PVD (Physical Vapor Deposition) coating is a versatile process that can be applied to a wide range of materials, including metals, plastics, ceramics, and even some organic materials. However, when it comes to wood, the application of PVD coating is not straightforward due to its organic nature and lack of vacuum compatibility. While PVD coatings are typically applied to inorganic materials that can withstand vacuum conditions and elevated temperatures, wood poses challenges due to its porous structure, moisture content, and inability to endure the high temperatures often associated with PVD processes. Pre-treatment methods, such as applying a vacuum-compatible coating or electroplating, could theoretically make wood suitable for PVD, but this remains unconventional and is rarely practiced in industrial applications.
Key Points Explained:
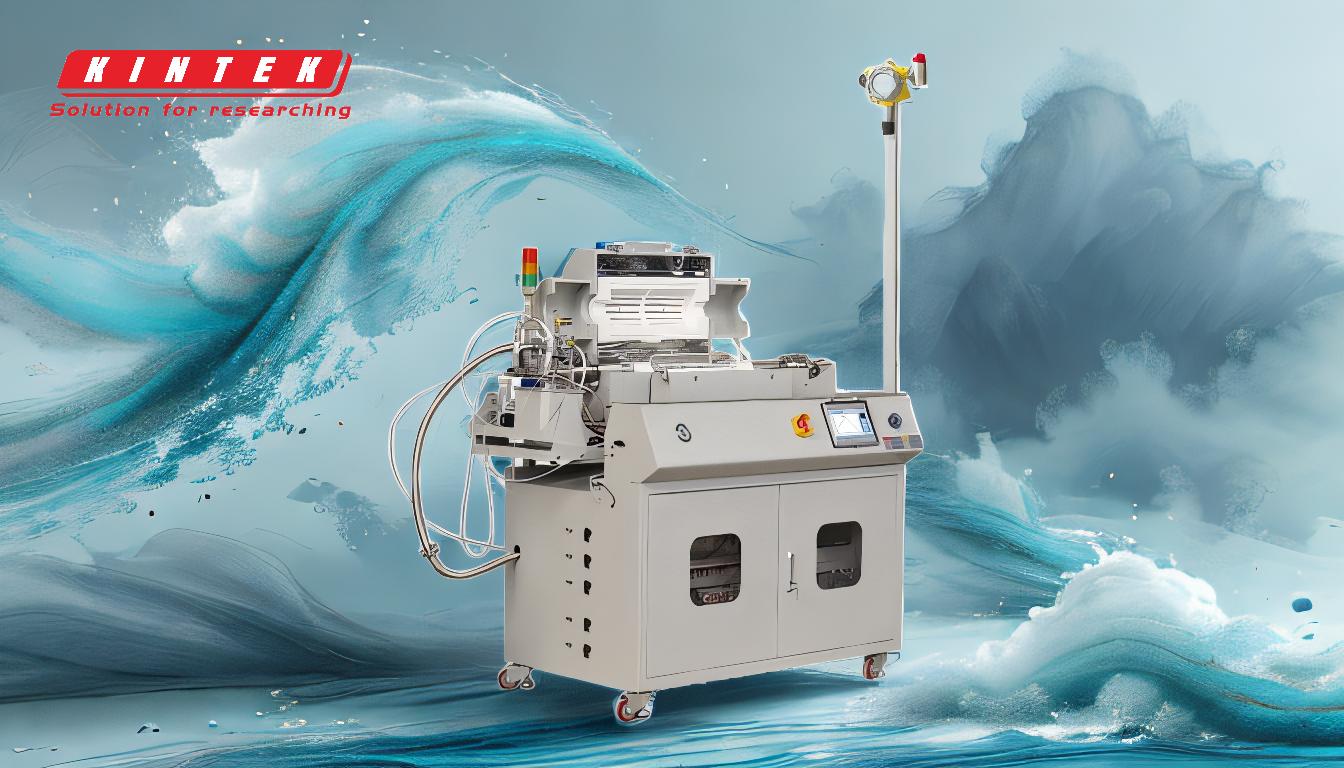
-
PVD Coating Basics:
- PVD coating is a process where a thin film is deposited onto a substrate in a vacuum environment.
- It is commonly used for metals, ceramics, plastics, and some organic materials.
- The process can be done at relatively low temperatures, making it suitable for a wide range of materials.
-
Material Compatibility:
- PVD coatings adhere best to inorganic materials like metals, ceramics, and certain plastics.
- Materials must be vacuum-compatible, meaning they can withstand the vacuum environment without degrading or releasing gases.
- Common substrates include stainless steel, titanium, glass, and ABS plastic.
-
Challenges with Wood:
- Wood is an organic material with a porous structure, making it unsuitable for direct PVD coating.
- The moisture content in wood can cause outgassing in a vacuum, which disrupts the PVD process.
- Wood cannot withstand the high temperatures often required for PVD coating, even though some PVD processes operate at lower temperatures.
-
Potential Solutions:
- Pre-treatment methods, such as applying a vacuum-compatible coating (e.g., nickel or chrome plating), could make wood suitable for PVD.
- Organic coatings or sealants could be used to create a barrier that prevents outgassing and makes the surface vacuum-compatible.
- However, these methods are unconventional and not widely practiced due to the complexity and cost involved.
-
Industrial Feasibility:
- While theoretically possible, PVD coating on wood is not a common industrial practice.
- The process would require significant pre-treatment and customization, making it less cost-effective compared to other coating methods.
- Alternative coating techniques, such as lacquering or varnishing, are more commonly used for wood due to their simplicity and effectiveness.
-
Applications and Limitations:
- PVD coating is typically used for materials requiring durability, corrosion resistance, or aesthetic finishes, such as metals and ceramics.
- For wood, PVD coating would primarily serve decorative purposes, but the challenges outweigh the benefits in most cases.
- If a wood-like appearance is desired, PVD coatings can be applied to other materials (e.g., plastics) that mimic the texture and color of wood.
In conclusion, while PVD coating on wood is theoretically possible with extensive pre-treatment, it is not a practical or common application due to the inherent challenges of working with organic materials in a vacuum environment. Alternative coating methods are generally preferred for wood substrates.
Summary Table:
Aspect | Details |
---|---|
PVD Coating Basics | Thin film deposition in a vacuum environment; suitable for inorganic materials. |
Material Compatibility | Best for metals, ceramics, and certain plastics; requires vacuum compatibility. |
Challenges with Wood | Porous structure, moisture content, and temperature sensitivity. |
Potential Solutions | Pre-treatment methods like vacuum-compatible coatings or sealants. |
Industrial Feasibility | Rarely practiced due to complexity and cost; alternatives like lacquering preferred. |
Applications | Primarily decorative; wood-like finishes achieved on other materials. |
Learn more about PVD coating solutions for unique materials—contact our experts today!