Heat treating metal twice is indeed possible and is often done to achieve specific material properties or to correct issues from a previous heat treatment. However, the feasibility and effectiveness of double heat treatment depend on the type of metal, the heat treatment processes used, and the desired outcomes. Below is a detailed explanation of the key considerations and implications of heat treating metal twice.
Key Points Explained:
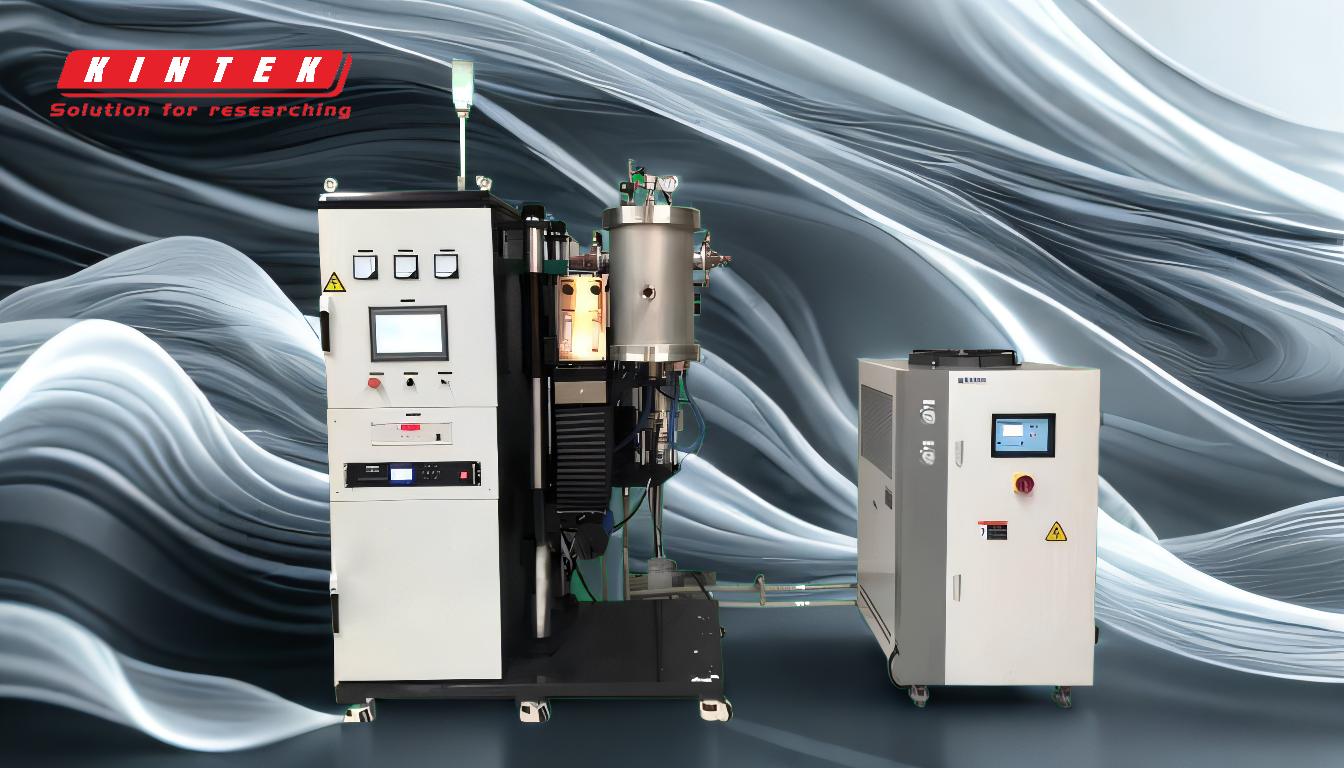
-
Purpose of Heat Treating Metal Twice
- Correcting Errors: If the first heat treatment did not achieve the desired hardness, toughness, or microstructure, a second heat treatment can be applied to rectify the issue.
- Achieving Specific Properties: Some metals require multiple heat treatments to achieve a combination of properties, such as strength and ductility. For example, maraging steels and precipitation-hardening stainless steels often undergo multiple heat treatment cycles.
- Stress Relief: A second heat treatment can be used to relieve residual stresses from the first treatment or from machining processes.
-
Factors Influencing Double Heat Treatment
- Material Type: Certain metals, such as tool steels, titanium alloys, and superalloys (e.g., Inconel), are more amenable to multiple heat treatments due to their ability to retain structural integrity under repeated thermal cycles.
- Heat Treatment Methods: Processes like vacuum heat treatment are particularly suitable for double heat treatment because they minimize oxidation, decarburization, and surface contamination, which can compromise the metal's properties.
- Temperature and Time: The temperature and duration of each heat treatment cycle must be carefully controlled to avoid over-tempering, grain growth, or other undesirable changes in the metal's microstructure.
-
Advantages of Double Heat Treatment
- Improved Mechanical Properties: A second heat treatment can refine the grain structure, enhance hardness, and improve wear resistance.
- Surface Quality: Vacuum heat treatment, in particular, ensures a bright and purified surface, free from oxidation or decarburization, which is critical for highly reactive materials like titanium.
- Stress Management: Double heat treatment can effectively reduce internal stresses, improving the metal's dimensional stability and performance under load.
-
Challenges and Risks
- Material Degradation: Repeated heat treatment can lead to grain coarsening, embrittlement, or loss of toughness, especially if the process parameters are not optimized.
- Cost and Time: Double heat treatment increases production time and costs, which may not be justified for all applications.
- Environmental Impact: Heat treatment processes generate waste water, waste gas, and other pollutants, so multiple treatments may exacerbate environmental concerns unless clean technologies are employed.
-
Applications of Double Heat Treatment
- Aerospace Components: Parts like airplane engine components and exhaust systems often undergo multiple heat treatments to ensure they can withstand extreme heat and stress.
- Tool and Die Making: Tool steels are frequently heat treated multiple times to achieve the necessary hardness and wear resistance.
- High-Performance Alloys: Materials like beryllium copper, stainless steels, and titanium alloys often require double heat treatment to optimize their mechanical and thermal properties.
-
Best Practices for Double Heat Treatment
- Precise Control: Use advanced heat treatment furnaces with accurate temperature and atmosphere control to ensure consistent results.
- Material Testing: Conduct thorough testing (e.g., hardness, microstructure analysis) after each heat treatment to verify the desired properties have been achieved.
- Environmental Considerations: Implement clean heat treatment technologies to minimize waste and pollution.
In conclusion, heat treating metal twice is a viable and often necessary process for achieving specific material properties or correcting issues. However, it requires careful consideration of the material, heat treatment method, and process parameters to avoid unintended consequences. Advanced techniques like vacuum heat treatment are particularly beneficial for double heat treatment, as they ensure high-quality results with minimal environmental impact.
Summary Table:
Key Considerations | Details |
---|---|
Purpose | Correct errors, achieve specific properties, and relieve stress. |
Factors | Material type, heat treatment methods, temperature, and time. |
Advantages | Improved mechanical properties, better surface quality, and stress management. |
Challenges | Material degradation, increased costs, and environmental impact. |
Applications | Aerospace components, tool and die making, and high-performance alloys. |
Best Practices | Precise control, material testing, and environmental considerations. |
Optimize your metal properties with double heat treatment—contact our experts today to learn more!