Heat treatment is a critical process in metallurgy that significantly impacts the hardness of metallic alloys. By controlling the rate of diffusion and cooling within the microstructure of the metal, heat treatment can manipulate various mechanical properties, including hardness. This process involves heating the metal to a specific temperature, holding it at that temperature for a certain period, and then cooling it at a controlled rate. The changes in hardness are primarily due to the transformation of the metal's microstructure, such as the formation of martensite in steel, which is a hard and brittle phase. Understanding how heat treatment affects hardness is essential for industries that require materials with specific mechanical properties.
Key Points Explained:
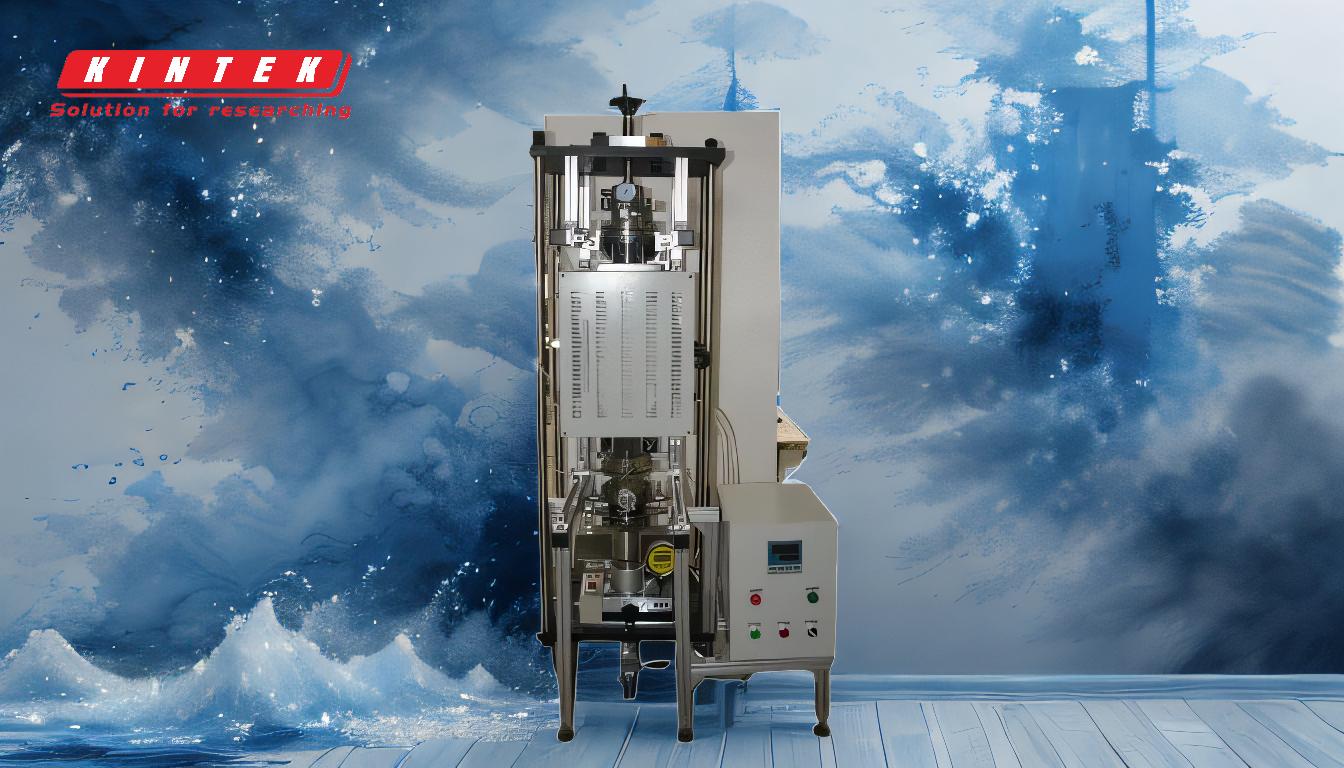
-
Definition of Heat Treatment:
- Heat treatment involves heating a metal to a specific temperature, maintaining it at that temperature for a set period, and then cooling it at a controlled rate.
