The "best" heat treatment method depends entirely on the desired outcome for the material, such as hardness, ductility, machinability, or stress relief. Annealing is ideal for softening metals, improving machinability, and relieving internal stresses. Quenching is used to rapidly cool metals, increasing hardness but often making them brittle. Tempering reduces brittleness post-quenching while maintaining hardness. Normalizing refines grain structure and improves mechanical properties. Case hardening enhances surface hardness while keeping the core ductile. Each method serves specific purposes, and the choice depends on the material's intended application and required properties.
Key Points Explained:
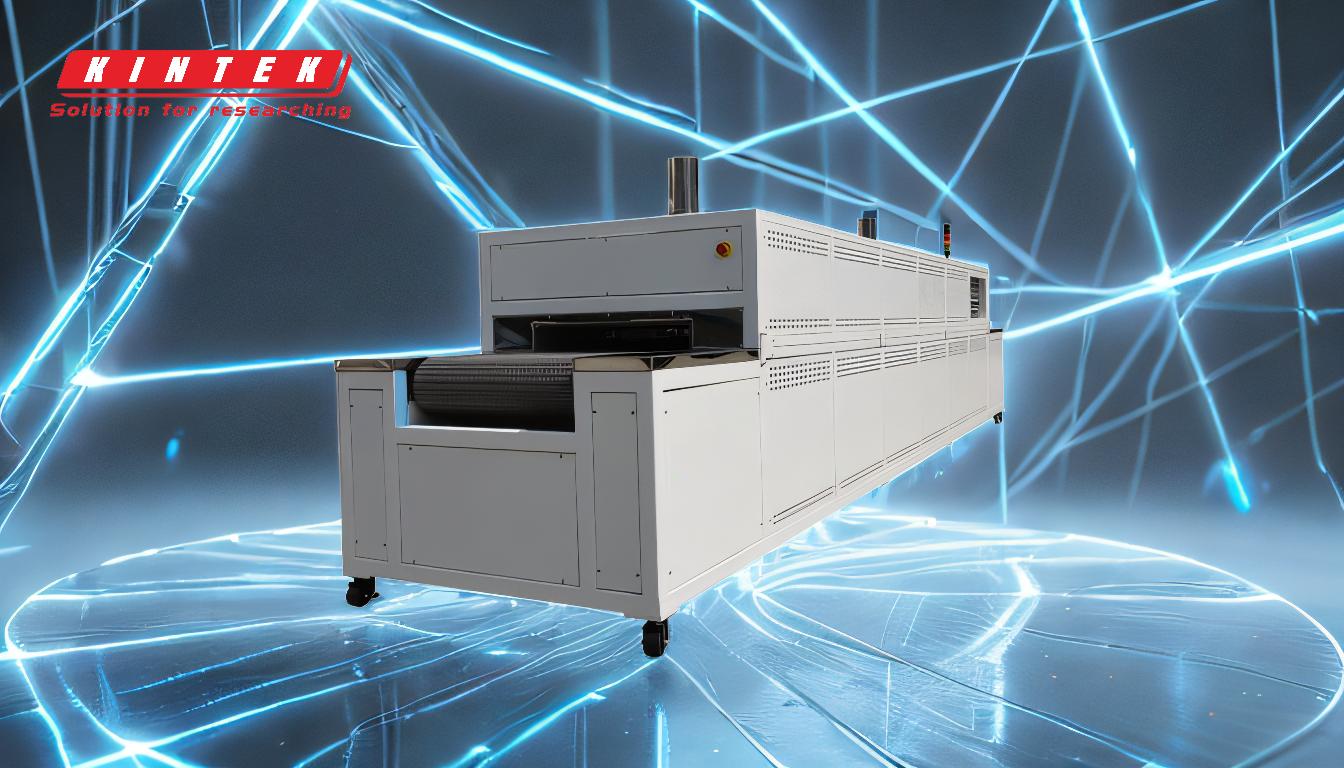
-
Annealing:
- Purpose: Softens metals, improves machinability, and relieves internal stresses.
- Process: Metals are heated and then gradually cooled.
- Result: Uniform and softer structure, ideal for materials that need to be worked further.
- Applications: Used in manufacturing processes where ductility and reduced hardness are required.
-
Quenching:
- Purpose: Increases hardness and strength.
- Process: Rapid cooling of heated metals, often in water, oil, or air.
- Result: Hard but brittle material.
