Reducing porosity during sintering is a critical goal in materials processing to achieve denser, stronger, and more reliable products. The porosity of a sintered material is influenced by several factors, including the initial porosity of the green compact, sintering temperature, sintering time, atmosphere, particle size, and applied pressure. By optimizing these variables, it is possible to minimize porosity and enhance the material's mechanical and physical properties. Key strategies include controlling the initial green compact's porosity, selecting appropriate sintering temperatures and times, using smaller particle sizes, and applying external pressure during sintering. Additionally, the sintering atmosphere and heating rate play significant roles in pore elimination and densification.
Key Points Explained:
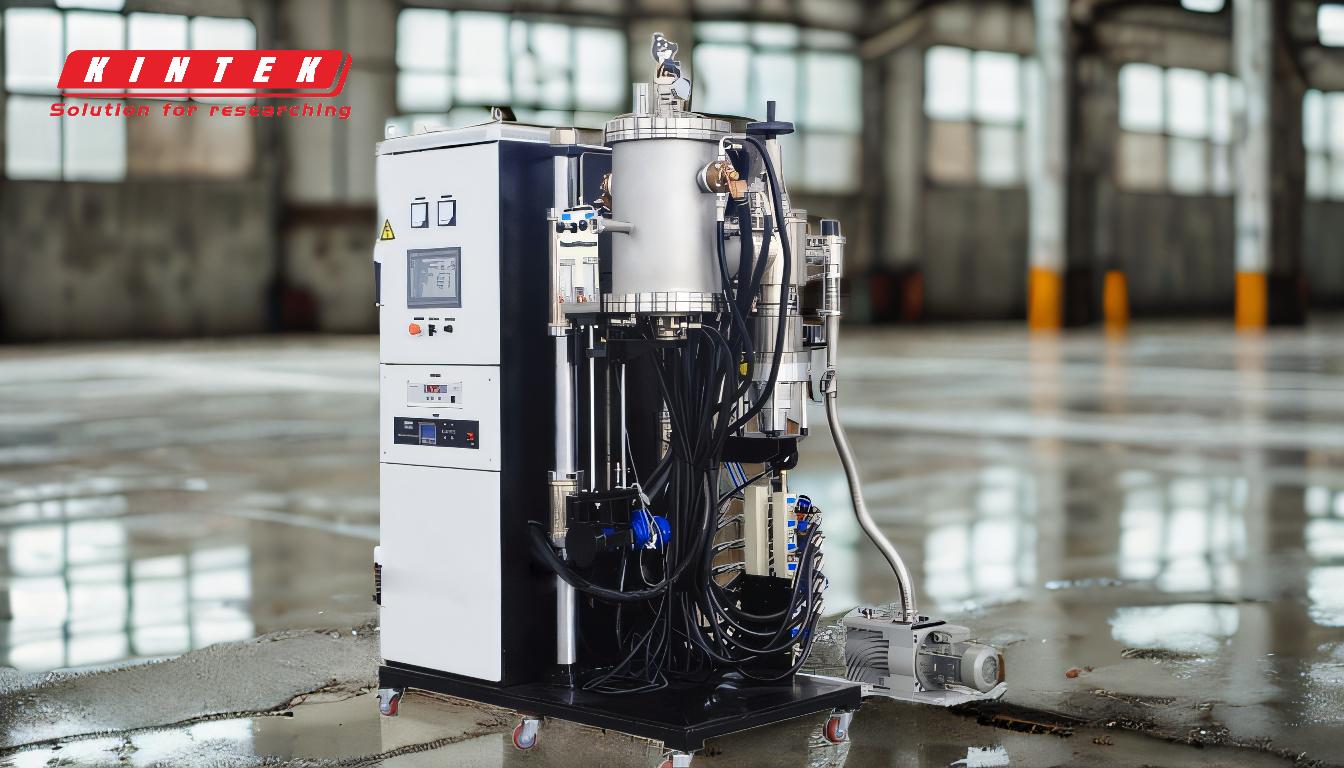
-
Control Initial Porosity of the Green Compact:
- The initial porosity of the green compact (the unsintered material) is a critical factor in determining the final porosity after sintering. A lower initial porosity generally leads to a denser final product.
