A batch furnace is a type of furnace designed to heat treat a single batch of components at a time. It operates by heating the furnace from room temperature to a predetermined maximum temperature, holding it at that temperature for a specified duration, and then cooling it at a controlled rate. Batch furnaces are versatile and can handle varying weights, sizes, and types of materials, making them ideal for low-volume production, deep case carburizing, or large-sized parts that are challenging to process in continuous furnaces. They are generally more cost-effective than continuous furnaces and can operate with or without a controlled atmosphere. Common types of batch furnaces include box, car-bottom, integral-quench, pit, and vacuum furnaces.
Key Points Explained:
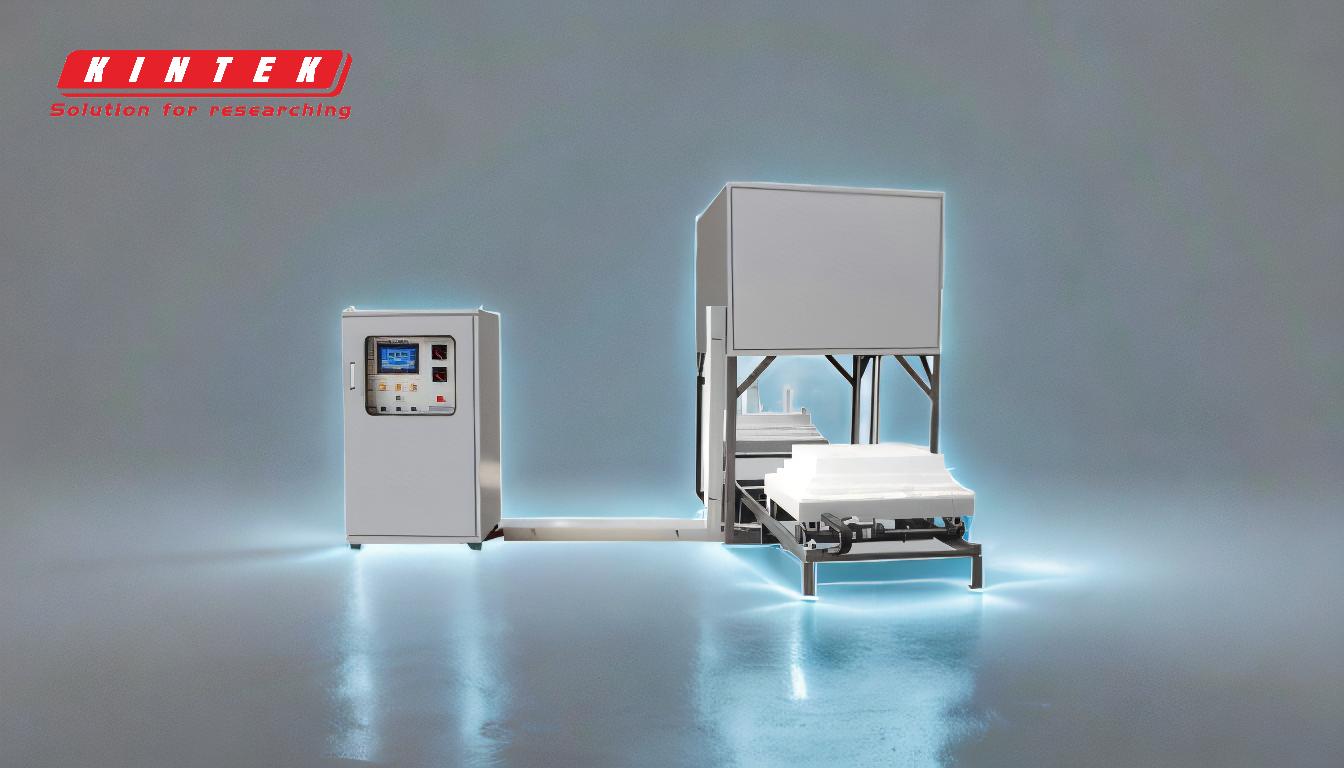
-
Definition of a Batch Furnace:
- A batch furnace is designed to heat treat one load or batch of components at a time. It processes the entire batch as a single unit, from heating to cooling, before moving on to the next batch.
- This method is distinct from continuous furnaces, which process materials in a constant flow.
-
Operational Process:
- Heating: The furnace is heated from room temperature to a specific maximum temperature at a controlled rate.
- Holding: The temperature is maintained for a predetermined period to ensure proper heat treatment.
- Cooling: The furnace is then cooled at a specified rate to complete the process.
- This cycle is repeated for each batch, allowing for customization based on the specific requirements of the materials being treated.
-
Types of Batch Furnaces:
- Box Furnaces: Enclosed furnaces ideal for small to medium-sized batches.
- Car-Bottom Furnaces: Larger furnaces that use rail-mounted cars to transport heavy or bulky loads.
- Integral-Quench Furnaces: Furnaces with integrated quenching chambers for rapid cooling.
- Pit Furnaces: Vertical furnaces used for treating long or tall components.
- Vacuum Furnaces: Furnaces that operate in a vacuum environment, ideal for materials sensitive to oxidation.
-
Applications:
- Batch furnaces are suitable for low-volume production runs, parts requiring deep case carburizing, or large components that are difficult to handle in continuous furnaces.
- They are commonly used in industries such as aerospace, automotive, and tool manufacturing.
-
Advantages:
- Flexibility: Can handle a wide range of materials, sizes, and heat treatment requirements.
- Cost-Effectiveness: Generally less expensive to purchase and operate than continuous furnaces.
- Customization: Each batch can be tailored to specific needs, making it ideal for specialized applications.
-
Comparison with Continuous Furnaces:
- Batch Furnaces: Process one batch at a time, making them suitable for low-volume or specialized production.
- Continuous Furnaces: Process materials in a constant flow, ideal for high-volume production with consistent requirements.
-
Atmosphere Control:
- Batch furnaces can operate with or without a controlled atmosphere, depending on the material and heat treatment process.
- Controlled atmospheres are used to prevent oxidation or to introduce specific gases for desired chemical reactions.
-
Design Variations:
- Batch furnaces come in various sizes and designs, from small hearth-style furnaces to large car-bottom furnaces.
- The design choice depends on the size and type of components being treated.
By understanding these key points, you can determine whether a batch furnace is the right choice for your specific heat treatment needs.
Summary Table:
Key Aspect | Details |
---|---|
Definition | Processes one batch of components at a time, from heating to cooling. |
Operational Process | Heating → Holding → Cooling, customizable for each batch. |
Types | Box, Car-Bottom, Integral-Quench, Pit, and Vacuum Furnaces. |
Applications | Low-volume production, deep case carburizing, large or specialized parts. |
Advantages | Flexibility, cost-effectiveness, and customization for specific needs. |
Atmosphere Control | Can operate with or without a controlled atmosphere. |
Comparison | Ideal for low-volume or specialized production vs. continuous furnaces. |
Need a batch furnace for your heat treatment needs? Contact our experts today to find the perfect solution!