- This process is used to alter the physical and sometimes chemical properties of a material to achieve desired characteristics such as increased hardness, improved strength, or enhanced ductility.
-
Mechanisms of Hardness Change:
- Microstructural Transformation: The primary way heat treatment changes hardness is through the transformation of the metal's microstructure. For example, in steel, heating to a high temperature and then rapidly cooling (quenching) can transform the microstructure into martensite, which is significantly harder than the original structure.
- Diffusion Control: The rate of diffusion of atoms within the metal is controlled during heat treatment. Slower cooling rates allow for more diffusion, leading to softer structures like pearlite, while rapid cooling limits diffusion, resulting in harder structures like martensite.
- Precipitation Hardening: In some alloys, heat treatment can cause the precipitation of fine particles within the metal matrix, which can increase hardness by impeding the movement of dislocations.
-
Types of Heat Treatment Affecting Hardness:
- Annealing: This process involves heating the metal to a specific temperature and then slowly cooling it. Annealing generally reduces hardness and increases ductility, making the metal easier to work with.
- Quenching: Rapid cooling of the metal from a high temperature, typically by immersing it in water or oil. Quenching increases hardness by forming martensite in steels.
- Tempering: After quenching, tempering is often used to reduce brittleness by reheating the metal to a lower temperature. This process can slightly decrease hardness but improves toughness.
- Case Hardening: This involves hardening only the surface layer of the metal while keeping the core relatively soft. Techniques like carburizing or nitriding are used to achieve this.
-
Factors Influencing Hardness Changes:
- Cooling Rate: The faster the cooling rate, the harder the metal will generally become. Rapid cooling prevents the formation of softer phases.
- Alloy Composition: Different alloys respond differently to heat treatment. For example, carbon content in steel significantly affects its ability to harden.
- Temperature and Time: The specific temperature and duration of heating and cooling cycles are critical. Incorrect temperatures or times can lead to insufficient hardness or excessive brittleness.
-
Practical Applications:
- Manufacturing: Heat treatment is widely used in manufacturing to produce components with specific hardness and strength requirements, such as gears, springs, and cutting tools.
- Aerospace: In the aerospace industry, heat-treated alloys are used for their high strength-to-weight ratio and resistance to wear and fatigue.
- Automotive: Heat treatment is essential in the automotive industry for producing durable and reliable engine components, transmission parts, and chassis elements.
-
Considerations for Equipment and Consumable Purchasers:
- Material Selection: Understanding the heat treatment process is crucial when selecting materials for specific applications. Purchasers need to consider the desired hardness and other mechanical properties.
- Quality Control: Ensuring that the heat treatment process is correctly applied is vital. Purchasers should work with suppliers who have robust quality control measures in place.
- Cost and Efficiency: Heat treatment can be energy-intensive and costly. Purchasers should evaluate the cost-effectiveness of different heat treatment methods and their impact on the final product's performance.
In conclusion, heat treatment is a powerful tool for altering the hardness of metallic alloys. By controlling the heating and cooling processes, manufacturers can achieve a wide range of mechanical properties tailored to specific applications. Understanding the principles and techniques of heat treatment is essential for anyone involved in the selection and procurement of materials and equipment.
Summary Table:
Aspect | Details |
---|---|
Definition | Heating, holding, and cooling metal to alter hardness and other properties. |
Mechanisms | Microstructural transformation, diffusion control, precipitation hardening. |
Types | Annealing, quenching, tempering, case hardening. |
Factors | Cooling rate, alloy composition, temperature, and time. |
Applications | Manufacturing, aerospace, automotive industries. |
Purchasing Considerations | Material selection, quality control, cost-efficiency. |
Optimize your material performance with expert heat treatment solutions—contact us today!