An inert atmosphere is used to create a controlled environment that minimizes or eliminates unwanted chemical reactions, particularly oxidation. This is achieved by replacing reactive gases, such as oxygen, with non-reactive gases like nitrogen, argon, or carbon dioxide. The primary purpose of an inert atmosphere is to protect materials, samples, or products from degradation, contamination, or damage caused by exposure to reactive elements. It is widely used in industries such as metallurgy, food preservation, and laboratory research, as well as in processes like heat treatment, sintering, and hot isostatic pressing. The benefits include reduced oxidation, improved product quality, enhanced safety, and the ability to maintain stability under varying conditions.
Key Points Explained:
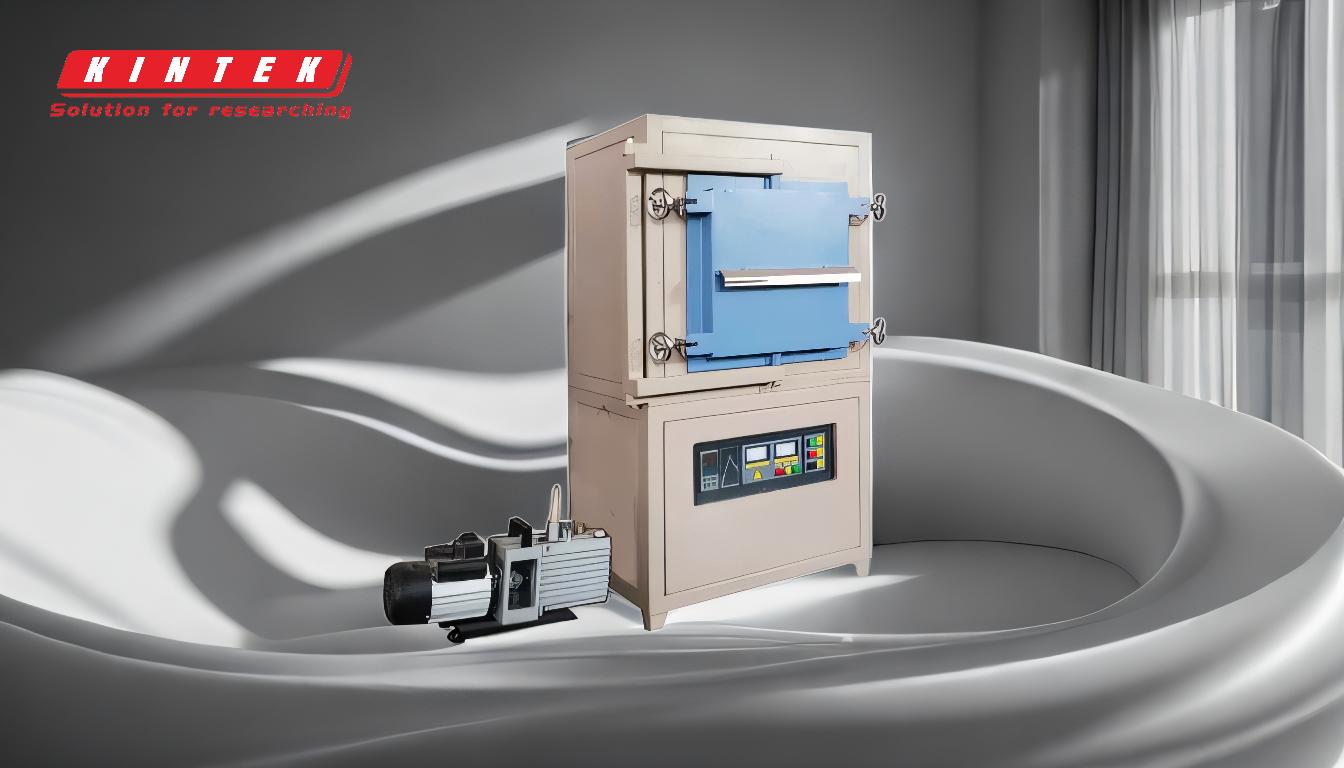
-
Prevention of Oxidation:
- Oxidation occurs when materials react with oxygen, leading to degradation, corrosion, or unwanted chemical changes.
- Inert atmospheres replace oxygen with non-reactive gases like nitrogen or argon, creating an environment where oxidation cannot occur.
- This is particularly important in heat treatment processes, where oxidation can compromise the structural integrity and quality of materials like steel.
-
Protection of Sensitive Materials:
- In laboratories and industrial settings, certain materials or samples are highly sensitive to oxygen or other reactive gases.
- Inert atmospheres ensure that these materials remain uncontaminated and undamaged during processing or storage.
- For example, in food preservation, inert gases like nitrogen are used to extend shelf life by preventing oxidation and microbial growth.
-
Enhanced Safety:
- Inert atmospheres reduce the risk of fire and explosions by displacing flammable gases or oxygen.
- This is critical in industries dealing with volatile substances or high-temperature processes.
- For instance, in metalworking, inert gases are used to prevent combustion during welding or heat treatment.
-
Improved Product Quality:
- By preventing unwanted chemical reactions, inert atmospheres ensure that products maintain their desired properties and quality.
- This is especially important in manufacturing processes like sintering or hot isostatic pressing, where surface oxidation or decarburization can weaken materials.
- The use of inert gases results in cleaner, more precise, and higher-quality end products.
-
Stability in Controlled Environments:
- Inert atmospheres provide a stable environment that remains unaffected by external changes in temperature, pressure, or humidity.
- This stability is crucial for processes requiring consistent conditions, such as semiconductor manufacturing or pharmaceutical production.
- The precision control offered by inert atmosphere systems ensures optimal performance and cost savings.
-
Applications Across Industries:
- Metallurgy: Inert atmospheres are used in heat treatment, welding, and metal fabrication to prevent oxidation and improve material properties.
- Food Preservation: Nitrogen or carbon dioxide is used to displace oxygen, extending the shelf life of perishable goods.
- Laboratory Research: Inert gases protect sensitive samples from contamination or degradation during experiments.
- Semiconductor Manufacturing: Inert atmospheres ensure the purity and stability of materials used in electronic components.
-
Cost Efficiency and Energy Savings:
- Modern inert atmosphere systems, such as furnaces with precision microprocessor controls and energy-efficient insulation, optimize performance while reducing operational costs.
- These systems minimize waste and improve process efficiency, making them a cost-effective solution for industries requiring controlled environments.
By understanding these key points, it becomes clear why inert atmospheres are indispensable in various applications. They provide a reliable and effective means of protecting materials, enhancing safety, and ensuring high-quality outcomes in diverse industrial and scientific processes.
Summary Table:
Key Benefits | Applications | Industries |
---|---|---|
Prevents oxidation | Heat treatment, sintering | Metallurgy, food preservation |
Protects sensitive materials | Laboratory research, food storage | Pharmaceuticals, semiconductor |
Enhances safety | Welding, metal fabrication | Manufacturing, chemical processing |
Improves product quality | Hot isostatic pressing | Aerospace, electronics |
Ensures stability in processes | Semiconductor manufacturing | Research and development |
Cost efficiency and energy savings | Precision-controlled systems | Energy, automotive |
Learn how inert atmospheres can optimize your processes—contact our experts today for tailored solutions!