- To reduce initial porosity, ensure proper compaction techniques, such as using higher compaction pressures or optimizing the particle size distribution in the green compact. Uniform particle packing minimizes large voids and promotes better densification during sintering.
-
Optimize Sintering Temperature:
- Sintering temperature significantly influences porosity reduction. Higher temperatures enhance atomic diffusion, which helps eliminate pores by promoting particle bonding and grain growth.
- However, excessively high temperatures can lead to undesirable grain growth or material decomposition. Therefore, it is essential to identify the optimal sintering temperature for the specific material to balance porosity reduction and material integrity.
-
Adjust Sintering Time:
- Longer sintering times allow more time for pore elimination through mechanisms like boundary diffusion and lattice diffusion. This is particularly important for materials with high initial porosity or those requiring solid-state diffusion, such as pure oxide ceramics.
- However, excessively long sintering times may lead to over-sintering, which can degrade material properties. The sintering time should be optimized based on the material and desired final porosity.
-
Use Smaller Particle Sizes:
- Smaller particles have a higher surface area-to-volume ratio, which increases the driving force for sintering and enhances densification. Smaller particles also reduce diffusion distances, making pore elimination more efficient.
- Ensure a uniform particle size distribution to avoid localized densification issues and promote homogeneous sintering.
-
Apply External Pressure (Hot Pressing or Hot Isostatic Pressing):
- Applying pressure during sintering (e.g., hot pressing or hot isostatic pressing) can significantly reduce porosity by enhancing particle rearrangement and eliminating voids. Pressure-assisted sintering is particularly effective for materials that are difficult to densify through conventional sintering methods.
- This method reduces sintering time and lowers the required sintering temperature, making it a powerful tool for achieving low-porosity materials.
-
Control Sintering Atmosphere:
- The sintering atmosphere (e.g., air, vacuum, or inert gases like argon or nitrogen) affects the sintering kinetics and final porosity. For example, a vacuum or inert atmosphere can prevent oxidation and promote better densification in certain materials.
- The choice of atmosphere depends on the material's reactivity and the desired properties of the final product.
-
Optimize Heating Rate:
- The heating rate influences the densification process. A slower heating rate allows for more uniform temperature distribution and better pore elimination, while a faster heating rate may lead to thermal gradients and incomplete densification.
- The optimal heating rate depends on the material and the sintering equipment used.
-
Improve Composition and Homogeneity:
- A homogeneous composition with minimal impurities promotes better sintering and reduces porosity. Impurities can act as barriers to diffusion and hinder pore elimination.
- Additives or dopants can sometimes be used to enhance sintering behavior and reduce porosity.
By carefully controlling these factors, it is possible to minimize porosity during sintering and produce materials with superior mechanical, thermal, and electrical properties. Each material system may require specific adjustments to achieve the desired results, but the principles outlined above provide a solid foundation for reducing porosity in sintered materials.
Summary Table:
Factor | Impact on Porosity Reduction |
---|---|
Initial Porosity | Lower initial porosity in green compact leads to denser final product. |
Sintering Temperature | Higher temperatures enhance atomic diffusion but must avoid excessive grain growth. |
Sintering Time | Longer times allow pore elimination but avoid over-sintering. |
Particle Size | Smaller particles increase densification and reduce diffusion distances. |
External Pressure | Pressure-assisted sintering (e.g., hot pressing) significantly reduces porosity. |
Sintering Atmosphere | Vacuum or inert gases prevent oxidation and promote densification. |
Heating Rate | Slower rates ensure uniform temperature distribution and better pore elimination. |
Composition & Homogeneity | Homogeneous materials with minimal impurities enhance sintering and reduce porosity. |
Ready to optimize your sintering process for denser, stronger materials? Contact our experts today for tailored solutions!