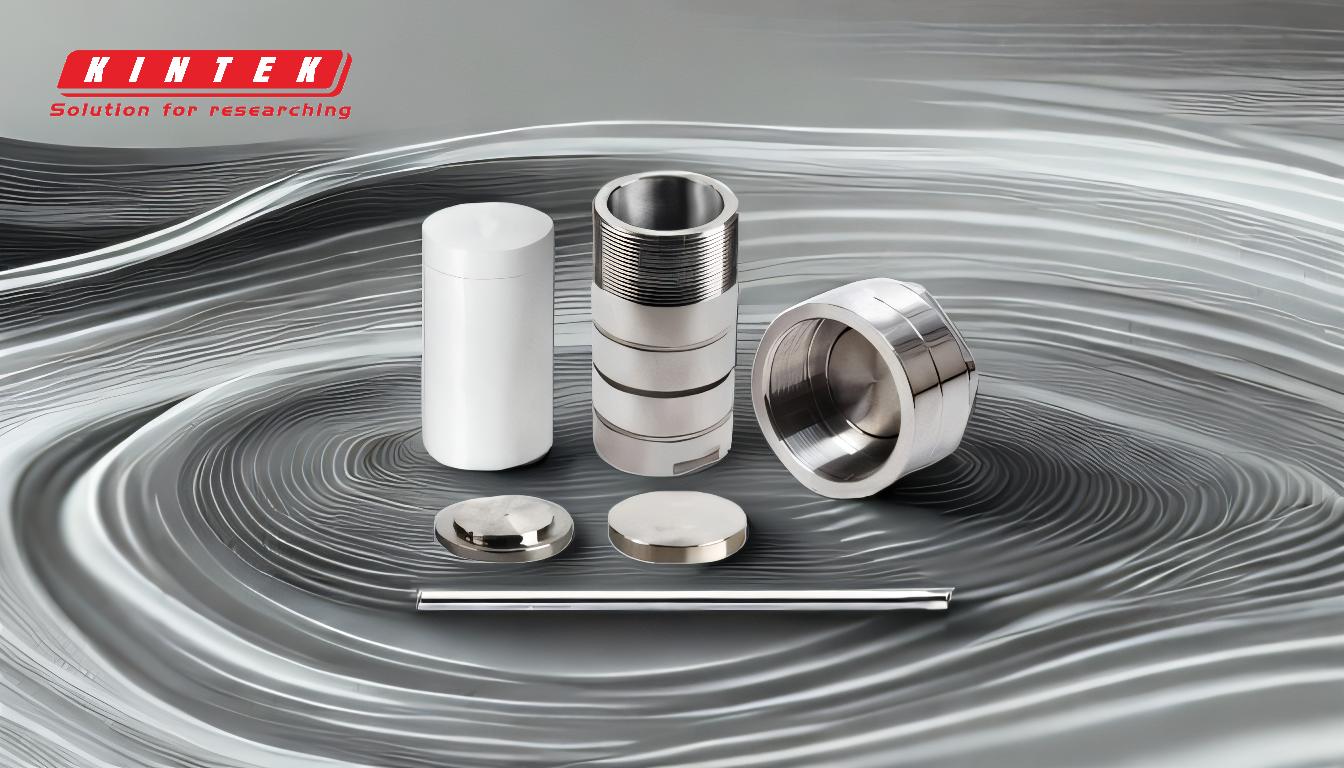
-
Purpose of Heat Treatment Chemicals:
- Heat treatment chemicals are used to modify the microstructure of metals, enhancing properties like hardness, strength, and ductility. The choice of chemical depends on the specific heat treatment process, such as annealing, quenching, or carburizing.
-
Common Chemicals Used in Heat Treatment:
-
Quenching Media:
- Water: Used for rapid cooling, especially in processes like hardening. It is inexpensive but can cause distortion or cracking in some metals.
- Oil: Provides slower cooling rates than water, reducing the risk of cracking. It is commonly used for alloy steels.
- Polymers: Offer adjustable cooling rates and are environmentally friendly compared to oil. They are used in various quenching applications.
-
Gases:
- Nitrogen: Used in controlled atmosphere furnaces to prevent oxidation and decarburization.
- Argon: An inert gas used to create a protective atmosphere, especially for reactive metals.
- Carbon Dioxide: Sometimes used in carburizing processes to introduce carbon into the metal surface.
-
Salts:
- Sodium Chloride and Potassium Chloride: Used in salt baths for precise temperature control and uniform heating. They are often used in processes like austempering and martempering.
-
Quenching Media:
-
Role of Chemicals in Specific Heat Treatment Processes:
- Annealing: Involves heating and slow cooling to soften the metal. Controlled atmospheres with nitrogen or argon are often used to prevent oxidation.
- Quenching: Rapid cooling to achieve high hardness. The choice of quenching medium (water, oil, or polymer) depends on the material and desired properties.
- Carburizing: Introduces carbon into the surface of low-carbon steels. Gases like carbon dioxide or hydrocarbon gases are used in this process.
- Nitriding: Introduces nitrogen into the surface of the metal to improve hardness and wear resistance. Ammonia is commonly used in this process.
-
Considerations for Selecting Heat Treatment Chemicals:
- Material Type: Different metals and alloys require specific chemicals for optimal results.
- Desired Properties: The choice of chemical depends on whether the goal is to increase hardness, toughness, or corrosion resistance.
- Environmental and Safety Concerns: Some chemicals, like oil and certain gases, may pose environmental or safety risks, so alternatives like polymers or inert gases may be preferred.
-
Advantages and Disadvantages of Common Chemicals:
-
Water:
- Advantages: Inexpensive and effective for rapid cooling.
- Disadvantages: Can cause distortion or cracking in some metals.
-
Oil:
- Advantages: Slower cooling rates reduce the risk of cracking.
- Disadvantages: Can be messy and pose environmental hazards.
-
Polymers:
- Advantages: Adjustable cooling rates and environmentally friendly.
- Disadvantages: May require more precise control and monitoring.
-
Gases (Nitrogen, Argon):
- Advantages: Prevent oxidation and decarburization.
- Disadvantages: Can be expensive and require specialized equipment.
-
Water:
-
Future Trends in Heat Treatment Chemicals:
- There is a growing trend towards using more environmentally friendly chemicals, such as biodegradable polymers and non-toxic gases. Additionally, advancements in controlled atmosphere technologies are improving the precision and efficiency of heat treatment processes.
In conclusion, the choice of chemical in heat treatment depends on the specific process, material, and desired outcome. Understanding the properties and applications of each chemical is crucial for achieving the desired results while minimizing risks and environmental impact.
Summary Table:
Category | Chemicals | Purpose |
---|---|---|
Quenching Media | Water, Oil, Polymers | Rapid or controlled cooling to achieve desired hardness and reduce cracking |
Gases | Nitrogen, Argon, Carbon Dioxide | Prevent oxidation, decarburization, and create protective atmospheres |
Salts | Sodium Chloride, Potassium Chloride | Precise temperature control in salt baths for uniform heating |
Need help selecting the right heat treatment chemicals for your application? Contact our experts today for tailored solutions!