- Applications: Suitable for tools and components requiring high surface hardness.
-
Tempering:
- Purpose: Reduces brittleness while maintaining hardness.
- Process: Heating quenched metals to a lower temperature and then cooling.
- Result: Improved toughness and ductility.
- Applications: Used in tools and structural components to balance hardness and durability.
-
Normalizing:
- Purpose: Refines grain structure and improves mechanical properties.
- Process: Heating metals to a high temperature and then cooling in air.
- Result: Uniform grain structure and enhanced strength.
- Applications: Common in steel manufacturing to prepare materials for further processing.
-
Case Hardening:
- Purpose: Increases surface hardness while maintaining a ductile core.
- Process: Adding carbon or nitrogen to the surface layer of the metal.
- Result: Hard exterior with a tough interior.
- Applications: Ideal for gears, shafts, and other components requiring wear resistance.
-
Martensitic Transformation:
- Purpose: Achieves high hardness and strength.
- Process: Rapid cooling to form martensite, a hard microstructure.
- Result: Extremely hard but brittle material.
- Applications: Used in high-strength applications like knives and cutting tools.
-
Carburizing:
- Purpose: Increases surface hardness by adding carbon.
- Process: Heating metals in a carbon-rich environment.
- Result: Hardened surface with a softer core.
- Applications: Suitable for components requiring wear resistance.
-
Stress Relieving:
- Purpose: Reduces residual stresses in metals.
- Process: Heating metals to a moderate temperature and then cooling slowly.
- Result: Improved dimensional stability and reduced risk of cracking.
- Applications: Used in welded or machined parts to prevent deformation.
-
Bright Annealing:
- Purpose: Minimizes oxidation during annealing.
- Process: Heating metals in a protective atmosphere (hydrogen, nitrogen, or argon).
- Result: Clean, oxidation-free surface.
- Applications: Used in stainless steel and other materials requiring a pristine finish.
-
Sintering:
- Purpose: Bonds metal powders into a solid structure.
- Process: Heating metals to just below their melting point in a protective atmosphere.
- Result: Dense, strong components.
- Applications: Common in powder metallurgy for creating complex shapes.
In conclusion, the "best" heat treatment method depends on the specific requirements of the material and its intended use. For example, annealing is best for softening and stress relief, while quenching and tempering are ideal for achieving high hardness and toughness. Understanding the properties and processes of each method is crucial for selecting the appropriate heat treatment for any given application.
Summary Table:
Method | Purpose | Process | Result | Applications |
---|---|---|---|---|
Annealing | Softens metals, improves machinability, relieves internal stresses | Metals are heated and gradually cooled | Uniform and softer structure | Manufacturing processes requiring ductility and reduced hardness |
Quenching | Increases hardness and strength | Rapid cooling of heated metals (water, oil, or air) | Hard but brittle material | Tools and components requiring high surface hardness |
Tempering | Reduces brittleness while maintaining hardness | Heating quenched metals to a lower temperature and cooling | Improved toughness and ductility | Tools and structural components balancing hardness and durability |
Normalizing | Refines grain structure, improves mechanical properties | Heating metals to a high temperature and cooling in air | Uniform grain structure and enhanced strength | Steel manufacturing for further processing preparation |
Case Hardening | Increases surface hardness while maintaining a ductile core | Adding carbon or nitrogen to the surface layer | Hard exterior with a tough interior | Gears, shafts, and components requiring wear resistance |
Martensitic Transformation | Achieves high hardness and strength | Rapid cooling to form martensite | Extremely hard but brittle material | High-strength applications like knives and cutting tools |
Carburizing | Increases surface hardness by adding carbon | Heating metals in a carbon-rich environment | Hardened surface with a softer core | Components requiring wear resistance |
Stress Relieving | Reduces residual stresses in metals | Heating metals to a moderate temperature and cooling slowly | Improved dimensional stability and reduced risk of cracking | Welded or machined parts to prevent deformation |
Bright Annealing | Minimizes oxidation during annealing | Heating metals in a protective atmosphere (hydrogen, nitrogen, or argon) | Clean, oxidation-free surface | Stainless steel and materials requiring a pristine finish |
Sintering | Bonds metal powders into a solid structure | Heating metals just below their melting point in a protective atmosphere | Dense, strong components | Powder metallurgy for creating complex shapes |
Need help choosing the right heat treatment method for your materials? Contact our experts today for tailored solutions!