Determining when the temperature of a joint is hot enough to braze is a critical step in ensuring a strong and durable bond. Brazing requires the joint to reach a specific temperature range, typically between 450°C and 900°C, depending on the materials and filler metal used. The process involves heating the base metals to a temperature where the filler metal melts and flows into the joint by capillary action, but the base metals themselves do not melt. Achieving the correct temperature ensures proper wetting, bonding, and strength of the joint. Methods to determine the right temperature include visual cues, temperature indicators, and the use of thermocouples or infrared thermometers. Understanding the melting point of the filler metal and the thermal properties of the base metals is essential for successful brazing.
Key Points Explained:
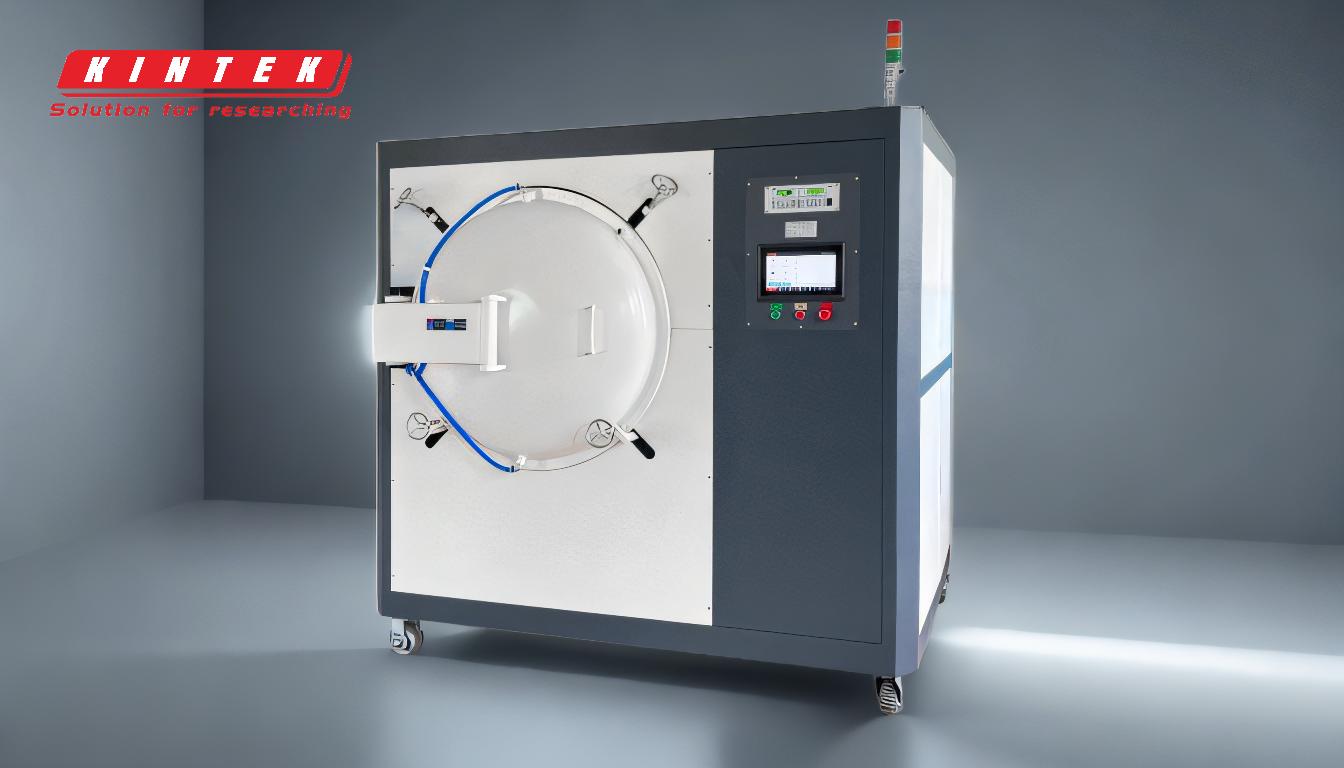
-
Understanding the Brazing Temperature Range:
- Brazing typically occurs at temperatures between 450°C and 900°C, depending on the materials and filler metal. The filler metal must melt and flow into the joint, but the base metals should not melt.
- The temperature range is determined by the melting point of the filler metal and the thermal properties of the base metals. For example, silver-based filler metals melt at lower temperatures compared to copper-based fillers.
-
Visual Cues for Temperature Determination:
- As the joint heats up, the filler metal will begin to melt and flow, which can often be observed visually. The filler metal will appear shiny and liquid when it reaches the correct temperature.
- The base metals may also change color as they heat up, providing an additional visual indicator. For instance, steel may turn a dull red at around 600°C.
-
Use of Temperature Indicators:
- Temperature-indicating sticks or pellets can be applied to the joint. These indicators melt at specific temperatures, providing a clear sign that the desired brazing temperature has been reached.
- This method is particularly useful for beginners or in situations where precise temperature control is challenging.
-
Thermocouples and Infrared Thermometers:
- Thermocouples are highly accurate tools that can be placed near the joint to measure the temperature directly. They provide real-time feedback, allowing for precise control of the heating process.
- Infrared thermometers can also be used to measure the surface temperature of the joint without direct contact, making them a convenient option for many applications.
-
Importance of Preheating:
- Preheating the base metals ensures that the entire joint reaches the required temperature uniformly. This step is crucial for preventing thermal stress and ensuring proper flow of the filler metal.
- Uneven heating can lead to weak joints or incomplete bonding, so preheating should be done gradually and evenly.
-
Monitoring the Filler Metal Flow:
- Once the joint reaches the correct temperature, the filler metal should flow smoothly into the joint by capillary action. If the filler metal does not flow properly, it may indicate that the temperature is either too low or too high.
- Proper flow is essential for creating a strong and durable bond, so careful monitoring is necessary.
-
Avoiding Overheating:
- Overheating the joint can cause the base metals to warp or oxidize, leading to a weak bond. It can also cause the filler metal to vaporize or burn off, resulting in a poor-quality joint.
- Maintaining the temperature within the recommended range is critical for achieving optimal results.
-
Post-Brazing Cooling:
- After brazing, the joint should be allowed to cool gradually to prevent thermal stress and cracking. Rapid cooling can weaken the bond and reduce the overall strength of the joint.
- Controlled cooling ensures that the filler metal solidifies properly and forms a strong bond with the base metals.
By following these steps and using the appropriate tools and techniques, you can accurately determine when the temperature of a joint is hot enough to braze, ensuring a high-quality and durable bond.
Summary Table:
Method | Description |
---|---|
Visual Cues | Observe filler metal flow and base metal color changes (e.g., steel turns red). |
Temperature Indicators | Use sticks or pellets that melt at specific temperatures. |
Thermocouples | Measure temperature directly near the joint for precise control. |
Infrared Thermometers | Measure surface temperature without direct contact. |
Preheating | Ensure uniform heating to prevent thermal stress and weak joints. |
Monitoring Filler Metal Flow | Ensure smooth flow into the joint for a strong bond. |
Avoid Overheating | Prevent warping, oxidation, or filler metal vaporization. |
Post-Brazing Cooling | Allow gradual cooling to prevent cracking and ensure bond strength. |
Need expert advice on brazing techniques? Contact us today for personalized guidance!