Nitriding is a surface hardening process that introduces nitrogen into the surface of a metal, typically steel, to improve wear resistance, fatigue strength, and corrosion resistance. One common concern regarding nitriding is whether it affects the dimensions of the treated parts. Generally, nitriding is known to cause minimal dimensional changes, but these changes can vary depending on factors such as the material being treated, the nitriding process used, and the specific conditions of the treatment. Below, we explore the key aspects of how nitriding may or may not affect dimensions.
Key Points Explained:
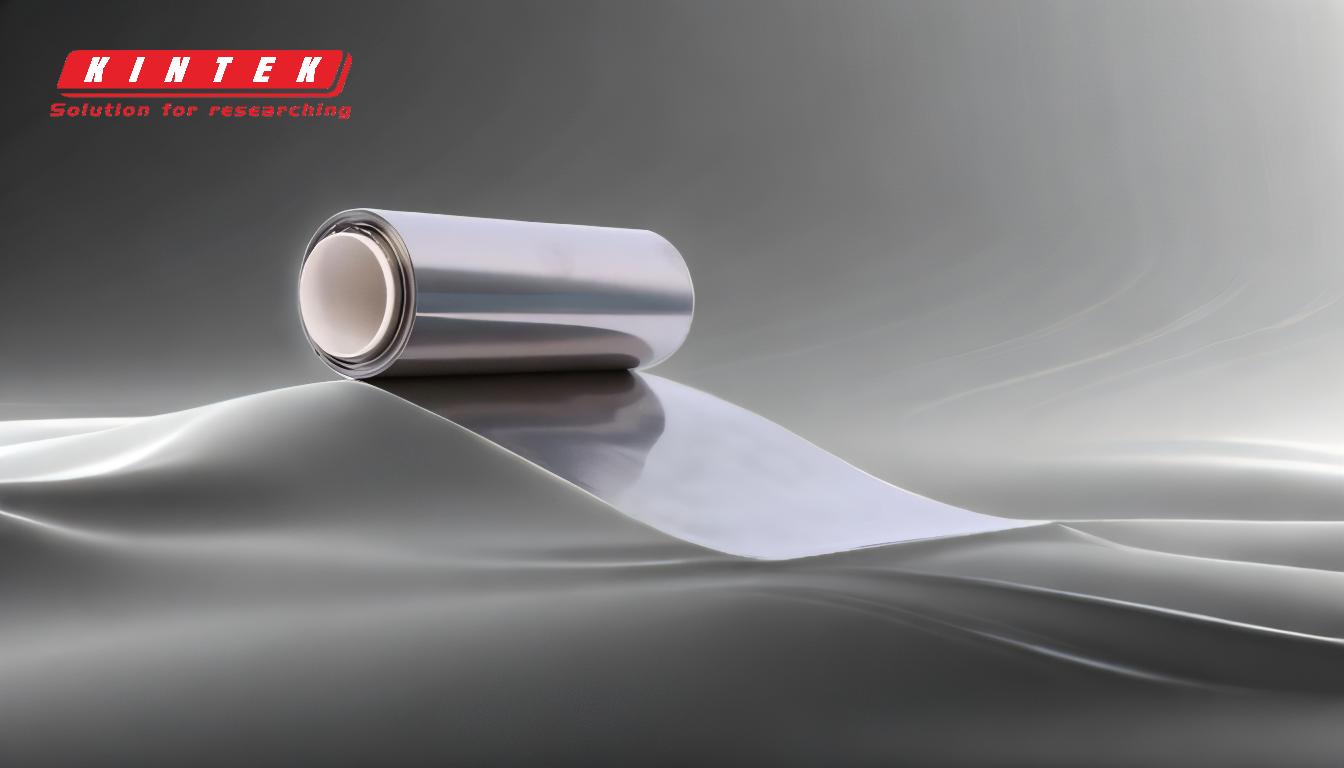
-
Minimal Dimensional Changes in Nitriding
- Nitriding is a low-temperature process, typically conducted between 500°C and 580°C, which is below the transformation temperature of most steels. This low temperature minimizes thermal distortion and dimensional changes compared to other heat treatment processes like carburizing or quenching.
- The process primarily affects the surface layer of the material, creating a hardened case depth without significantly altering the core dimensions. This makes nitriding suitable for precision components where dimensional stability is critical.
-
Factors Influencing Dimensional Changes
- Material Composition: The type of steel or alloy being treated can influence the extent of dimensional changes. For example, low-alloy steels may experience less distortion compared to high-alloy steels due to differences in thermal expansion coefficients and phase transformations.
- Process Type: Different nitriding methods, such as gas nitriding, plasma nitriding, or salt bath nitriding, can have varying effects on dimensions. Plasma nitriding, for instance, is often preferred for its ability to provide uniform case depths and minimal distortion.
- Case Depth: The depth of the nitrided layer can impact dimensional changes. Deeper case depths may lead to slight growth or expansion of the surface layer, but this is typically within acceptable tolerances for most applications.
-
Surface Growth and Its Implications
- During nitriding, nitrogen atoms diffuse into the surface, forming nitrides that can cause slight surface growth. This growth is usually in the range of a few micrometers, which is negligible for many applications but may require consideration for high-precision components.
- The surface growth is often predictable and can be accounted for during the design and machining stages to ensure final dimensions meet specifications.
-
Mitigating Dimensional Changes
- Pre-Treatment Machining: To compensate for potential surface growth, parts can be machined slightly undersized before nitriding. This ensures that the final dimensions after treatment are within the desired tolerances.
- Post-Treatment Finishing: In some cases, a light finishing process, such as grinding or polishing, may be applied after nitriding to achieve precise dimensions and surface finish.
-
Applications Where Dimensional Stability is Critical
- Nitriding is widely used in industries such as aerospace, automotive, and tooling, where dimensional stability is essential. Components like gears, crankshafts, and molds often undergo nitriding to enhance performance without compromising dimensional accuracy.
In conclusion, while nitriding can cause minor dimensional changes, these are typically predictable and manageable. By understanding the factors influencing these changes and implementing appropriate pre- and post-treatment measures, manufacturers can ensure that nitrided components meet the required dimensional tolerances. This makes nitriding a reliable choice for applications demanding both surface hardness and dimensional precision.
Summary Table:
Aspect | Details |
---|---|
Dimensional Changes | Minimal, typically within a few micrometers. |
Key Influencing Factors | Material composition, process type, and case depth. |
Surface Growth | Predictable and manageable, often accounted for in design stages. |
Mitigation Strategies | Pre-treatment machining and post-treatment finishing. |
Applications | Aerospace, automotive, and tooling industries. |
Ensure your components maintain precision after nitriding—contact our experts today for tailored solutions!