Hydrogen is used in annealing furnaces primarily because it acts as a reducing agent, preventing oxidation and removing oxides from metal surfaces. This is particularly important in processes like sintering, annealing, and surface treatment of materials such as hard alloys, ceramics, and magnetic materials. Hydrogen annealing furnaces are versatile, capable of handling a wide range of applications, including ceramic sintering, metallization, and semiconductor alloy processing. Additionally, hydrogen provides a clean and controlled atmosphere, which is essential for high-precision metal components and processes like stainless steel deep-drawing. The use of hydrogen also ensures uniform heating and precise temperature control, making it ideal for applications requiring high thermal accuracy and material purity.
Key Points Explained:
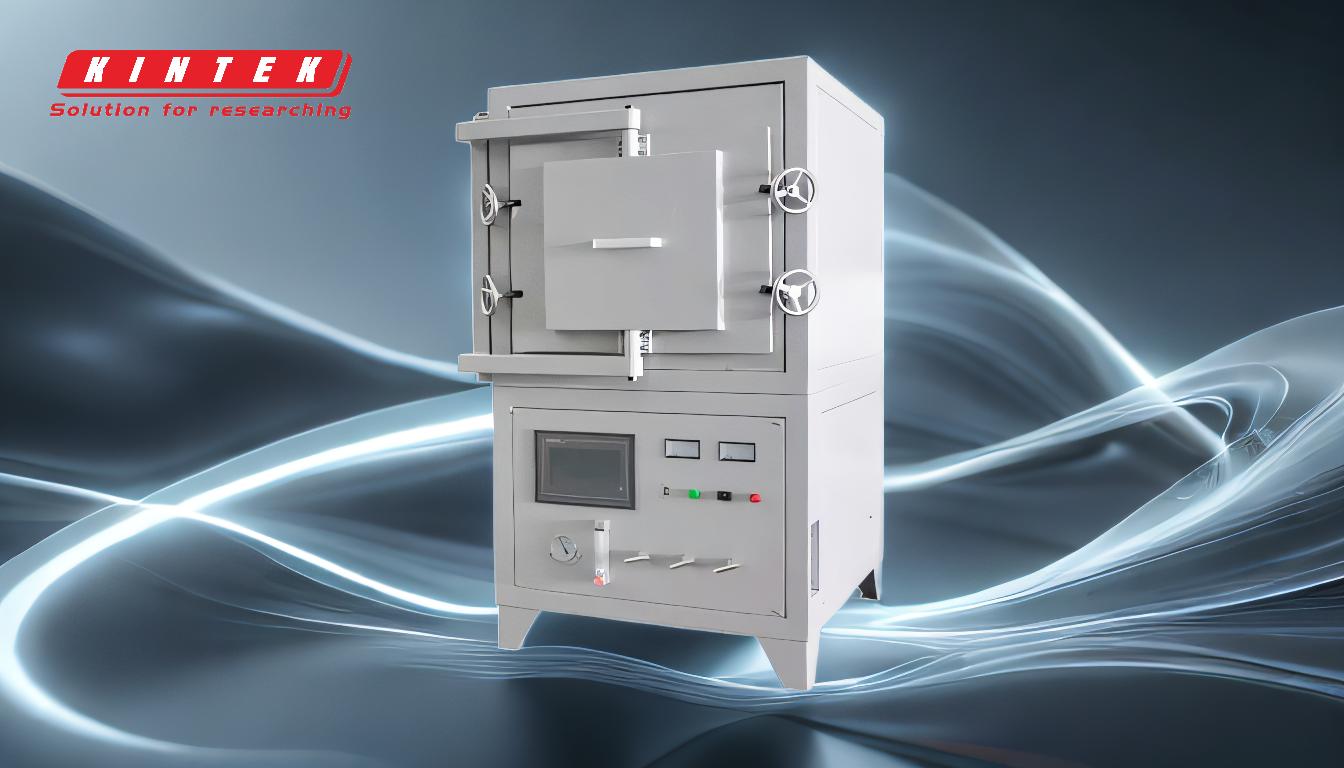
-
Hydrogen as a Reducing Agent:
- Hydrogen is highly effective in preventing oxidation during annealing. It reacts with oxygen to form water vapor, which is then removed from the furnace atmosphere. This ensures that the metal surfaces remain oxide-free, which is critical for processes like sintering and surface treatment.
- In a vacuum annealing furnace, hydrogen can be used alongside vacuum conditions to further enhance the reduction of oxides and improve material purity.
-
Versatility in Applications:
- Hydrogen annealing furnaces are used for a wide range of processes, including ceramic sintering, metallization, brazing, and semiconductor alloy processing. This versatility makes them suitable for industries ranging from electronics to automotive.
- The ability to handle different materials, such as hard alloys, ceramics, and magnetic materials, makes hydrogen annealing furnaces indispensable in advanced manufacturing.
-
Clean and Controlled Atmosphere:
- Hydrogen provides a clean atmosphere that minimizes contamination, which is crucial for high-precision metal components. This is especially important in industries like aerospace and medical devices, where material purity is paramount.
- The controlled atmosphere also ensures consistent results, which is essential for processes like stainless steel deep-drawing and the production of stainless steel bearings and cutting tools.
-
Temperature Control and Uniformity:
- Hydrogen annealing furnaces are equipped with advanced temperature control systems, such as piecewise program temperature controllers, which allow for precise temperature regulation. This ensures uniform heating, which is critical for achieving desired material properties.
- The temperature uniformity of ±3℃ to ±10℃ ensures that the entire workpiece is heated evenly, reducing the risk of defects and improving the quality of the final product.
-
Additional Features Enhancing Performance:
- Features like automatic and manual control, hydraulic systems with smooth lifting, and pressure control for water and air systems enhance the performance and reliability of hydrogen annealing furnaces.
- The inclusion of a paperless recorder allows for easy tracking and storage of usage data, which is important for quality control and process optimization.
In summary, hydrogen is used in annealing furnaces because of its ability to prevent oxidation, provide a clean and controlled atmosphere, and ensure precise temperature control. These properties make hydrogen annealing furnaces ideal for a wide range of applications, from ceramic sintering to semiconductor alloy processing, and ensure high-quality results in advanced manufacturing processes.
Summary Table:
Key Benefits of Hydrogen in Annealing Furnaces |
---|
Acts as a reducing agent to prevent oxidation and remove oxides |
Provides a clean, controlled atmosphere for high-precision processes |
Ensures uniform heating with temperature uniformity of ±3℃ to ±10℃ |
Versatile for applications like ceramic sintering, metallization, and semiconductor alloy processing |
Enhances material purity and reduces contamination |
Advanced temperature control systems for precise regulation |
Learn how hydrogen annealing furnaces can optimize your processes—contact our experts today!