Hydraulic Press: A Brief Introduction
Table of Contents
- Hydraulic Press: A Brief Introduction
- Application of Laboratory Hydraulic Press in Spectroscopy
- Role of Hydraulic Press in Powder Compaction for Composite Material Study
- Hydraulic Press in Material Testing
- Prototyping Microfluidic Devices Using Hydraulic Press
- Hydraulic Press in Pharmaceutical Research & Development
- Choosing the Right Hydraulic Press for Laboratory Application
Definition of Hydraulic Press
A hydraulic press is a machine that uses the pressure generated in a confined fluid to configure metals, plastics, rubber, and other materials. Its operation is governed by Pascal’s principle, which states that pressure applied to a confined fluid is transmitted unaltered throughout the fluid. In a hydraulic press, this pressure is transmitted to a piston that functions like a pump.
Types of Hydraulic Press
There are different types of hydraulic presses available, each designed for specific applications. Some of the common types include:
-
Manual Hydraulic Press: This type of press uses a hand-operated lever to apply load to a sample. It relies on a hydraulic ram powered by an electric motor or hand-operated levers. Manual hydraulic presses are versatile and relatively affordable, making them ideal for scientific laboratories.
-
Laboratory Hydraulic Press: Laboratory presses come in various sizes and configurations to suit different applications and lab workflows. They use high pressure to condense and mold materials. Laboratory hydraulic presses are commonly used in scientific laboratories for tasks like preparing powder samples for analysis.
-
Industrial Hydraulic Press: Industrial hydraulic presses are larger and more powerful than laboratory presses. They are used in industries such as metalworking, plastics processing, and woodworking. Industrial hydraulic presses can perform operations like forging, punching, blanking, deep drawing, and forming.
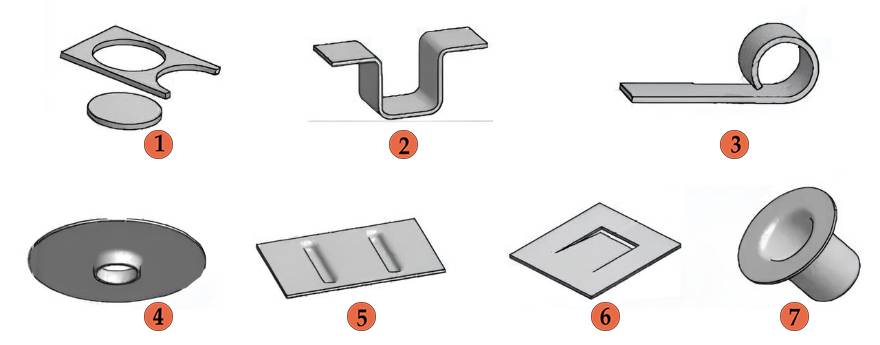
Differences between Laboratory and Industrial Hydraulic Presses
The main differences between laboratory and industrial hydraulic presses are in their size, power, and application. Laboratory presses are smaller, more compact, and generally used for smaller-scale tasks in scientific laboratories. On the other hand, industrial hydraulic presses are larger, more powerful, and designed for heavy-duty applications in industrial settings.
Laboratory presses are versatile and affordable, making them suitable for scientific research and experimentation. They are often used for sample preparation and analysis. Industrial presses, on the other hand, are built to withstand high loads and perform complex operations required in manufacturing processes.
When choosing a hydraulic press, it is important to consider the specific requirements of your application, available space, and the amount of force needed. Whether it's for a laboratory or an industrial setting, hydraulic presses offer immense versatility and precision in shaping and molding materials.
Application of Laboratory Hydraulic Press in Spectroscopy
Creating KBr Pellets for FTIR
When a mixed sample and KBr powder is compressed inside a die using a hydraulic press, its uniform force will produce a solid pellet which is mostly transparent to infrared light; but also contains a dilute quantity of sample, which is within the detection range of an FTIR instrument. The press applies an evenly distributed pressure over the sample, which transforms refractive material into transparent films that can be used for spectroscopic analysis. With the right press, this process can be completed in a few minutes.
FTIR is a type of spectroscopy that uses infrared light to study the properties of matter. In order to study the molecular structure of a powder sample, it first needs to be diluted in a transparent material – which is where the hydraulic press comes in. The hydraulic press is essential to create KBr (potassium bromide) pellets for FTIR analysis. The press ensures that the sample is uniformly compressed, resulting in a transparent pellet that can be easily analyzed using an FTIR instrument.
