The materials used in an induction furnace are carefully selected to ensure they can withstand high temperatures and provide efficient heat preservation. The primary materials include refractory materials like magnesia, dolomite, and alumina for the furnace lining, which offer high melting points and durability. The furnace body is often constructed using vacuum-formed high-purity alumina fiber materials, known for their excellent heat preservation and high-temperature resistance. Heating elements are typically made from iron-chrome aluminum or nickel chrome alloys, and sometimes graphite or molybdenum strips. Additionally, the furnace is designed to melt a variety of metals and alloys, including stainless steel, aluminum, and precious metals, as well as specialized alloys like nickel, cobalt, and iron-based superalloys.
Key Points Explained:
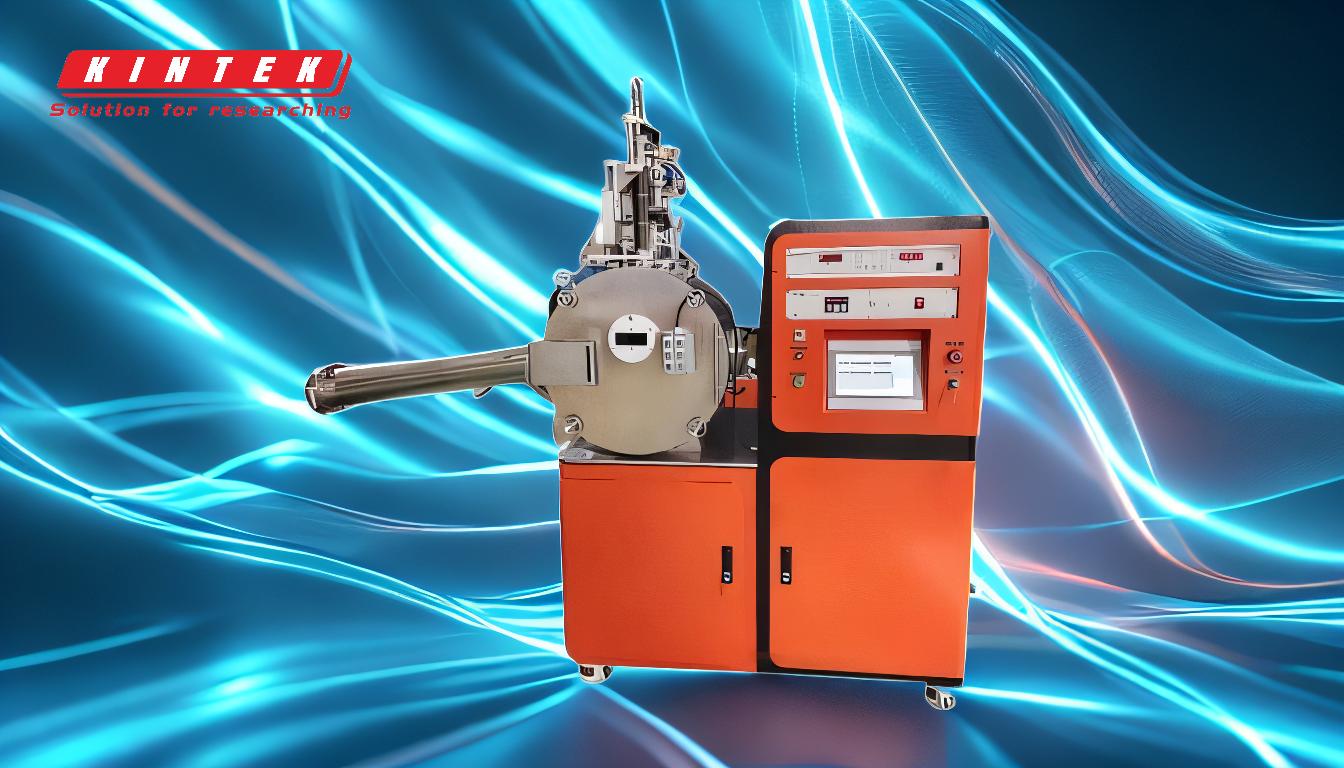
-
Refractory Materials for Furnace Lining:
- Magnesia, Dolomite, and Alumina: These materials are used for the furnace lining due to their high melting points and ability to withstand extreme temperatures. They ensure the furnace can operate efficiently without degrading over time.
- Purpose: The lining protects the furnace structure from the intense heat generated during melting processes and prevents contamination of the molten metal.
-
Furnace Construction Materials:
- Vacuum-Formed High-Purity Alumina Fiber: This material is used to construct the furnace body. It provides excellent heat preservation and can bear high temperatures, making it ideal for maintaining consistent heat levels during melting.
- Benefits: High-purity alumina fiber is lightweight, durable, and offers superior thermal insulation, which enhances energy efficiency.
-
Heating Elements:
- Iron-Chrome Aluminum or Nickel Chrome Alloys: These materials are commonly used for heating elements due to their high resistance to heat and wear. They are shaped into cylindrical, semi-circular, or flat panels to ensure even heat distribution.
- Graphite or Molybdenum Strips: In some designs, heating elements are made from lightweight curved graphite or molybdenum strips, which are highly effective in high-temperature environments.
-
Materials Melted in Induction Furnaces:
- Metals: Common metals melted include stainless steel, aluminum, and precious metals like gold and silver. These metals are melted to make them more malleable for forming, molding, and reconfiguring.
- Specialized Alloys: Induction furnaces are also used to melt nickel, cobalt, and iron-based superalloys, as well as other specialized materials like tool steel, bearing steel, and magnetic alloys.
-
Applications of Induction Furnaces:
- Steel and Alloy Production: Induction furnaces can produce steel and alloys from alloyed waste, pure iron, and ferroalloys.
- Non-Ferrous Metals: They are also capable of smelting non-ferrous metals such as copper and aluminum, making them versatile for various industrial applications.
-
High-Temperature Resistance:
- Refractory Metals: High-temperature furnaces are often made from refractory metals, which are dense, hard, and highly resistant to heat and wear. These properties ensure the furnace can operate at extreme temperatures without structural failure.
By understanding these key points, a purchaser can make informed decisions about the materials and design features needed for their specific induction furnace requirements. The choice of materials directly impacts the furnace's performance, durability, and efficiency, making it crucial to select the right components for the intended application.
Summary Table:
Component | Materials Used | Key Benefits |
---|---|---|
Furnace Lining | Magnesia, Dolomite, Alumina | High melting points, durability, and protection against contamination. |
Furnace Body | Vacuum-formed high-purity alumina fiber | Excellent heat preservation, lightweight, and superior thermal insulation. |
Heating Elements | Iron-chrome aluminum, nickel chrome alloys | High resistance to heat and wear, even heat distribution. |
Alternative Heating | Graphite or molybdenum strips | Lightweight and effective in high-temperature environments. |
Metals Melted | Stainless steel, aluminum, precious metals | Versatile for forming, molding, and reconfiguring various metals and alloys. |
Specialized Alloys | Nickel, cobalt, iron-based superalloys | Ideal for high-performance applications in industrial settings. |
Ready to enhance your induction furnace performance? Contact our experts today for tailored solutions!