The choice between LPCVD (Low-Pressure Chemical Vapor Deposition) and PECVD (Plasma-Enhanced Chemical Vapor Deposition) depends on the specific application, material requirements, and process constraints. LPCVD is generally favored for its high-quality films, excellent step coverage, and ability to operate at higher temperatures, making it ideal for high-value semiconductor applications. PECVD, on the other hand, offers lower-temperature processing, higher deposition rates, and greater flexibility, making it suitable for applications requiring lower thermal budgets, such as CMOS manufacturing. Both methods have distinct advantages and limitations, and the decision should be based on the desired film properties, substrate compatibility, and process conditions.
Key Points Explained:
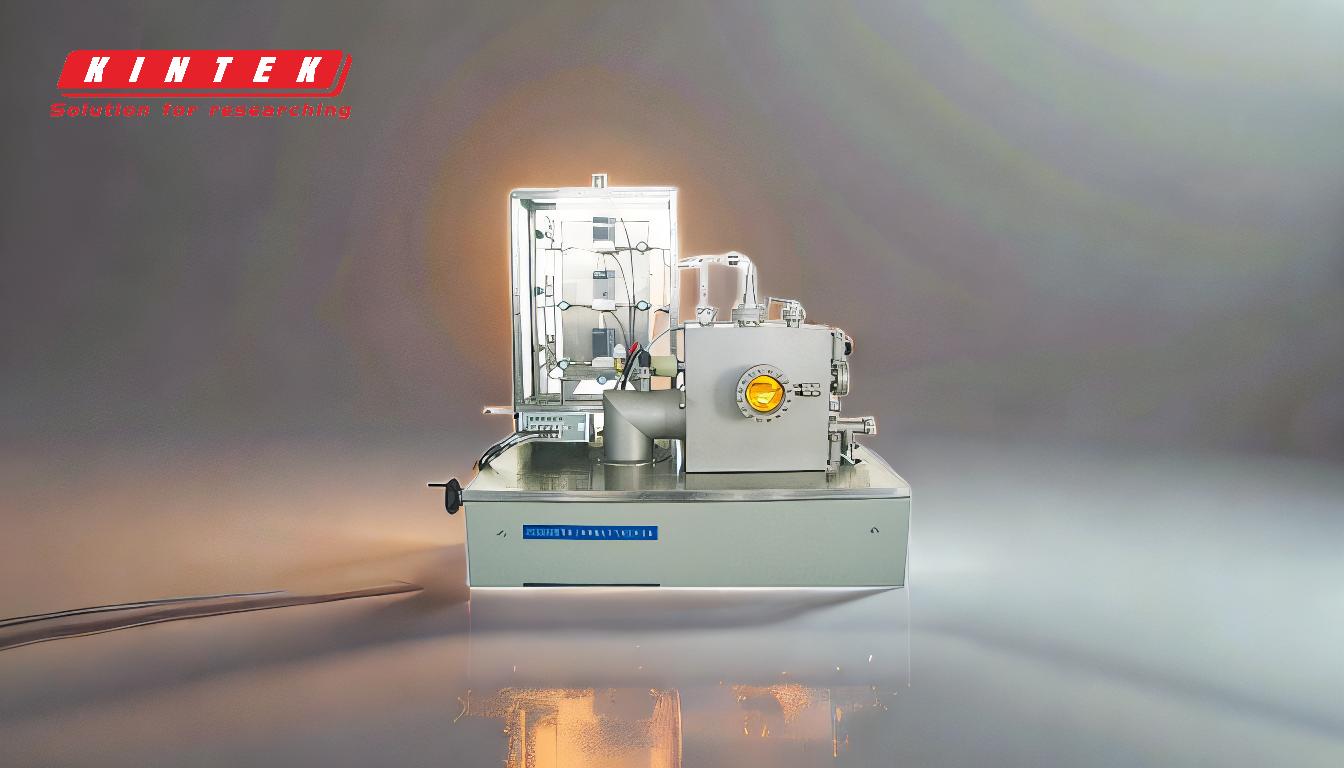
-
Film Quality and Properties:
- LPCVD: Produces high-quality films with excellent conformal step coverage, good composition control, and low hydrogen content. These properties make LPCVD ideal for applications requiring precise film characteristics, such as in the semiconductor industry.