Application in XRF Spectroscopy
Similarly, XRF spectroscopy is an analytical technique used to determine the elemental composition of materials. By producing general sample pellets in a hydraulic press, the integrity of a sample can be maintained throughout the XRF process. By squeezing the sample between two pressure plates at high pressure, a hydraulic press ensures that the sample is completely compacted and ready for analysis.
XRF (X-ray fluorescence) spectroscopy is a non-destructive technique that uses X-rays to excite the atoms in a sample. This excitation causes the atoms to emit characteristic X-ray fluorescence, which can be measured and used to identify the elements present in the sample. To perform XRF analysis, the sample needs to be in pellet form. A hydraulic press is used to compress the sample into a solid pellet, ensuring that it is fully compacted and ready for analysis.
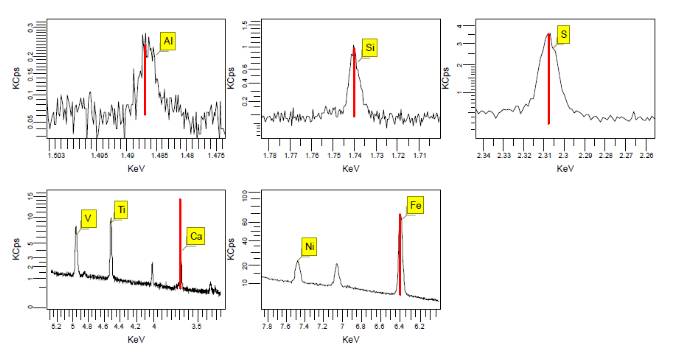
Powder Compaction for Composite Material Study
In addition to creating KBr pellets for FTIR and general sample pellets for XRF, a laboratory hydraulic press is also useful for other applications in spectroscopy. For example, it can be used to test the strength and durability of materials, investigate the effects of high pressure on different substances, and create pellets for sample analysis.
Laboratory hydraulic presses are smaller versions of industrial hydraulic presses that are specifically designed for research and testing purposes. They offer more precision and control, allowing researchers to apply the required load for sample preparation. The use of a laboratory hydraulic press ensures reproducible load for pressing high-quality pellets suitable for quantitative studies.
Overall, the application of a laboratory hydraulic press in spectroscopy, particularly in creating KBr pellets for FTIR and general sample pellets for XRF, is essential for sample preparation. It allows for the uniform compression of samples, ensuring accurate and reliable spectroscopic analysis.
Role of Hydraulic Press in Powder Compaction for Composite Material Study
Understanding Powder Compaction
Powder compaction is a process used to create a wide variety of composite materials. It involves the use of a hydraulic press to compress powder into a desired shape. This technique is essential for engineers and scientists who are working to develop new composite materials.
Usage in the Study of Ferromagnetics
In the study of ferromagnetics, hydraulic presses play a crucial role in powder compaction. By applying force to a material, the press can change its shape and create a magnetic field. This magnetic field aligns the spins of the electrons within the atoms of the substance. Hydraulic presses are used to control the strength of the material's magnetic field by adjusting the force applied, allowing for the manipulation of its properties.
Application in the Creation of Metal Matrix Composites (MMCs)
Hydraulic presses are also extensively used in the creation of metal matrix composites (MMCs). MMCs combine a metal with another substance, typically a ceramic or a polymer, to enhance mechanical strength, biocompatibility, and imaging properties. The most common method for producing MMCs is powder metallurgy, which involves blending the desired metal powder with a matrix material and using a hydraulic press to compact the mixture into the desired shape.
Metal matrix composites have a wide range of potential applications, particularly in the field of medicine. They can be used in orthopedic implants to provide greater strength and durability compared to traditional materials. The use of hydraulic presses in the production of MMCs ensures precise shaping and control of the composite material's properties.
Overall, hydraulic presses play a vital role in powder compaction for composite material study. They enable researchers and engineers to manipulate the properties of materials, study ferromagnetics, and create metal matrix composites with enhanced characteristics.
Hydraulic Press in Material Testing
Utilization of Hydraulic Press in Flexographic Printing
Hydraulic presses are versatile machines that are widely used in various industries for different applications. One of the key areas where hydraulic presses are utilized is in material testing. These presses offer several advantages over other types of presses, making them a popular choice among manufacturers.
Powder Compacting
One of the key applications of hydraulic presses in material testing is powder compacting. In this process, powdered materials are compressed into various designs and shapes using a hydraulic press. This allows manufacturers to create intricate shapes while being economical with materials.
