Chemical vapor deposition (CVD) is a critical technology in modern materials science and engineering due to its versatility, precision, and ability to produce high-quality materials at relatively low temperatures and pressures. It overcomes the limitations of other methods like high-pressure high-temperature (HPHT) and detonation nanodiamond (DND) techniques, enabling the deposition of materials such as diamond and graphene over a wide range of substrates. CVD is particularly important in industries like semiconductors, where it is used to create thin films and coatings with specific properties. Its ability to produce large-area, high-quality materials like graphene at a low cost makes it indispensable for advanced applications in electronics, optics, and surface engineering.
Key Points Explained:
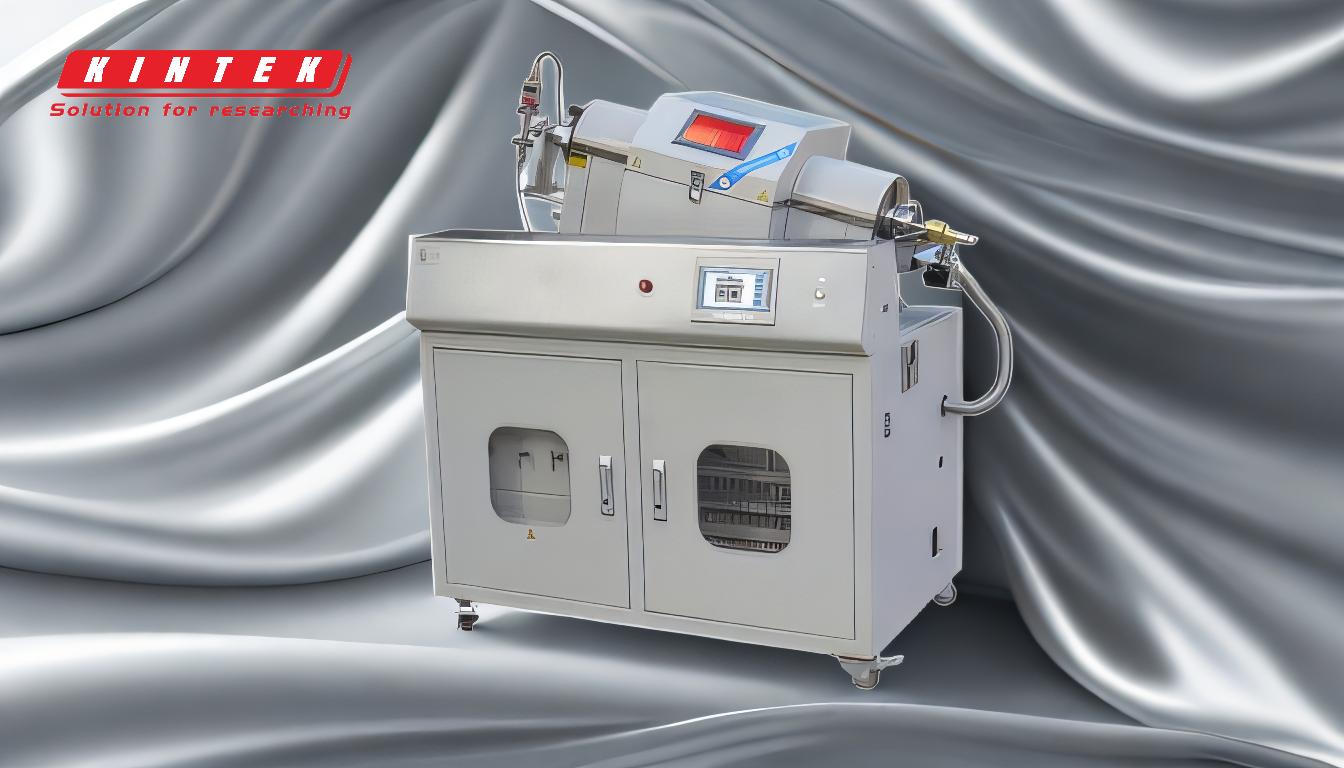
-
Versatility in Material Deposition:
- CVD allows the deposition of materials like diamond, graphene, and other thin films over a wide variety of substrates. This versatility makes it suitable for diverse engineering applications, from electronics to surface treatments.
- Unlike high-pressure high-temperature (HPHT) methods, CVD operates at subatmospheric pressures and temperatures below 1000°C, making it more adaptable and less energy-intensive.
-
Overcoming Limitations of Other Techniques:
- Traditional methods like HPHT and DND have limitations in terms of pressure, temperature, and substrate compatibility. Chemical vapor deposition overcomes these by enabling precise control over deposition conditions, resulting in high-quality materials with tailored properties.
-
Importance in Semiconductor Industry:
- CVD is extensively used in the semiconductor industry to deposit thin films of materials like silicon, silicon dioxide, and graphene. These films are essential for manufacturing integrated circuits, transistors, and other electronic components.
- The ability to produce uniform, high-purity films at a relatively low cost makes CVD a preferred method for semiconductor fabrication.
-
Production of Graphene:
- Since its first successful application in 2008 and 2009, CVD has become the most promising method for producing large-area, high-quality graphene. This material is crucial for advancements in electronics, energy storage, and composite materials.
- The low cost and scalability of CVD make it a viable option for industrial-scale graphene production, which is essential for its widespread adoption in various technologies.
-
Surface Engineering and Coatings:
- CVD is used to create coatings that improve the hardness, oxidation resistance, and friction properties of substrates. These coatings are vital in industries like aerospace, automotive, and tool manufacturing, where material performance is critical.
- Compared to physical vapor deposition (PVD), CVD can produce thicker and more durable coatings, making it suitable for applications requiring long-term durability.
-
Cost-Effectiveness and Scalability:
- CVD is relatively inexpensive compared to other deposition techniques, especially when producing large-area materials like graphene. This cost-effectiveness, combined with its scalability, makes it an attractive option for industrial applications.
- The ability to produce high-quality materials at a lower cost ensures that CVD remains a cornerstone of modern materials science and engineering.
In summary, chemical vapor deposition is a transformative technology that addresses the limitations of traditional methods, enabling the production of high-quality materials for a wide range of applications. Its importance in industries like semiconductors, electronics, and surface engineering cannot be overstated, making it a cornerstone of modern materials science and engineering.
Summary Table:
Key Aspect | Description |
---|---|
Versatility | Deposits materials like diamond and graphene on diverse substrates. |
Overcomes Limitations | Operates at low pressures/temperatures, surpassing HPHT and DND methods. |
Semiconductor Applications | Essential for thin films in integrated circuits and transistors. |
Graphene Production | Enables large-area, high-quality graphene at low cost. |
Surface Engineering | Creates durable coatings for aerospace, automotive, and tool manufacturing. |
Cost-Effectiveness | Scalable and inexpensive for industrial applications. |
Learn how chemical vapor deposition can revolutionize your projects—contact our experts today!