- PECVD: Films tend to have higher hydrogen content, higher etch rates, and potential pinholes, especially in thinner films. However, PECVD can still produce high-quality dielectrics for specific applications like CMOS manufacturing.
-
Temperature Requirements:
- LPCVD: Operates at higher temperatures, which can limit its use with temperature-sensitive substrates. However, the higher temperatures contribute to better film quality and lower hydrogen content.
- PECVD: Operates at lower temperatures (below 300°C), making it suitable for temperature-sensitive materials and later stages of integrated circuit manufacturing.
-
Deposition Rate:
- LPCVD: Offers a high deposition rate, which is beneficial for high-throughput processes in the semiconductor industry.
- PECVD: Provides an even higher deposition rate compared to LPCVD, which can be advantageous for applications requiring rapid film deposition.
-
Step Coverage and Conformality:
- LPCVD: Known for its excellent step coverage and conformality, making it suitable for complex geometries and high-aspect-ratio structures.
- PECVD: Step coverage is generally inferior to LPCVD, which can be a limitation for certain applications requiring uniform film deposition over intricate features.
-
Substrate Compatibility:
- LPCVD: Does not require a silicon substrate and can deposit films on a variety of materials, offering greater versatility.
- PECVD: Typically uses a tungsten-based substrate and is more limited in terms of substrate compatibility compared to LPCVD.
-
Process Flexibility:
- LPCVD: Offers versatility in depositing a wide range of materials, making it suitable for diverse applications in the electronics industry.
- PECVD: Provides greater flexibility in terms of process conditions, such as lower temperatures and higher pressures, which can be tailored to specific application needs.
-
Hydrogen Content and Film Integrity:
- LPCVD: Films have lower hydrogen content, resulting in better film integrity and fewer defects.
- PECVD: Films tend to have higher hydrogen content, which can affect film properties and performance, particularly in thinner films.
-
Applications:
- LPCVD: Widely used in high-value-added semiconductor applications, such as thin film deposition for advanced electronic devices.
- PECVD: Commonly used in CMOS manufacturing and other applications requiring high-quality dielectrics at lower temperatures.
-
Cost and Complexity:
- LPCVD: Generally more expensive and complex due to the higher temperatures and precise control required.
- PECVD: Can be more cost-effective and simpler to implement, especially for applications requiring lower temperatures and higher deposition rates.
-
Environmental and Operational Considerations:
- LPCVD: Does not require carrier gas, reducing particle pollution and environmental impact.
- PECVD: Operates at higher pressures and temperatures, which can influence the environmental and operational aspects of the process.
In summary, the choice between LPCVD and PECVD should be guided by the specific requirements of the application, including film quality, temperature constraints, deposition rate, and substrate compatibility. LPCVD is generally preferred for high-quality, high-temperature applications, while PECVD offers advantages in lower-temperature, high-deposition-rate scenarios.
Summary Table:
Feature | LPCVD | PECVD |
---|---|---|
Film Quality | High-quality, low hydrogen content, excellent step coverage | Higher hydrogen content, potential pinholes, good for dielectrics |
Temperature | High-temperature processing (ideal for semiconductors) | Low-temperature processing (below 300°C, suitable for CMOS) |
Deposition Rate | High deposition rate | Even higher deposition rate |
Step Coverage | Excellent conformality for complex geometries | Inferior step coverage compared to LPCVD |
Substrate Compatibility | Versatile, works with various materials | Limited to tungsten-based substrates |
Applications | High-value semiconductor applications | CMOS manufacturing and low-temperature processes |
Cost and Complexity | More expensive and complex | Cost-effective and simpler to implement |
Need help deciding between LPCVD and PECVD? Contact our experts today for tailored advice!