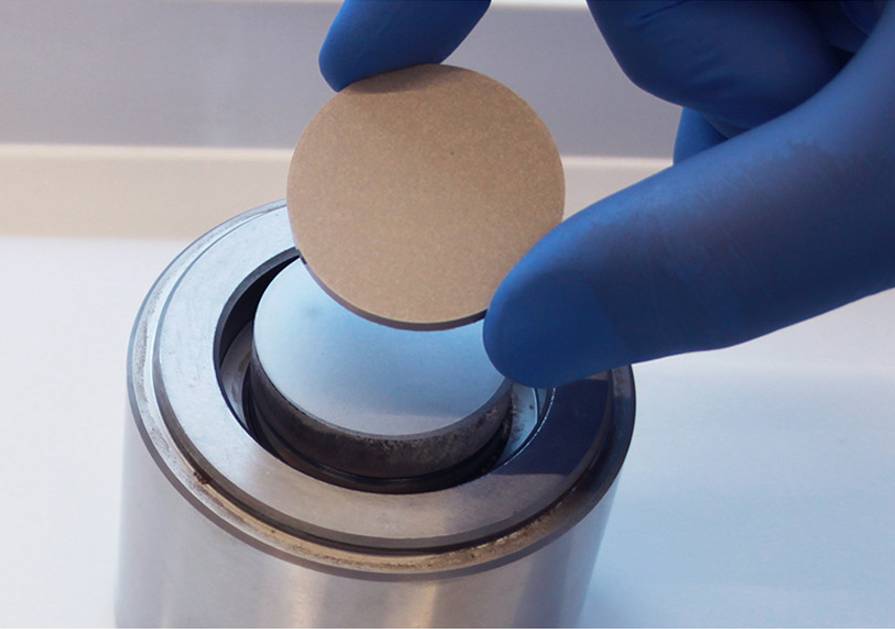
Concrete Compression Testing
Concrete manufacturers often test the tensile strength of their materials using hydraulic presses. These presses apply pressure to concrete samples, allowing manufacturers to determine the strength and quality of their concrete products. This helps ensure that the concrete meets the required standards and can withstand the intended applications.
Scrap Baling
Hydraulic presses are also used for scrap baling. This process involves crushing metal objects such as cars and machines to reduce their size for easy transport, processing, and storage. Hydraulic presses provide the necessary force to compact these metal objects, making them more manageable and efficient to handle.
Ceramics Manufacturing
In ceramics manufacturing, hydraulic presses have replaced high-temperature kiln manufacturing methods for producing ceramic tiles, bricks, and other objects. These presses can operate at room temperature, offering a more efficient and cost-effective solution for ceramics production. Manufacturers can create high-quality ceramic products with precise shapes and sizes using hydraulic presses.

Laboratory Testing
Hydraulic presses play a crucial role in laboratory testing. They allow manufacturers to test the quality and performance of their products in a laboratory setting. From testing the strength of materials to evaluating their durability, hydraulic presses provide a reliable and accurate method for assessing product quality.
Sample Preparation for XRF Analysis
Hydraulic presses are also used in sample preparation for X-ray fluorescence spectroscopy (XRF) analysis. XRF is a non-destructive analytical technique that quantifies fluorescent X-rays emitted from a sample. Hydraulic presses are used to compress powder mixtures into pellets, which are then analyzed using XRF. This enables rapid and high-volume sample preparation for accurate analysis.
Power Compaction for Composite Materials
Laboratory hydraulic presses are used in power compaction to create composite materials. This process is similar to sample preparation for spectroscopy, but the resulting composite materials are lightweight yet sturdy. These materials are used in studying ferromagnetics and metal matrix composites, providing valuable insights into their properties and behavior.
Material Testing
Hydraulic presses are also used to create test substances for analyzing material performance during manufacturing processes. For example, in flexographic printing, hydraulic presses assess blocking resistance by testing the print material's ability to adhere to itself when subjected to pressure. This helps manufacturers ensure that their print materials meet the required standards and can perform optimally in real-world applications.
