Brazing is a versatile joining method that offers several advantages over other techniques like welding or soldering. It involves joining materials using a filler metal that melts at a lower temperature than the base metals, ensuring minimal thermal distortion and preserving the integrity of the components. Brazing is particularly advantageous for joining dissimilar materials, complex geometries, and high-precision assemblies. It is also suitable for mass production and can be performed in controlled environments like vacuum or hydrogen furnaces, ensuring clean, high-quality joints with minimal post-processing.
Key Points Explained:
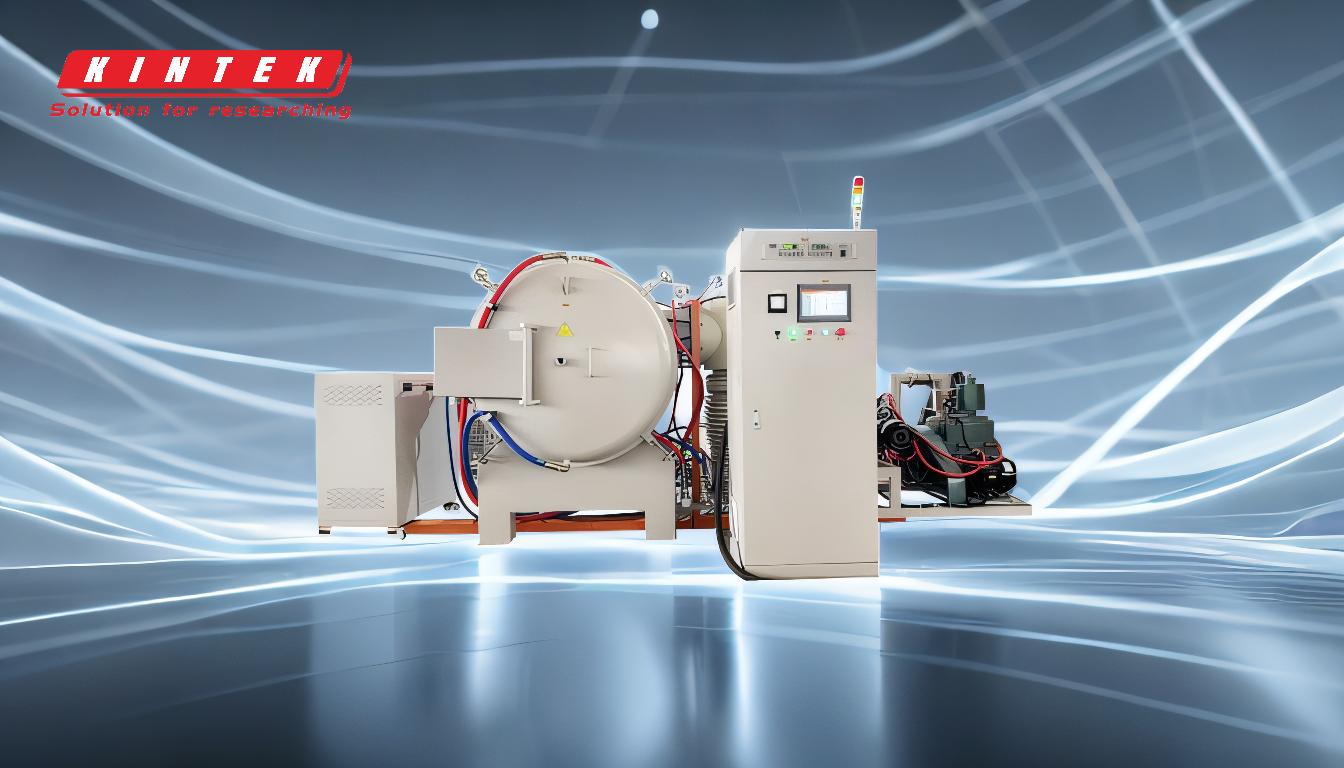
-
Preservation of Base Metal Integrity:
- Brazing does not melt the base metals, which allows for maintaining close tolerances and preventing weakening of the parts. The filler metal solidifies at the joint, creating a strong bond without compromising the structural integrity of the base materials.
-
Joining Dissimilar and Complex Materials:
- Brazing is highly effective for joining dissimilar materials, such as metals to ceramics, and can handle complex geometries. This makes it suitable for industries like aerospace, medical, and semiconductor manufacturing, where precision and material compatibility are critical.
-
Reduced Thermal Distortion:
- Compared to welding, brazing operates at lower temperatures, which minimizes thermal distortion and residual stress in the parts. This is especially beneficial for high-precision assemblies where dimensional accuracy is crucial.
-
High-Volume Mass Production:
- Brazing is well-suited for mass production due to its ability to join multiple parts simultaneously and its compatibility with automated processes. Techniques like vacuum brazing and furnace brazing enhance efficiency and consistency.
-
Clean and High-Quality Joints:
- Processes like vacuum brazing and hydrogen brazing produce clean, flux-free joints by removing oxides and contaminants. This results in aesthetically pleasing, high-quality joints that often require no additional post-processing.
-
Versatility in Process Control:
- Brazing allows precise control over heating and cooling cycles, ensuring uniform temperature distribution and minimizing thermal stress. This is particularly advantageous for complex assemblies and materials with varying thermal properties.
-
Cost and Time Efficiency:
- Brazing can integrate heat treatments like hardening or annealing into the same cycle, reducing processing time and costs. Additionally, the ability to braze multiple joints simultaneously further enhances its efficiency.
-
Applications in High-Tech Industries:
- The clean and precise nature of brazing makes it ideal for industries requiring tight tolerances and high-performance materials, such as aerospace, medical devices, and semiconductors.
By leveraging these advantages, brazing stands out as a reliable and efficient joining method for a wide range of applications, offering both technical and economic benefits.
Summary Table:
Advantage | Description |
---|---|
Preservation of Base Metal Integrity | Maintains close tolerances and prevents weakening of parts. |
Joining Dissimilar Materials | Effective for metals to ceramics and complex geometries. |
Reduced Thermal Distortion | Lower temperatures minimize distortion and residual stress. |
High-Volume Mass Production | Suitable for automated processes and simultaneous joining. |
Clean and High-Quality Joints | Flux-free joints with minimal post-processing. |
Versatility in Process Control | Precise heating and cooling cycles for uniform temperature distribution. |
Cost and Time Efficiency | Integrates heat treatments, reducing processing time and costs. |
Applications in High-Tech Industries | Ideal for aerospace, medical, and semiconductor manufacturing. |
Learn how brazing can enhance your manufacturing process—contact our experts today!