Hardening is a heat treatment process used to increase the hardness and strength of metals, typically through heating and rapid cooling (quenching). While it significantly improves mechanical properties, it can also affect the dimensions of the material. The dimensional changes during hardening are influenced by factors such as material composition, quenching medium, and the geometry of the part. These changes can result in warping, distortion, or even cracking if not properly controlled. Understanding the relationship between hardening and dimensional stability is crucial for manufacturers to ensure the final product meets specifications.
Key Points Explained:
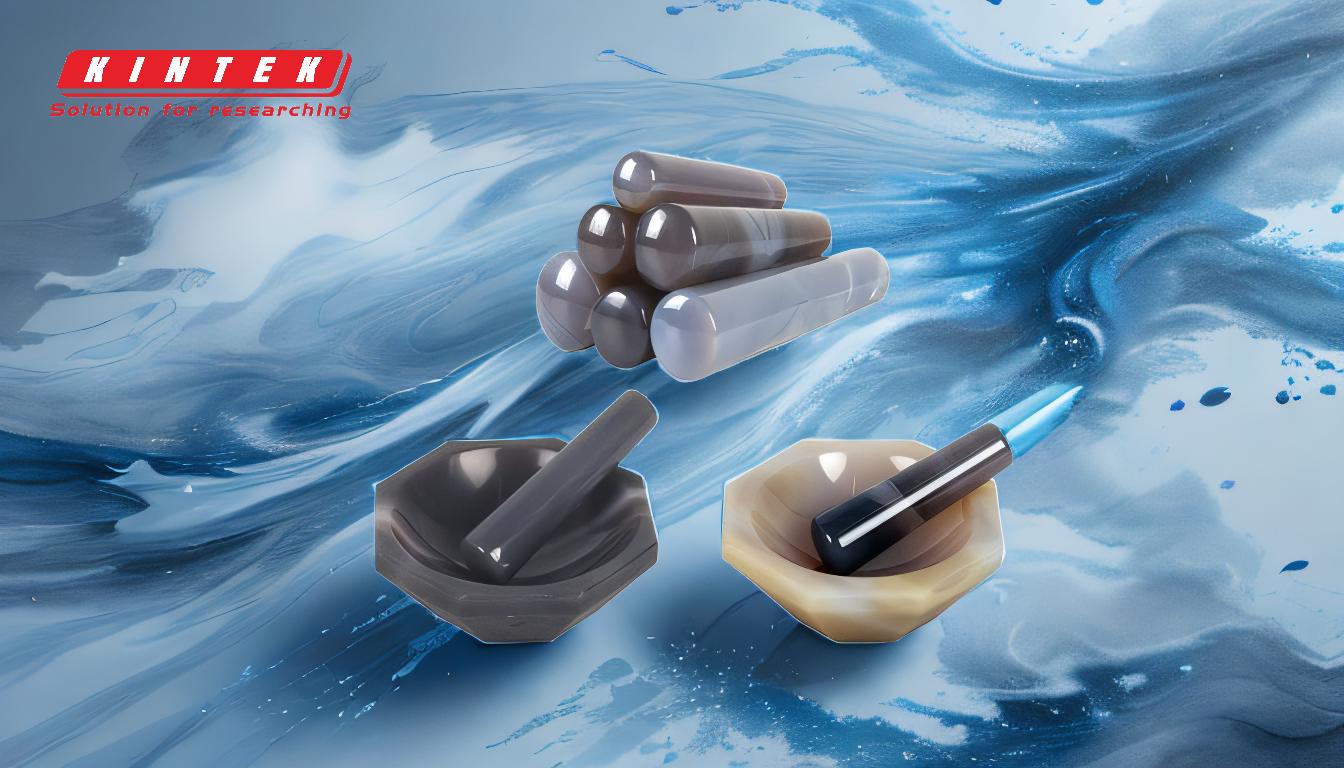
-
Mechanism of Hardening and Dimensional Changes:
- Hardening involves heating the metal to a high temperature and then rapidly cooling it. This process alters the microstructure of the metal, transforming it into a harder state, such as martensite in steel.
- The rapid cooling during quenching introduces internal stresses, which can cause dimensional changes. These stresses arise due to uneven cooling rates across the material, leading to warping or distortion.
- The magnitude of dimensional changes depends on the material's thermal expansion coefficient, phase transformations, and the cooling rate.
-
Factors Influencing Dimensional Changes:
- Material Composition: Alloying elements in the metal can affect its response to hardening. For example, high-carbon steels are more prone to distortion due to their higher hardness potential.
- Quenching Medium: The choice of quenching medium (oil, water, or air) impacts the cooling rate. Faster cooling mediums like water increase the risk of distortion and cracking.
- Part Geometry: Complex shapes or thin sections are more susceptible to dimensional changes because they cool unevenly, leading to higher internal stresses.
-
Mitigating Dimensional Changes:
- Precision Control of Quenching: Using controlled quenching techniques, such as interrupted quenching or martempering, can reduce internal stresses and minimize distortion.
- Stress Relieving: Post-hardening heat treatments, like tempering, help relieve residual stresses and stabilize dimensions.
- Design Considerations: Engineers can design parts with uniform cross-sections and avoid sharp corners to reduce stress concentrations during quenching.
-
Practical Implications for Equipment and Consumable Purchasers:
- When selecting materials for components that require hardening, purchasers should consider the material's susceptibility to dimensional changes and choose alloys with better dimensional stability.
- For equipment like furnaces and quenching systems, investing in advanced control systems can ensure uniform heating and cooling, reducing the risk of distortion.
- Collaborating with heat treatment specialists can help optimize the hardening process for specific applications, ensuring both hardness and dimensional accuracy.
By understanding the interplay between hardening and dimensional changes, manufacturers can make informed decisions to achieve the desired mechanical properties while maintaining dimensional integrity.
Summary Table:
Key Factor | Impact on Dimensional Changes |
---|---|
Material Composition | Alloying elements influence distortion; high-carbon steels are more prone to warping. |
Quenching Medium | Faster cooling (e.g., water) increases distortion and cracking risks. |
Part Geometry | Complex shapes or thin sections cool unevenly, leading to higher internal stresses. |
Mitigation Strategies | Controlled quenching, tempering, and uniform part design reduce dimensional changes. |
Optimize your hardening process for dimensional accuracy—contact our experts today!