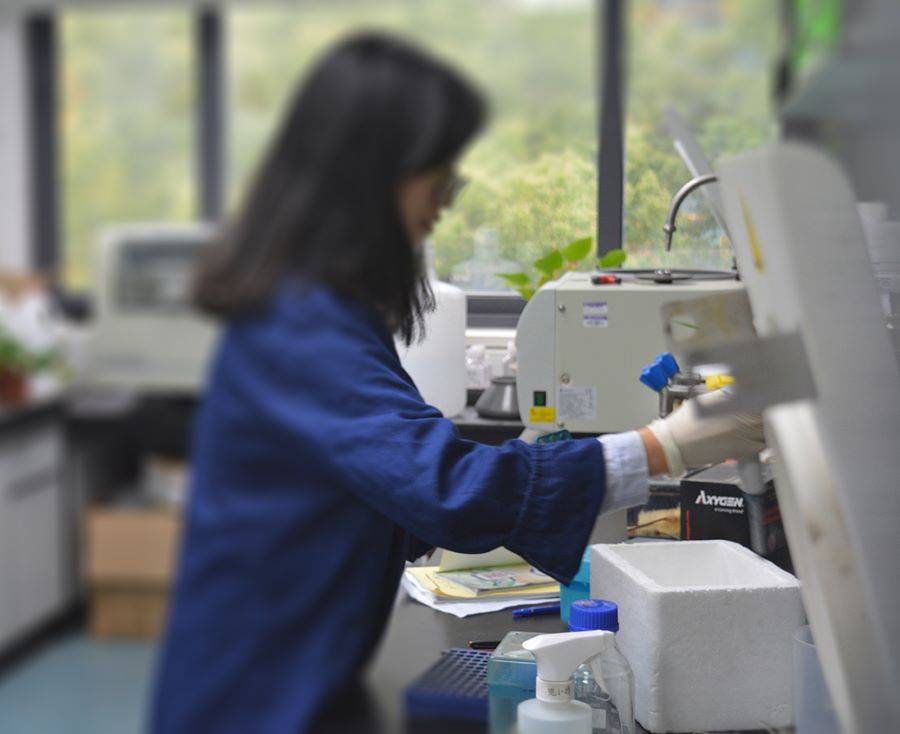
Prototyping Microfluidic Devices
Hydraulic presses can also be used to prototype microfluidic devices, which are increasingly sought-after for handling small liquid amounts. By using a hydraulic press, manufacturers can create exact prototypes of these devices, ensuring that the final products function correctly and meet the desired specifications.
In conclusion, hydraulic presses play a crucial role in material testing and offer several benefits for manufacturers. From powder compacting to concrete compression testing and from ceramics manufacturing to laboratory testing, hydraulic presses provide a reliable and efficient solution for various applications. These presses enable manufacturers to test the physical limits of different materials, evaluate their performance, and ensure the quality of their products. Whether it's in the field of construction, manufacturing, or research, hydraulic presses are an invaluable tool for material testing.
Prototyping Microfluidic Devices Using Hydraulic Press
Challenges in Microfluidic Device Prototyping
Prototyping microfluidic devices can be a challenge due to the small size of the components. However, using a hydraulic press can help overcome these challenges. A hydraulic press allows for quick and easy creation of prototypes, and it also ensures precision in the final device. This is crucial for ensuring proper functionality. Additionally, using a press eliminates the need for expensive and delicate manufacturing equipment, making it a cost-effective solution for microfluidic device prototyping.
Benefits of Using Hydraulic Press in Prototyping
-
Quick and Easy: A hydraulic press allows for the rapid creation of prototypes of microfluidic devices. This saves time in the development process and allows for faster iterations and improvements.
-
Precision: The use of a hydraulic press ensures precise prototyping, which is essential for microfluidic devices to function correctly. The press applies consistent pressure, resulting in accurate and reliable prototypes.
-
Cost-effectiveness: Press-based prototyping eliminates the need for expensive and delicate manufacturing equipment. This reduces costs and makes microfluidic device prototyping more accessible.
-
Versatility: Hydraulic presses can be used in various industries, including pharmaceutical research and development. For example, they can be used in dissolution testing, a quality control process that helps ensure the efficacy of pharmaceutical products. The press applies mechanical stress to break down the drugs into smaller pieces for analysis.
In conclusion, the use of a hydraulic press in prototyping microfluidic devices offers several benefits, including speed, precision, cost-effectiveness, and versatility. It is a valuable tool for overcoming the challenges associated with creating these small-scale devices and is particularly useful in industries such as pharmaceutical research and development.
Hydraulic Press in Pharmaceutical Research & Development
Usage in Dissolution Testing for Quality Control
Dissolution testing is a crucial quality control process in pharmaceutical research and development. It helps ensure the efficacy of pharmaceutical products by analyzing the potency and other attributes of the drug. One method used in dissolution testing involves the use of a hydraulic press.
