When an electric current passes through a heating element, the resistance within the material causes the conversion of electrical energy into heat, a phenomenon known as Joule heating. This process occurs because the electrons moving through the resistor collide with atoms, transferring kinetic energy and increasing the material's temperature. The heat generated is proportional to the resistance and the square of the current, making it an efficient method for producing heat in various applications. The direction of the current does not affect this heating process, distinguishing it from other thermal effects like the Peltier effect.
Key Points Explained:
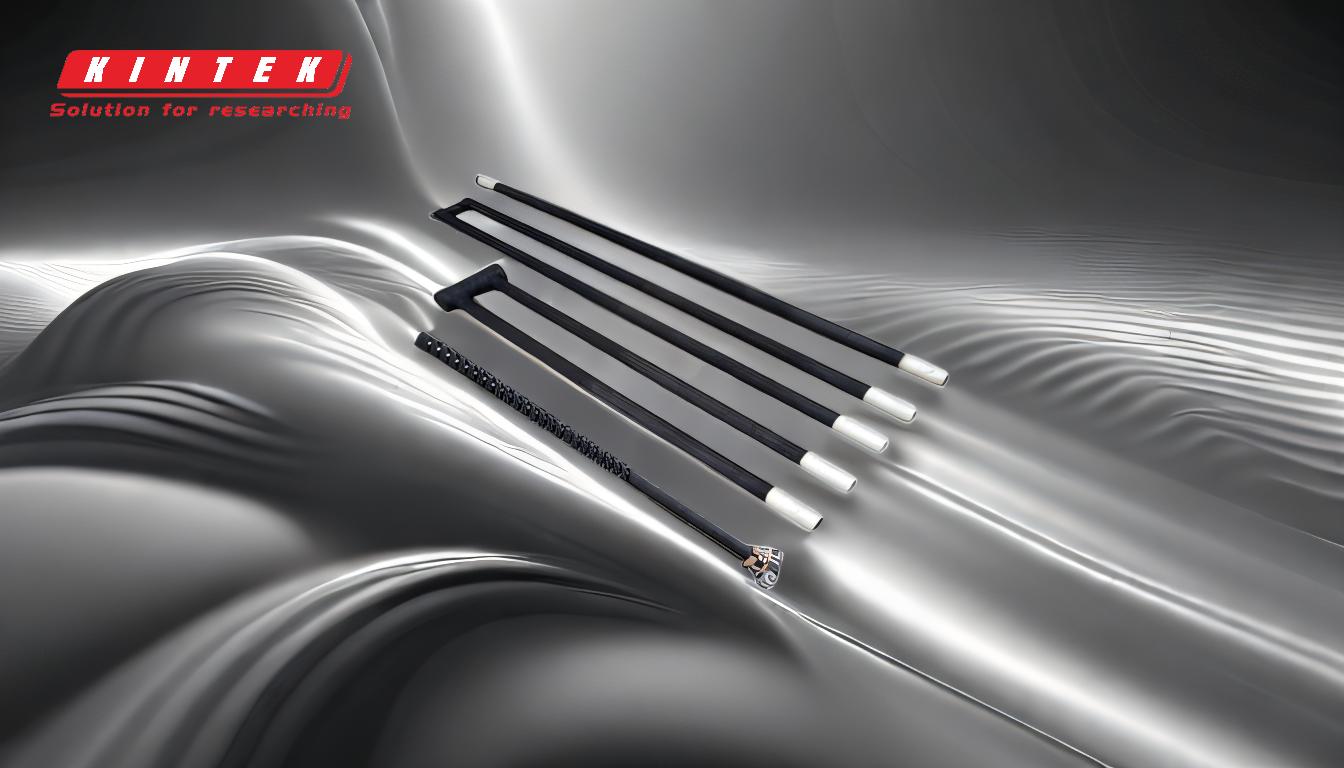
-
Joule Heating Principle:
- Explanation: Joule heating, also known as resistive or ohmic heating, is the process by which electrical energy is converted into thermal energy as electric current passes through a resistive material. This occurs due to the resistance encountered by the moving electrons, which results in energy dissipation in the form of heat.
- Relevance: This principle is fundamental to understanding why heating elements get hot when electricity flows through them. It explains the direct relationship between electrical energy input and heat output.
-
Role of Resistance in Heating:
- Explanation: The resistance of the heating element material is crucial in determining how much heat is generated. Materials with higher resistance will produce more heat for a given current compared to those with lower resistance.
- Relevance: This highlights the importance of selecting appropriate materials for heating elements based on their resistive properties to achieve desired heating levels.
-
Current and Heat Relationship:
- Explanation: The amount of heat generated is proportional to the square of the current (I²) passing through the element, as described by the formula ( P = I^2R ), where ( P ) is power (heat), ( I ) is current, and ( R ) is resistance.
- Relevance: This relationship is critical for designing heating elements that can safely and efficiently convert electrical energy into heat without overheating or failing.
-
Direction Independence of Heating:
- Explanation: Unlike some other thermal effects (e.g., Peltier effect), Joule heating does not depend on the direction of the current. Heat is generated regardless of whether the current is alternating (AC) or direct (DC).
- Relevance: This characteristic makes Joule heating versatile and applicable in both AC and DC systems, broadening its use in various heating applications.
-
Material Considerations:
- Explanation: The choice of material for a heating element affects its efficiency, durability, and maximum operating temperature. Common materials include nichrome, Kanthal, and ceramic, each with specific properties suited for different applications.
- Relevance: Understanding material properties helps in selecting the right heating element for specific needs, ensuring optimal performance and longevity.
-
Applications of Heating Elements:
- Explanation: Heating elements are used in a wide range of applications, from household appliances like toasters and ovens to industrial processes requiring precise temperature control.
- Relevance: This demonstrates the widespread utility of heating elements and underscores the importance of understanding their operation for effective application in various fields.
By breaking down the process into these key points, we gain a comprehensive understanding of why heating elements get hot and how they function within electrical circuits. This knowledge is essential for anyone involved in the design, selection, or application of heating elements in both consumer and industrial settings.
Summary Table:
Key Aspect | Explanation | Relevance |
---|---|---|
Joule Heating Principle | Electrical energy converts to heat as current passes through resistive material. | Explains why heating elements get hot and their energy-to-heat relationship. |
Role of Resistance | Higher resistance materials generate more heat for a given current. | Helps in selecting materials for desired heating levels. |
Current & Heat | Heat is proportional to the square of the current (I²). | Critical for safe and efficient heating element design. |
Direction Independence | Heat generation is unaffected by current direction (AC or DC). | Makes Joule heating versatile for various applications. |
Material Considerations | Materials like nichrome and Kanthal affect efficiency and durability. | Ensures optimal performance and longevity of heating elements. |
Applications | Used in household appliances and industrial processes. | Highlights the widespread utility of heating elements. |
Need help selecting the right heating element for your application? Contact our experts today!