The efficiency of a furnace depends on several factors, including its type, fuel source, and operational conditions. Generally, electric furnaces are more thermally efficient, but gas furnaces tend to be more cost-effective and efficient in most climates. For pyrolysis furnaces, efficiency is influenced by temperature, residence time, and pressure control. Proper maintenance and operation are critical for maximizing efficiency. Below, we explore the key factors that determine furnace efficiency and provide a detailed comparison of electric and gas furnaces.
Key Points Explained:
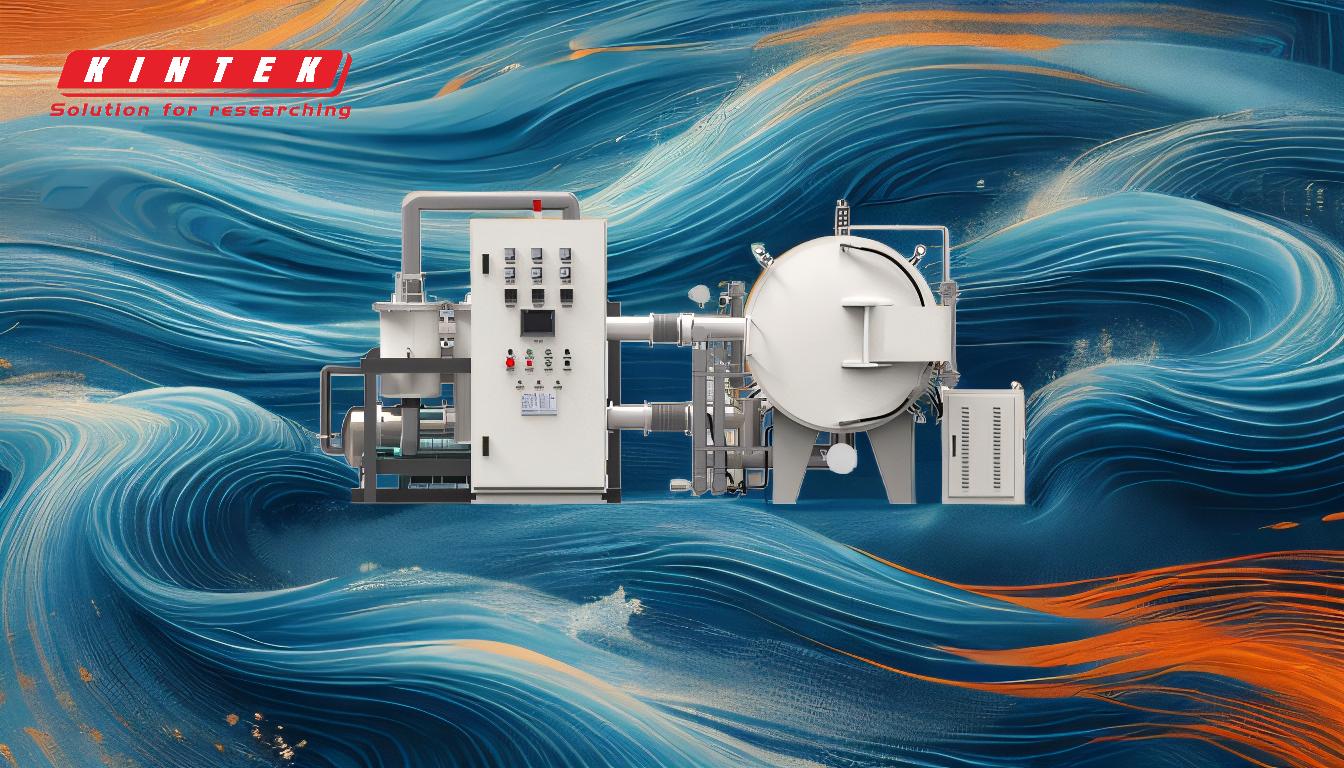
-
Thermal Efficiency of Electric vs. Gas Furnaces
- Electric Furnaces: These furnaces convert nearly 100% of the electricity they consume into heat, making them highly thermally efficient. However, electricity is often more expensive than natural gas, which can offset their efficiency advantages.
- Gas Furnaces: While gas furnaces typically have lower thermal efficiency (around 80-98%), they are often more cost-effective due to the lower price of natural gas. In colder climates, gas furnaces are generally more efficient overall because they can produce heat more quickly and at a lower cost.
-
Factors Affecting Pyrolysis Furnace Efficiency
- Temperature: The furnace temperature must be carefully controlled to ensure optimal thermal decomposition of materials. Too high or too low temperatures can reduce efficiency.
- Residence Time: The amount of time materials spend in the furnace affects the completeness of the pyrolysis process. Proper residence time ensures maximum energy extraction.
- Pressure: Maintaining the correct pressure inside the furnace is crucial for efficient operation and safety.
- Maintenance: Regular maintenance ensures that the furnace operates at peak efficiency and reduces the risk of breakdowns.
-
Operational Considerations
- Climate: In colder climates, gas furnaces are often more efficient because they can generate heat more quickly and cost-effectively. Electric furnaces may struggle to meet heating demands in extreme cold.
- Fuel Availability and Cost: The availability and cost of fuel (electricity, natural gas, or oil) play a significant role in determining the overall efficiency of a furnace.
- Furnace Type: Single-stage, two-stage, and modulating furnaces offer varying levels of efficiency and control. Modulating furnaces, for example, adjust their output to match heating needs, improving efficiency.
-
Energy Efficiency Ratings
- AFUE (Annual Fuel Utilization Efficiency): This rating measures how efficiently a furnace converts fuel into heat over a year. Gas furnaces with high AFUE ratings (90% or above) are highly efficient.
- HSPF (Heating Seasonal Performance Factor): For heat pumps and electric furnaces, HSPF measures efficiency over a heating season. Higher HSPF values indicate better efficiency.
-
Cost of Operation
- While electric furnaces have higher thermal efficiency, the cost of electricity often makes them more expensive to operate than gas furnaces. Gas furnaces, despite lower thermal efficiency, are generally more economical due to the lower cost of natural gas.
-
Environmental Impact
- Electric furnaces produce no direct emissions, making them environmentally friendly if the electricity comes from renewable sources.
- Gas furnaces emit carbon dioxide and other pollutants, but modern high-efficiency models significantly reduce emissions compared to older units.
In summary, the most efficient furnace depends on your specific needs, climate, and fuel availability. Electric furnaces excel in thermal efficiency but may be costly to operate, while gas furnaces are often more economical and effective in colder climates. For pyrolysis furnaces, precise control of temperature, residence time, and pressure is essential for optimal efficiency. Always consider long-term operational costs and environmental impact when choosing a furnace.
Summary Table:
Factor | Electric Furnaces | Gas Furnaces | Pyrolysis Furnaces |
---|---|---|---|
Thermal Efficiency | Nearly 100% | 80-98% | Depends on temperature, residence time |
Cost of Operation | Higher due to electricity costs | Lower due to natural gas affordability | Requires precise control and maintenance |
Climate Suitability | Less efficient in extreme cold | More efficient in colder climates | N/A |
Environmental Impact | No direct emissions (if renewable energy used) | Emits CO2 (modern models reduce emissions) | N/A |
Key Considerations | High thermal efficiency, higher operating cost | Cost-effective, better for cold climates | Temperature, residence time, pressure |
Need help choosing the right furnace for your needs? Contact our experts today for personalized advice!