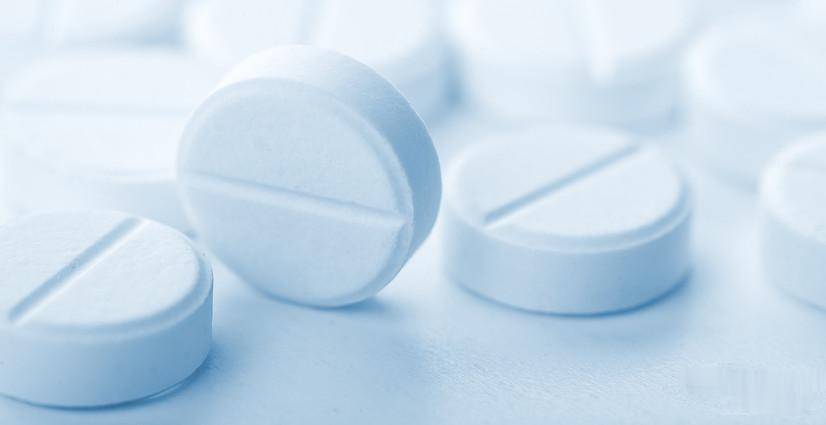
How the Hydraulic Press Works
The hydraulic press starts by creating a hollow cavity using a mechanical punch. This cavity serves as the space where the device walls will be formed. The punch is then placed inside the press chamber. Under pressure from the hydraulic system, the punch drives two weldable plates together, forming a single device entity. This ensures secure connections and prevents any fluid leakage from the system.
Importance of Dissolution Testing
Dissolution testing plays a vital role in ensuring the safety and effectiveness of drugs. It involves testing the rate and amount of active ingredients that dissolve in a liquid vehicle. This measurement helps determine how much of the drug will be released into the body and at what rate.
The Role of the Hydraulic Press
A hydraulic press is commonly used in dissolution testing. The process starts by carefully weighing the drug sample and placing it in a dialysis bag with a dissolution medium. The bag is then submerged in the vessel of the press. The press applies 1-10 tons of force repeatedly over time to ensure thorough mixing with the dissolution media. This mixing process allows for accurate measurement of the amount of material released from the system. The continued pressing also breaks down particles further, reinforcing precise results.
Advantages of Hydraulic Press in Pharmaceutical Research
The use of a hydraulic press offers several advantages in pharmaceutical research and development. One significant advantage is the ability to create prototypes of microfluidic devices quickly and precisely. This capability is essential for ensuring the proper functioning of the final device. Additionally, hydraulic press-based prototyping eliminates the need for expensive and delicate manufacturing equipment, making it a cost-effective option.
In conclusion, hydraulic presses play a crucial role in pharmaceutical research and development, particularly in dissolution testing for quality control. They enable efficient and accurate analysis of drug potency and other attributes. The use of a hydraulic press also offers advantages in creating prototypes of microfluidic devices, contributing to the advancement of pharmaceutical research.
Choosing the Right Hydraulic Press for Laboratory Application
Importance of Correct Equipment Selection
Why must lab managers and researchers choose the right hydraulic press? Every application will have unique requirements for clamping force, dwelling time, temperature, and several other factors that are necessary to the creation of a successful sample. Therefore, it is critical to select the press most suited for the specific application to achieve the best possible results.
Options by KINTEK
How does Kin-Tech’s extensive experience in the field make this choice easier? Kin-Tech can help make selecting the appropriate press an easy decision for you. With your application requirements, our sales team and engineers can use our extensive experience to provide a standard press or provide a custom option to fit your unique needs. However, if your workflow relies on pressed samples and your lab staff will need to produce them recurrently, they might find a manual hydraulic press to be quite laborious. In these instances, an automatic press will likely be more convenient and enable a quicker pace of work.
Are you trying to find the right hydraulic press for your laboratory application? Testing is a critical step in many research processes. It’s critical to use the right equipment to ensure accurate results.
Hydraulic presses are available in a variety of sizes and configurations and choosing the right one for your application can be a challenge. Fortunately, Kin-Tech offers a range of hydraulic presses to suit a wealth of applications. With our help, you can find the ideal press to suit your needs, ensuring accurate and repeatable results.
CONTACT US FOR A FREE CONSULTATION
KINTEK LAB SOLUTION's products and services have been recognized by customers around the world. Our staff will be happy to assist with any inquiry you might have. Contact us for a free consultation and talk to a product specialist to find the most suitable solution for your application needs!