The failure of furnace linings is primarily caused by thermal expansion and spalling, which occur due to the differential rates of expansion and contraction of refractory materials under varying thermal conditions. This phenomenon leads to cracking and spalling, which, if left unaddressed, can result in the structural failure of the furnace lining. Understanding the mechanisms behind these failures is crucial for selecting appropriate materials and implementing maintenance strategies to prolong the lifespan of furnace linings.
Key Points Explained:
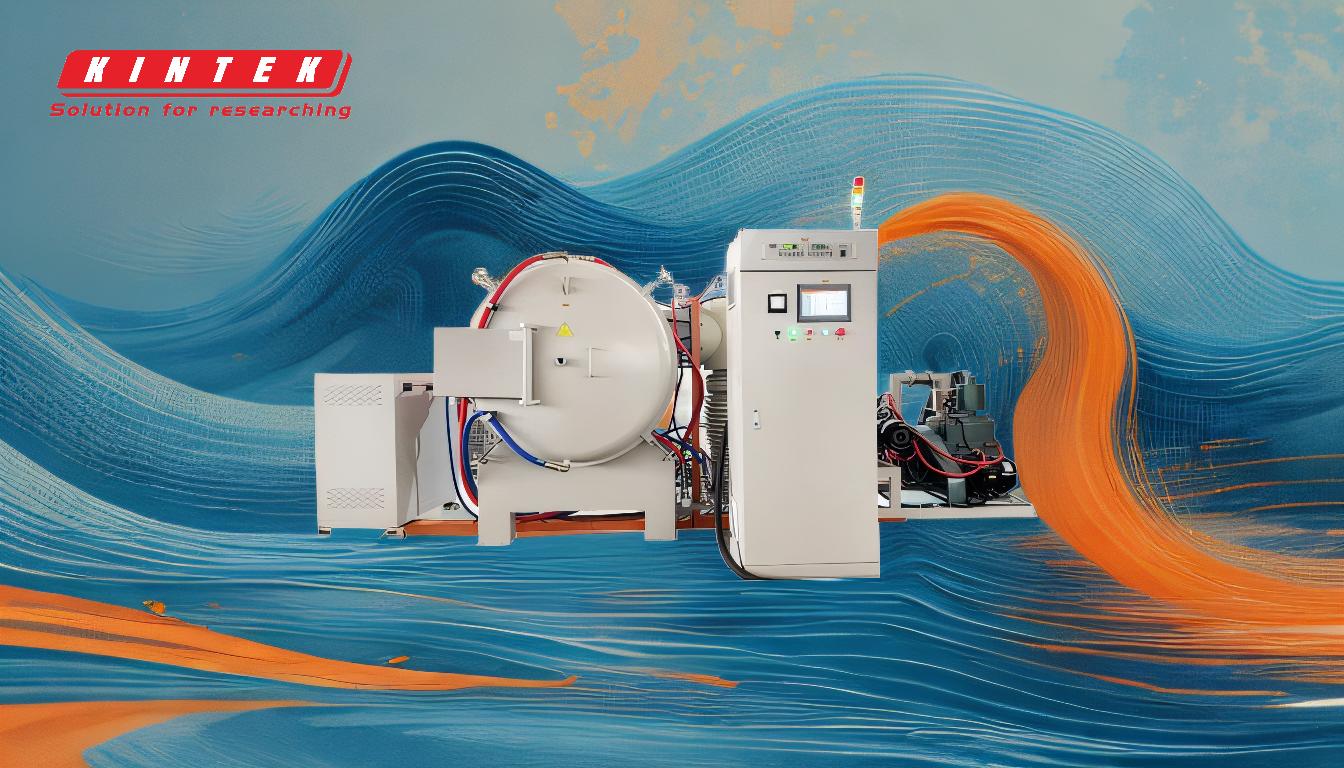
-
Thermal Expansion and Contraction:
- Mechanism: Refractory materials expand when heated and contract when cooled. Different materials have varying coefficients of thermal expansion, meaning they expand and contract at different rates.
- Impact: When the furnace undergoes thermal cycling (heating and cooling), the differential expansion and contraction rates can cause stress within the lining. This stress can lead to the formation of cracks over time.
-
Spalling:
- Definition: Spalling refers to the breaking off of fragments or layers from the surface of the refractory lining.
- Causes: Spalling is often a direct result of the stresses caused by thermal expansion and contraction. It can also be exacerbated by mechanical wear, chemical attack, or improper installation of the refractory materials.
- Consequences: Spalling exposes the underlying layers of the refractory lining to higher temperatures and more severe thermal and chemical conditions, accelerating further degradation and potentially leading to catastrophic failure.
-
Cracking:
- Formation: Cracks can form due to the repeated thermal cycling of the furnace. These cracks can start as micro-cracks and grow larger over time.
- Implications: Cracks provide pathways for heat and corrosive gases to penetrate deeper into the refractory lining, leading to further deterioration. They also weaken the structural integrity of the lining, making it more susceptible to mechanical failure.
-
Preventive Measures:
- Material Selection: Choosing refractory materials with compatible thermal expansion coefficients can minimize the stress caused by thermal cycling.
- Design Considerations: Proper design of the furnace lining, including the use of expansion joints and appropriate thicknesses, can help accommodate thermal expansion and contraction.
- Maintenance: Regular inspection and timely repair of cracks and spalled areas can prevent minor issues from developing into major failures.
-
Repair and Maintenance:
- Importance: Early detection and repair of cracks and spalled areas are crucial to maintaining the integrity of the furnace lining.
- Techniques: Techniques such as patching, gunning, and applying protective coatings can be used to repair damaged areas and extend the life of the lining.
In summary, the failure of furnace linings is predominantly caused by thermal expansion and spalling, which lead to cracking and structural degradation. Understanding these mechanisms and implementing appropriate preventive and maintenance measures are essential for ensuring the longevity and reliability of furnace linings.
Summary Table:
Key Factor | Description | Impact |
---|---|---|
Thermal Expansion | Refractory materials expand and contract at different rates under thermal cycling. | Causes stress, leading to cracks and weakening the lining structure. |
Spalling | Fragments break off due to stress, wear, or chemical attack. | Exposes underlying layers, accelerating degradation and risking catastrophic failure. |
Cracking | Repeated thermal cycling causes micro-cracks to grow larger. | Allows heat and corrosive gases to penetrate, further deteriorating the lining. |
Preventive Measures | Proper material selection, design, and maintenance strategies. | Minimizes stress, accommodates thermal changes, and prevents minor issues from escalating. |
Repair Techniques | Patching, gunning, and protective coatings. | Extends the lifespan of the lining by repairing damaged areas. |
Protect your furnace lining from failure—contact our experts for tailored solutions and maintenance strategies!