Heat treating aluminum is a common process used to enhance its mechanical properties, including strength. The process involves heating the aluminum to a specific temperature, holding it at that temperature for a set period, and then cooling it at a controlled rate. This treatment alters the microstructure of the aluminum, leading to improved strength, hardness, and other desirable properties. The effectiveness of heat treatment depends on the specific alloy of aluminum, the temperature and duration of heating, and the cooling method used. Understanding these factors is crucial for achieving the desired strength and performance in aluminum components.
Key Points Explained:
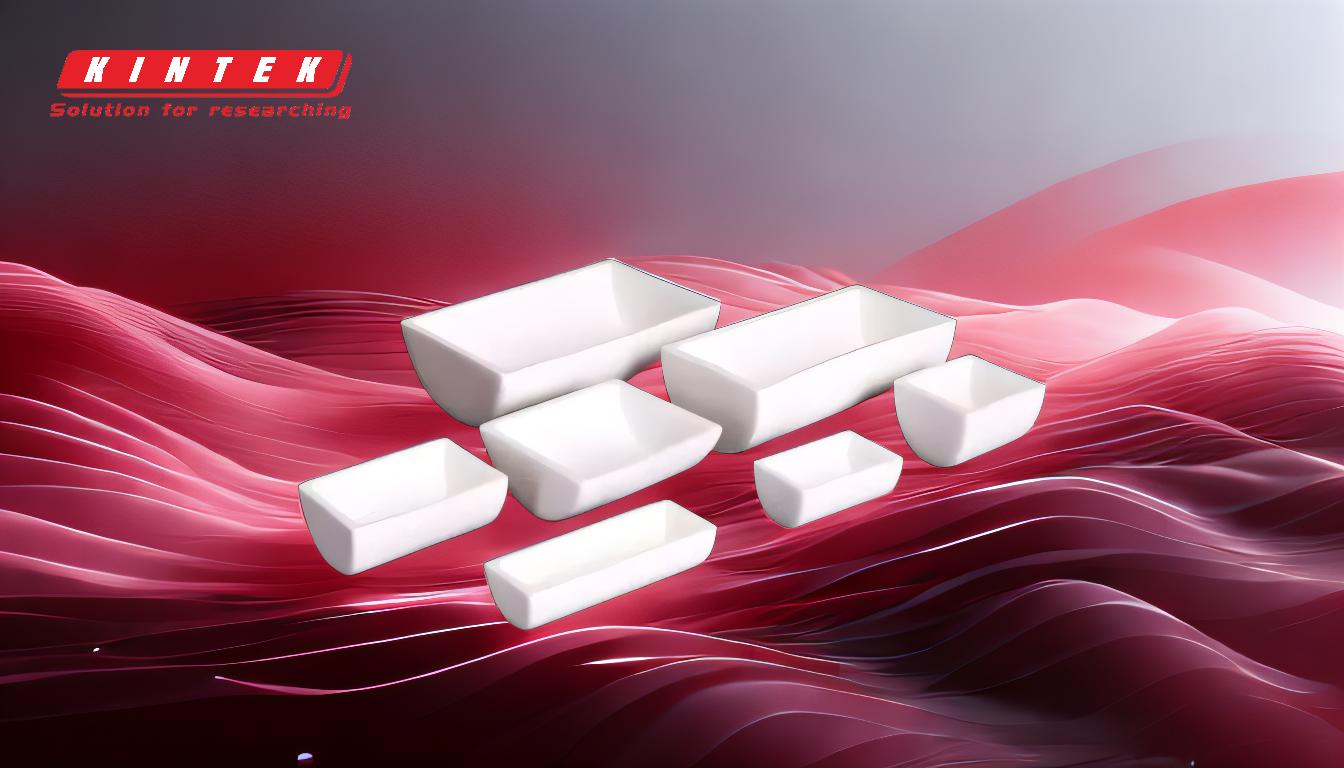
-
What is Heat Treatment?
- Heat treatment is a process that involves heating and cooling metals to alter their physical and mechanical properties without changing their shape. For aluminum, this process can significantly enhance strength, hardness, and resistance to wear and corrosion.
-
How Heat Treatment Affects Aluminum
- When aluminum is heated, its microstructure changes. The heat allows the alloying elements within the aluminum to dissolve and form a solid solution. Upon cooling, these elements precipitate out, forming small particles that strengthen the metal by impeding the movement of dislocations within the crystal structure.
-
Types of Heat Treatment for Aluminum
- Solution Heat Treatment: The aluminum is heated to a temperature where the alloying elements dissolve into the base metal. This is followed by rapid cooling (quenching) to trap the elements in solution.
- Precipitation Hardening (Aging): After solution heat treatment, the aluminum is aged at a lower temperature to allow the alloying elements to precipitate out, forming strengthening particles.
- Annealing: This process involves heating the aluminum to a specific temperature and then slowly cooling it to soften the metal, making it more workable.
-
Factors Influencing the Effectiveness of Heat Treatment
- Alloy Composition: Different aluminum alloys respond differently to heat treatment. Some alloys, like the 2000, 6000, and 7000 series, are specifically designed to benefit from heat treatment.
- Temperature and Time: The temperature and duration of heating must be carefully controlled to achieve the desired properties. Overheating or underheating can lead to suboptimal results.
- Cooling Rate: The rate at which the aluminum is cooled after heating can significantly impact its final properties. Rapid cooling (quenching) is often used to lock in the desired microstructure.
-
Benefits of Heat Treating Aluminum
- Increased Strength: Heat treatment can significantly increase the tensile strength and yield strength of aluminum, making it suitable for high-stress applications.
- Improved Hardness: The process can also enhance the hardness of aluminum, improving its resistance to wear and abrasion.
- Enhanced Corrosion Resistance: Some heat treatments can improve the corrosion resistance of aluminum, making it more durable in harsh environments.
-
Applications of Heat-Treated Aluminum
- Aerospace: Heat-treated aluminum is widely used in the aerospace industry for components that require high strength-to-weight ratios.
- Automotive: In the automotive industry, heat-treated aluminum is used for parts like engine blocks, pistons, and wheels, where strength and durability are critical.
- Construction: Heat-treated aluminum is used in construction for structural components that need to withstand heavy loads and environmental stresses.
-
Limitations and Considerations
- Cost: Heat treatment can add to the cost of aluminum components due to the energy and equipment required.
- Complexity: The process requires precise control of temperature, time, and cooling rates, which can be complex and requires specialized knowledge.
- Material Selection: Not all aluminum alloys are suitable for heat treatment. It's essential to choose the right alloy for the intended application.
In conclusion, heat treating aluminum can indeed make it stronger, but the effectiveness of the process depends on various factors, including the alloy composition, heat treatment method, and cooling rate. By carefully controlling these variables, manufacturers can significantly enhance the mechanical properties of aluminum, making it suitable for a wide range of demanding applications.
Summary Table:
Key Aspect | Details |
---|---|
What is Heat Treatment? | A process to alter aluminum's microstructure for improved mechanical properties. |
Types of Heat Treatment | Solution Heat Treatment, Precipitation Hardening, Annealing. |
Key Benefits | Increased strength, improved hardness, enhanced corrosion resistance. |
Applications | Aerospace, automotive, and construction industries. |
Factors Influencing | Alloy composition, temperature, time, and cooling rate. |
Ready to enhance your aluminum components' strength? Contact our experts today to learn more!