Heating elements are essential components in various heating applications, from household appliances to industrial furnaces. They are made from a wide range of materials, including metals, graphite, and silicon carbide, each chosen for specific properties like high resistivity, thermal stability, and resistance to oxidation. The manufacturing process involves shaping these materials into forms like wires, ribbons, or panels, often with protective measures to enhance durability and performance. The choice of material and design depends on the application's temperature requirements, environmental conditions, and desired heating efficiency.
Key Points Explained:
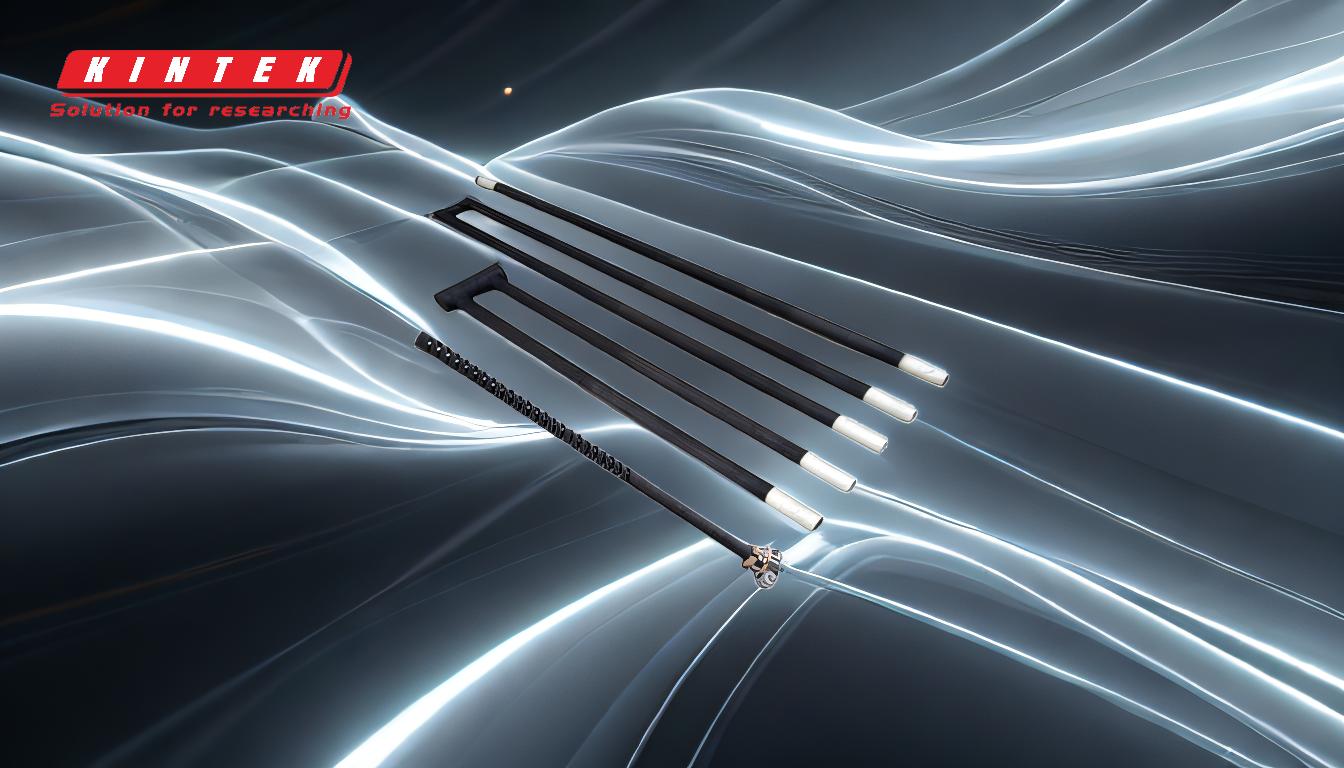
-
Materials Used in Heating Elements:
- Metallic Materials: Common metals include nickel-chromium alloys, stainless steel, tungsten, molybdenum, and tantalum. These materials are chosen for their high resistivity and ability to withstand high temperatures.
- Non-Metallic Materials: Graphite and silicon carbide are popular for their thermal stability and resistance to oxidation. Graphite is particularly noted for its uniform thermal fields and long service life.
-
Forms and Shapes:
- Wires and Ribbons: Heating elements are often made from resistance wire or ribbon, which can be straight or coiled. This form is common in household appliances like toasters and hair dryers.
- Panels and Strips: In industrial applications, heating elements are shaped into cylindrical, semi-circular, or flat panels. Molybdenum and graphite strips are also used, with options for pure or lanthanated molybdenum.
-
Protective Measures:
- Oxidation Protection: Materials like tungsten, molybdenum, and graphite are sensitive to oxygen and must be protected to prevent oxidation, which can degrade performance. This is often achieved through the use of protective coatings or environments.
- Insulation and Shielding: In high-temperature applications, heating elements may be shielded with materials like carbon felt and stainless steel sleeves to provide insulation and thermal shock resistance.
-
Applications:
- Household Appliances: Heating elements in devices like toasters and hair dryers are typically made from metallic wires or ribbons.
- Industrial Furnaces: High-temperature furnaces use exotic materials like platinum, tungsten disilicide, and silicon carbide. These materials can withstand extreme temperatures and provide uniform heating.
- Specialized Heating: Applications like floor heating, roof heating, and pathway heating to melt snow often use metallic or graphite elements designed for durability and efficiency.
-
Performance Characteristics:
- High Purity and Uniformity: Materials like high-purity graphite offer small changes in resistivity and uniform thermal fields, ensuring consistent performance.
- Rapid Heating: Some designs, particularly those using graphite, can reach high temperatures quickly, often within 90 minutes, making them suitable for applications requiring rapid heating.
By understanding the materials, forms, protective measures, and applications of heating elements, manufacturers can select the most appropriate design for their specific needs, ensuring optimal performance and longevity.
Summary Table:
Aspect | Details |
---|---|
Materials | Metals (e.g., nickel-chromium, tungsten), graphite, silicon carbide |
Forms | Wires, ribbons, panels, strips |
Protective Measures | Oxidation protection, insulation, shielding |
Applications | Household appliances, industrial furnaces, specialized heating systems |
Performance | High purity, uniform heating, rapid temperature rise |
Need the right heating element for your application? Contact our experts today for tailored solutions!